Makers of the world’s first chopper pump back in 1950, Landia has developed a unique chopping system of fixed and rotating hardened steel cutters that prevent the potential damage that would burden weaker pumps. As the following two case studies illustrate, the combination of Landia’s time-tested designs and innovative engineering have broadened the range of applications for which chopper pumps can provide solutions. Although chopper pumps may have once been thought of as specialized equipment for water and wastewater facilities, today’s pump users are increasingly turning to chopper pumps for their needs.
CASE 1: PUMPS AND MIXERS ROCK
Chopper pumps and mixers made by Landia have completed nearly ten years of service at the Rockwool manufacturing plant near Bridgend in South Wales, where stone wool is produced at the company’s state-of- the-art line and packaging facility. Rockwool is the world’s largest producer of stone wool insulation and the second largest insulation producer globally.
The stone wool at Bridgend is filtered from the collected process water, as Rockwool’s maintenance manager, Jeff Thomas, explains, “The stone wool manufacturing process resembles a giant candy floss machine, with Landia’s mixers keeping the dust in suspension, whilst the chopper pumps then send the wastewater away.”
THOROUGH AND DEPENDABLE
Serving two production lines, Landia’s 7.5 kilowatt DG chopper pumps and 2.2 kilowatt 300 revolutions per minute POP-I mixers are located in a reclamation unit underneath two large towers, reclaiming every last speck of dust and drop of water.
Thomas adds, “We make and supply a full range of smart and sustainable insulation products for the construction industry, based on innovative stone wool technology, so we don’t want breakdowns and downtime. The Landia equipment has always worked fine and been very reliable in what is a very tough application, especially for pumps.”
CASE 2: SAND IN THE SLURRY IS NO PROBLEM
Alice and Jens Munk operate a dairy farm in Denmark’s North Jutland County. The farm is home to around 290 acres of pasture and corn, over three hundred head of cattle, and—until recently—one recurring pumping problem.
The Munks believe that each cow should have an individual milking stall, confident that it improves the welfare of the cows. The farm’s milk yield was within the range of 22,000 pounds (10,000 kilograms) of energy corrected milk (ECM).
“It was very labor intensive,” Jens Munk offers. “The plan is that there must be 100 heifers home on the property along with the milking cows. The remaining heifers must be on the neighboring property, as is the case now.”
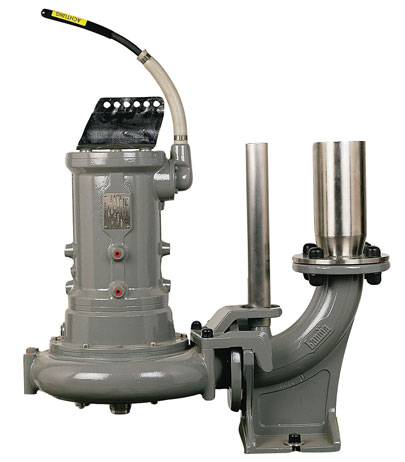
Landia high pressure pump type DG H
SAND IN THE SLURRY
The new pens at the Munks’ farm have 385 stalls, and the bottom of each stall is made of sand, which has a reputation for making manure handling difficult. The passageways consist of a solid floor of concrete, over which runs a scraper.
Below the floor is a series of cross-channels to the edge of the stalls, which—during stall cleaning—slows down the flow in order to avoid the disaster of a liquid manure tsunami. There are two cross channels 98.4 feet (30 meters) apart. In addition, there is a transverse channel at one end of the housing. The cross channels are V-shaped, and each cross-channel has its own pump with a stirrer. The combination of cow manure, sand, water, and cleaning solutions results in a thick slurry headed for the farm’s reception tank system.
“We have chosen to get all the sand in the slurry tank and, therefore, do not want it to settle in the reception tank,” says Munk. “The main tank requires more agitation, as the slurry from two smaller tanks flows straight in and from the main tank slurry is pumped into the slurry tank.”
There were some problems in the beginning because the slurry in the reception tank could not be pushed up when the flow exceeded certain levels.
A BOOST TO THE SYSTEM
To remedy the situations, Landia installed a chopper pump to serve as a booster. For every 9.8 to 13.1 feet (3 to 4 meters) of stalls, there were also drains placed to en sure the floor is kept dry. The improved system was even more efficient than expected. In the beginning, the drains were too small and clogged with sand and therefore need to be cleaned.
“We initiate two cleaning cycles every fourteen days and expel about 66 tons (60 tonnes) in two weeks,” says Munk. “The sand could be difficult to keep clean so it is a demanding job. If the stalls stay wet, it would lead to dirty cows. However, our cows have become cleaner overall—even cows that come from neighboring barns have managed to be comfortable in the stalls right away.”
HIGH PRESSURE SUBMERSIBLE SLURRY PUMP
Landia’s DG chopper pump operates at high pressure and is ideally suited for long distance pumping of raw and thick slurry. Its unique knife system eliminates clogging risks and ensures comminution of coarse solid parts, which makes the DG especially suited for the pumping of heavily contaminated and thickened liquids with a high dry matter content.
Features of the DG pump include:
- Specially designed impeller for difficult mediums
- Guide traces in the pump casing ensure that no dry matter parts will be ”caught” in the pump
- Horizontal or vertical mounting
- Motor sizes from 2.2 to 30.0 kilowatts, protection class IP 68
- Chopping system adjusted to medium and process requirements
- Impeller can be adjusted to constant head
- Available with equipment for mounting in existing installation
- Available with explosion-proof motor
- Available with lifting equipment for easy maintenance
Along with numerous application possibilities in agriculture and industry like the ones illustrated above, Landia’s DG pumps are also reliable pumps for biogas applications. In fact, as chopper pumps continue to be used across different markets and return with continued success, pump users will continue to find innovative uses for these reliable and powerful machines.
_______________________________________________________________________
ABOUT THE AUTHOR
Soren Rasmussen is sales manager at Landia Inc., the U.S. subsidiary of Landia A/S. With a background in mechanical engineering, Soren’s career at Landia now stretches back over a decade, during which time he has been instrumental in establishing the Landia brand in the United States and Canada. For more information about Landia’s range of applications, call 919.466.0603 or visit www.landiaworld.com.
_______________________________________________________________________
MODERN PUMPING TODAY, August 2013
Did you enjoy this article?
Subscribe to the FREE Digital Edition of Modern Pumping Today Magazine!
