By Rob Martindale, Watson-Marlow Fluid Technology Group
The importance of water cannot be underestimated, and consequently all mines must carefully assess the impact of mining on local and regional water quantity and quality in order to retain a social license to operate. With this in mind, best practice water management defines credibility for the mining industry while negating the potential impact of additional costs.
In a paper prepared for the International Council on Mining and Metals, it was suggested that water access, quality, use, and environmental impact directly affect the ability of the industry to operate worldwide. Despite these challenges, mine operators face ever increasing obligations to reduce water consumption.
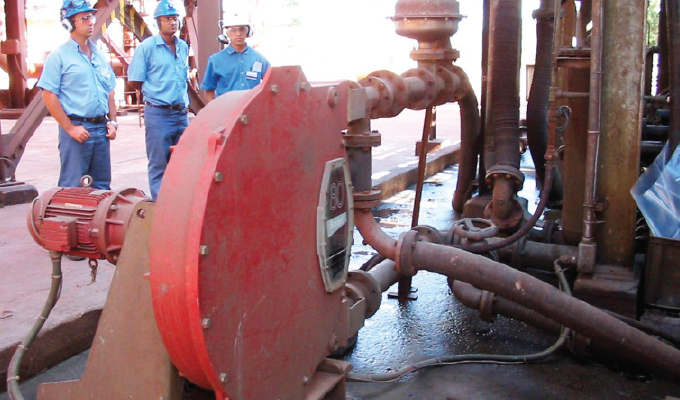
LESS WATER EQUALS FEWER COSTS
Among the key drivers for water reduction and greater water re-use in the mining sector are:
- Environmental responsibility. For instance, the Pascau Lama project on the Chilean-Argentinean border was delayed by a decade because of possible environmental impact.
- The limited availability of water at mines located in desert areas or at altitude.
- Increasing price of water.
- Intake water needs to be conditioned i.e. alum dosing, pH control, etc.
- Effluent water of operation needs to be treated.
In order to increase production and, at the same time, minimize rising costs, companies need to optimize their mining procedures.
The less time a mine requires to pump, add, or remove water in the course of processes translates into reduced operating costs. However, the relationship between maintaining a reliable supply of water to support mineral processing, and using as little water as possible in order to have the smallest volume on hand at any time, means that water inventories must be managed carefully.
Pumps have a vital role to play, and peristaltic pumps specifically can be considered water-saving devices, not simply because they accommodate very high solids-content materials found commonly in mining operations, but because they do not have seals they don’t require water for flushing, thus eliminating the requirements to both treat process wastewater or provide pump service water.
BENEFITS OF PERISTALTIC PUMP TECHNOLOGY FOR MINING APPLICATIONS
Peristaltic pumps supplied by Watson-Marlow Fluid Technology Group (WMFTG) can be considered as inherent metering pumps offering repeatability of 99.5 percent. Bredel hose pumps from WMFTG, for instance, accommodate continuous flow rates up to 28,500 gallons per hour and are extremely durable (pressures up to 16 bar). There are no internal universal joints, valves, dead corners, or glands to impact flow, and they are reversible for back-flushing.
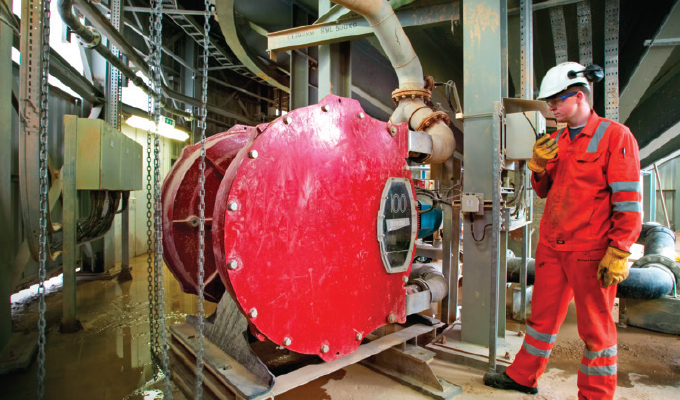
HANDLING THICKER SLURRY FLOWS
Although one main goal of mine operators is to use less water in the transportation process, doing so creates thicker, more paste-like slurries, which in turn creates other issues. More product can be transferred at lower velocities, but pumps and hoses must be designed to handle thicker flows.
Bredel hose pumps can handle undiluted tailings and thickener underflow up to 80 percent solids. No seal water flush systems, strainers, dampeners, in-line check valves, run-dry protection devices, or other ancillary equipment is needed. The entire family of pumps are self-priming to 29.5 feet, can run dry safely and can meter accurately to ±1 percent.
This innovative technology fits the demand for more efficient modes of high concentration slurry transport. The ultimate aim is to reduce water use, energy consumption, and capital costs, as well as improve slurry transport reliability by establishing a more fundamental understanding of slurry flow behavior and design.
