Long-time SWPA member Jack Creamer, Schneider Electric’s market segment manager of pumping equipment, is a walking encyclopedia on the topic of maximizing the effective combination of submersible pumps and programmable logic controller (PLC) technology. Below, Creamer joins SWPA Executive Director Adam Stolberg in a conversation to share his wealth of knowledge and experience.
What are some of the benefits provided to submersible pumps from programmable logic controllers (PLCs)?
In short, better control and monitoring. The inclusion of a controller in pump application generally allows for the monitoring of multiple variables and their inclusion in the control routines. For example, a controller can monitor motor current, flow, and pressure and provide vital information regarding mechanical efficiency of the system over time.
How has PLC technology expanded the range of applications for submersible pumps?
PLC technology, due to providing system remote monitoring and intelligence capabilities, allows for increased applications due to their typically remote application. Both in the buildings and water/wastewater markets for example, remote monitoring and control adds great value. Reducing maintenance and downtime being two good examples.
How do PLCs add to the life-cycle cost benefits of submersible pumps?
A large part of life-cycle cost of a pump system is energy consumption. Energy consumption can be optimized based on better correlation between various data points including user usage behavior with scheduling features and current and power trending over time.
PLCs allow for data collection and logging. motor vitals such as current and power consumption over time and correlating it with pump flow and pressure allows for preventative maintenance activities to be performed before a system
The usage of multiple variables in control routines and preventative maintenance planning allows for optimization of costs in the lifecycle of a submersible pump.
How can PLCs allow submersible pump operators to achieve better efficiency?
A large component in increasing the efficiency of pump systems is achieved with variable frequency drives. The addition of a PLC allows for more advanced control and data logging features. PLCs allow for historical usage data to be logged and tracked over time. This gives system operators and end users better visibility of the health of a pump system and plan for maintenance activities preemptively.
What advice would you give pump users to get the most out of their PLCs?
Applying PLCs to pump applications allows for control sequences to be based on multiple variables. This could include motor electrical data, pump system pressure and flow data, and usage and maintenance planning. A benefit of including a multi-variate solution is to achieve higher efficiency in the life-cycle of a system.
MODERN PUMPING TODAY, July 2019
Did you enjoy this article?
Subscribe to the FREE Digital Edition of Modern Pumping Today Magazine!
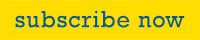