Flexible hones address surface roughness and increased dimensional changes for anodized cylinders that mate with other parts.
To permit the use of aluminum instead of other, heavier metals in industrial applications, many cylinders are anodized to create an extremely hard surface that is wear-resistant, corrosion resistant, non-conductive and lubricious. Because anodized surfaces are porous, they also improve adhesion of coatings as well as accept a variety of dyes for coloring.
THE ANODIZING PROCESS
Given the myriad of benefits, anodizing is popular for a variety of cylindrical items including lift mechanisms for chairs, lift cylinders for hatchbacks, shock absorbers and forks for bicycles, fuel pumps, water pumps, pneumatic and hydraulic cylinders, spool valves, valve stems and valve bodies.
By definition, however, the anodizing process means the parts grow dimensionally and increase in surface roughness.
For a cylinder, that includes both an increase to the outer diameter (OD) and decreases to the inner diameter (ID). There are several different types of anodizing methods, and each type or class reflects a range of coating thicknesses. As a rule, thicker coatings provide greater corrosion protection and, in harsh environments like salt air, this means longer-lasting surfaces.
As for surface finish, generally a hardcoat that is anodized to a .002 thickness will result in a Ra that is two to three times the original bare metal finish. For example, a machined Ra of 16 can easily become 30 Ra or more after anodizing.
For many parts, this is not an issue. However, when the part is cylindrical and mates with another part, often using a seal, increased dimensions and rougher surface finish can be problematic.
Anodic coatings are very hard (only slightly less than diamond and harder than hard chrome plating) and increased surface roughness can abrade sealing materials. Seal wear and coating irregularities can provide a path for leaks.
For this reason, parts require a fine surface finish for reliable sealing and long component life. To accomplish this, many are utilizing honing tools as an economical approach to treating the surface before or after the electrochemical process to control the dimensions and create a smoother surface.
The result is a cost-effective approach to resolving finishing challenges in the anodizing process to consistently yield high-quality products at a competitive price.
HONING TOOLS
Traditionally, manufacturers have used grinding, lapping, and rigid honing to improve the surface finish of anodized and hard-coat anodized parts. Machine setups are difficult, however, and they must be extremely precise. There are several reasons for this. First, the anodized coating is very hard. Second, the total coating thickness is very thin. Third, the high points and low points of the anodized coating are not absolutely symmetrical around the centerline of the cylinder ID.
When rigid honing is used with anodized parts, the honing stones only contact the coating’s high points. In other words, parts of the cylinder ID remain untouched.
There are other issues with rigid honing, too. Because anodized coatings are relatively thin, only a very small amount of material should be removed. Yet rigid honing works best with heavier cuts and greater material removal. Fine cuts combined with tool loading can contributed to smeared surfaces.
THE FLEX-HONE TOOL
The Flex-Hone Tool from Brush Research Manufacturing (Los Angeles, California) provides a better way to improve the surface finish of anodized and hard-coated cylinders.
With its unique construction, the Flex-Hone® is comprised of abrasive globules that are permanently laminated onto the ends of flexible nylon filaments. Because the diameter of the tool is greater than diameter of the bore, the Flex-Hone is used in an oversized condition and is self-centering, self-aligning, and self-compensating for wear.
Importantly, the Flex-Hone tool’s abrasive globules “float” to ensure that all parts of the bore—and not just the high spots—are surface finished. Unlike rigid honing machines, Flex-Hone setups are simple, too. Surface finishes can be improved with just a few strokes of the tool and the results are consistent.
The Flex-Hone Tools can be used prior to anodizing to control the size in anticipation of the shrinkage in ID. Honing also removes “fuzz,” sharp edges and any amorphous material that might adhere to the surface and affect the quality of the anodizing.
The most common usage for the honing tool, however, is after anodizing to correct unanticipated size and surface finish issues. When the quality of the final anodized finish is of the utmost importance, some even use the tool before and after.
With anodized coatings, the recommended abrasive types are aluminum oxide (400, 600, or 800 grits) and levigated alumina (extra fine only). Choice of grit depends on the type and thickness of the anodized coating and the final surface-finish specification. Flexible honing tools are available in sizes ranging from 4 millimeters to 36 inches.
ABOUT THE AUTHOR
Jeff Elliott is a Torrance, California, based technical writer. He has researched and written about industrial technologies and issues for the past twenty years. Brush Research Manufacturing is a privately-owned company located in Los Angeles, California, solving difficult finishing problems with brushing technology since 1958. Brush Research was one of the first companies to advocate the critical need for finer surface finishes to optimize performance. Concepts such as plateau finishing were pioneered by our founder, Steve Rands, and are now commonplace goals across many industries. For more information, call 323.261.2193, email info@brushresearch.com, or visit www.brushresearch.com.
MODERN PUMPING TODAY, May 2019
Did you enjoy this article?
Subscribe to the FREE Digital Edition of Modern Pumping Today Magazine!
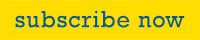