OPTIMIZING THE TRANSFER OF PASTE BACKFILL
One of the most commonly pumped materials in mining operations is paste backfill, a cementitious composite that is similar to concrete. It consists primarily of mine tailings mixed with hydraulic binders, which are typically Portland cement and some form of supplementary cementing materials, and water.
Residues, slimes, or “tailings” are the materials left over after the process of separating the valuable fraction from the worthless fraction (gangue) of an ore or mineral.
Paste technology is introduced to make the backfill quicker, easier, and more cost effective to transport, deposit, and cure. The goal for the high density paste formulations is to produce a pumpable material that does not segregate when transferred—the fines content should be a minimum of 15 percent by weight of the paste. Naturally, choosing the right pump technology for the task is vital.
ACCOMMODATING HIGH SOLIDS CONTENT
Pumping applications in the mining sector frequently involve abrasive, corrosive, shear sensitive, and viscous liquid products. Solids such as rocks, sand, and ore comprise different mineral contents and pump systems must be able to accommodate these variations.
Mining slurries often feature sub-micron solid contents of 80 percent by weight, with specific gravity often greater than 2.0. In addition to offering abrasion resistant slurry pumping performance in arduous conditions for extended periods, pumps must be capable of high operating pressures and flow rates to ensure a smooth liquid passage and deny the opportunity for the product to settle.
Other features include repeatable and reliable flow, self-priming functionality, and low and easy maintenance. However, with so many pump types available it is little wonder mines frequently end up employing technology unsuitable for the task. Ultimately this leads to inefficiency and increased costs, typically due to excessive wear and downtime.
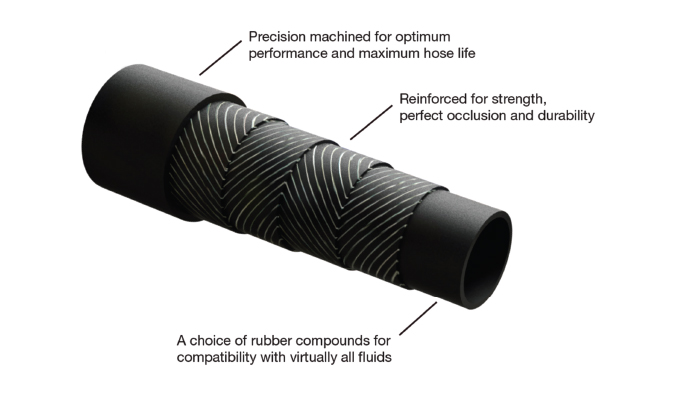
LIMITATIONS OF CENTRIFUGAL PUMPS
While centrifugal pumps have traditionally dominated the mining sector, particularly for operations such as thickener underflow applications, they are not without their shortcomings. For instance, the amount of dry solids that can be handled by centrifugal pumps is limited. In several applications, rotors or impellers on slurry pumps last only weeks and membrane pumps clog, leak, or fail due to factors such as strong acidity in a matter of months. Attempting to overcome these problems, some mine operators purchased highly expensive special pumps constructed from acid-resistant materials.
For these reasons peristaltic hose pumps are taking ever greater slices of market share. Among the many benefits of peristaltic hose pumps are:
- No mechanical seals.
- No requirement for seal gland water.
- No seal water flush systems.
- No moving parts in the product zone.
- Low and easy maintenance—just one wearing part: the hose.
- Almost all materials can be pumped, including slurries.
- Backflow and siphoning are prevented without the need for valves.
- Wear-free performance.
For the mining sector this last point is arguably the most advantageous. Obviously, the longer a pump can operate without maintenance or failure, the better. The wear-free performance of peristaltic pumps is an attribute that results from a unique operating principle. Unlike other pumps, the abrasive nature of the product has no bearing on pump life and the need for routine maintenance and spare parts is reduced greatly.
A LOOK AHEAD
The hose is at the heart of peristaltic operations, and in next month’s conclusion to this article, we’ll highlight its benefits as well as calculate savings of using a peristaltic hose pump over a rubber lined centrifugal pump.
FOR MORE INFORMATION
Watson-Marlow Fluid Technology Group (WMFTG) is the world leader in peristaltic pumps and associated fluid path technologies. The group comprises ten established brands, each with their own area of expertise. Together they provide leading engineering solutions across the food, pharmaceutical, chemical, and environmental industries. WMFTG is a wholly owned subsidiary of Spirax-Sarco Engineering PLC. For more information, visit www.wmftg.com.
MODERN PUMPING TODAY, May 2020
Did you enjoy this article?
Subscribe to the FREE Digital Edition of Modern Pumping Today Magazine!
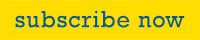