Today, critical processes in water, wastewater and irrigation activities jointly use more than 55 billion kilowatt-hours per year, according to estimates from the U.S. Department of Energy (DOE). In fact, it also is estimated that the water and wastewater treatment sector is the third largest energy consuming sector in the United States, accounting for approximately 3 to 4 percent of the country’s total annual electricity consumption.
THE PUSH TO EFFICIENCY
For U.S. municipalities, where more than 35 percent of total energy use is attributed to water and wastewater facilities, rising energy costs play a significant role in water and wastewater treatment services. At the same time, a plant’s ability to treat, use and deliver water efficiently—reducing water loss—also has a direct impact on the plant’s energy consumption and bottom line.
DOE estimates indicate that treatment plants could save 11 to 18 percent of annual energy consumption by improving system design, matching component size to system loads, motor efficiency upgrades and use of variable speed technology. By simply upgrading the efficiency of the plant’s motors, municipalities could save as much as two billion kilowatt hours per year. And, if these upgrades include the implementation of variable speed technology, an additional 3 to 10 billion kilowatt hours per year could be uncovered.
Energy and water efficiency, therefore, serve as a critical and powerful tools to reduce costs, enhance customer service and improve sustainability.
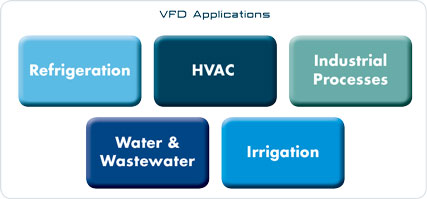
Use of VFDs extend across various applications, each with an increasing need for energy efficiency.
PROVEN TECHNOLOGIES FOR EFFICIENCY TODAY
For both new plant designs and retrofit projects, there are two technology paths that can be pursued to address energy and water use: new “innovative and alternative” technologies and accepted “innovative and alternative” technologies. These accepted technologies offer proven value to an application, including established design standards and ready adaptability. Plus, accepted technologies often already have the required EPA and/or state approvals.
Proven energy-saving measures for water and wastewater include process adjustments, improvements to blower and pump sizing, intelligent pump control and motor efficiency upgrades. Furthermore, variable speed technology—through variable frequency drives, offers the simplest implementation and the greatest energy-saving potential.
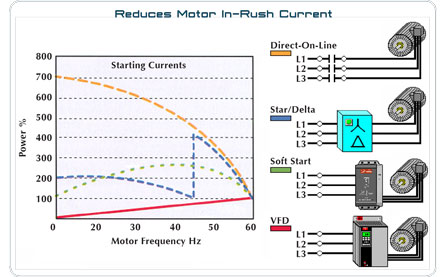
Reducing the in-rush current can help eliminate the damaging effects of high starting torque surges.
THE ROLE OF VFDS
Variable frequency drives (VFDs) serve as an intermediary between the electrical grid and a motor and reduce energy use by taking advantage of Affinity Laws—mathematical formulas that describe the relationship between speed and power. In rotating machinery, power consumption is directly proportional to the cube of speed, which means that reducing motor speed by just 20 percent could produce energy savings of nearly 50 percent. The fixed frequency electrical current supplied by the grid is varied by the VFD before it reaches the motor. The VFD thereby reduces the motor’s rotational speed to match the workload more precisely and reduce electricity consumption.
VFDs can also provide intelligent pump control via a cascade controller. Typically, the constant speed pumps used at water and wastewater treatment plants operate at maximum performance and efficiency for only a percentage of each day. However, a cascade controller can receive pressure feedback signals, stage on additional pump drives as required, provide a master speed reference signal to all pumps and ensure matched pressure and flow. This use of variable speed technology can help save water and wastewater treatment plants up to 20 percent on electrical costs and 30 percent on water usage annually.
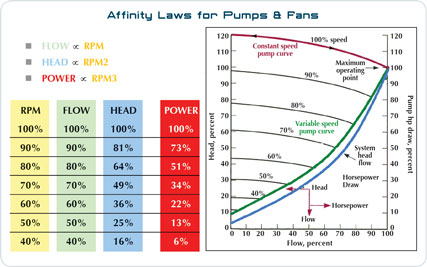
WASTEWATER ISSUES AND CONCERNS
For wastewater systems, in particular, variable frequency drives contribute to improved aeration control when incorporated as part of a systems approach that includes accurate, reliable input signals. A typical wastewater treatment plant can experience load fluctuations by as much as a factor of 5 over a 24-hour period, and manually controlling aeration can cause excess energy consumption by as much as 50 to 65 percent. A VFD, therefore, can cut energy use by 60 percent or more, compared to fixed speed operation in compressor applications.
As the wastewater treatment plant in Moundsville, West Virginia, can attest, variable frequency drive technology makes good financial sense. Originally, the plant was operating three 75-horsepower centrifugal blowers, two of which supplied air to four aeration basins with one blower unit as backup. The plant’s Dissolved Oxygen levels varied—from 0.5 ppm to 6.0 ppm throughout a 24-hour period. However, as part of a retrofit project, the plant installed one 100-horsepower and one 50-horsepower rotary lobe blower, each with a Danfoss VLT® AQUA Drive, which not only helped control dissolved oxygen levels by maintaining 2.2 ppm throughout the day, but also slashed annual energy costs by $50,000 to $60,000.
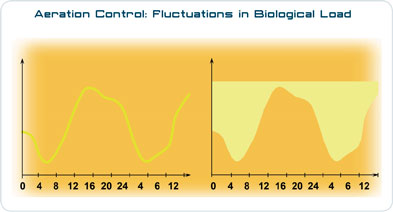
A typical wastewater treatment plant can experience load fluctuations as much as a factor of 5 over twenty-four hours of operation. Manually controlled aeration can cause excess energy consumption by as much as 50 to 65 percent.
THE INTERDEPENDENCY OF WATER AND ENERGY
Variable frequency drives can also address the interdependency of water and energy. In many countries, non-revenue water losses can exceed 30 percent. Not only is this water loss critical to the environment and sustainability, but energy is wasted pumping and treating lost water that ultimately does not make it to the consumer—and repairing holes or leaks is often costly and unrealistic. Constant pressure control schemes, like those assisted by variable frequency drives, however, can reduce these water losses through flow compensation. In fact, reducing pressure from 75 psi to 60 psi can save as much as 530,000 gallons per year through only one ½ inch (12.7 millimeter) leak in a water system. Multiply this by the probable hundreds of leaks in a typical distribution system and the savings potential is tremendous.
Yet, despite the proven results of these existing, highly effective technologies, deployment in the United States, where energy is relatively cheap, is still low. Municipal budget constraints, combined with first-cost investment challenges and a lack of financing models and incentives programs, as well as limited policy and regulatory mandates, are proving significant barriers to moving innovation forward. It is critical that the industry work together with policymakers to develop price signals, implement rebates and credits for retrofits and use standards, promotion and education to move these technologies forward.
It is only through the accelerated deployment of existing technologies that the highly efficient systems could be created to encourage the rapid deployment of future technology developments for the water, wastewater and irrigation sectors.
_______________________________________________________________________
ABOUT THE AUTHOR
John Masters is the vice president of sales for water for Danfoss, a world leader within energy-efficient and climate-friendly solutions for selected industries. For more information, visit www.danfoss.com.
_______________________________________________________________________
MODERN PUMPING TODAY, August 2013
Did you enjoy this article?
Subscribe to the FREE Digital Edition of Modern Pumping Today Magazine!
