The support bearings of literally millions of machines are located at or near the ends of the shafts so supported. However, design, configuration constraints or simple economics often preclude these support bearings from being fixed or rigid in the sense of being totally in line with each other. Alignment flexibility is therefore needed in shaft systems where one bearing support is exposed to a temperature different from the other support. In other words, thermal expansion may make it difficult for housing bores at opposite ends to remain truly in line.
UNDERSTANDING PILLOW BLOCKS
That’s why and where pillow blocks are often used (see figure1). Occasionally called plummer blocks in the English technical literature, pillow blocks typically incorporate a spherical double-row ball or roller bearing. Pillow blocks are widely used on conveyor guides and support rolls, paper machine rotors, mining equipment, furnace fans, centrifugal blowers, cooling tower fan gear drive shafts, and so forth. Depending on size and service parameters, the bearings are lubricated either by oil mist, grease, or liquid oil.
Pairs of suitable oil seals are generally integrated in a pillow block; they serve to prevent both ingress of contaminant and egress of the lubricant. By thus keeping the bearings supplied with clean oil, well-engineered bearing protector seals can multiply equipment life.
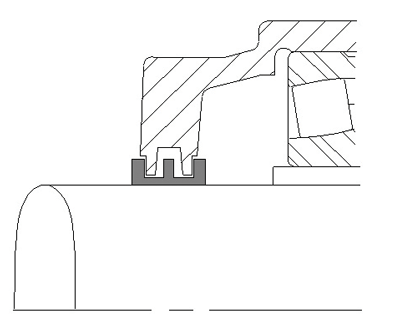
Figure 2: Pillow block segment showing non-contacting labyrinth-type bearing protector seal.
DISTINCTIONS AMONG BEARING PROTECTOR SEALS
Bearing protector seals generally fall into two main categories: non-contacting and contacting. Non-contacting bearing protectors can be of repeller or labyrinth configuration (see figure 2). By definition, non-contacting implies a relatively large, approximately 0.001 to 0.01 inches (0.025 to 0.25 millimeters) radial air gap between rotating and stationary sealing components. Smaller air gaps are more desirable than larger air gaps; the smaller gaps are typically found in more advanced rotating labyrinth seals.
Although qualifying for the designation non-contacting, many of these bearing housing seals incorporate elastomer rings that will contact at standstill and warm-up (run-up to operating) speeds. This is of importance because contacting parts must be designed to minimize component wear. Non-contacting seals designed to minimize component wear are a relatively recent development and have first been marketed in late 2005.
Non-Contacting Bearing Protector
In a non-contacting bearing protector, the rotating component typically has a complex outer profile which is located adjacent and in close radial and axial proximity to the complex inner profile of a stationary component. Together, these complex profiles, in theory, provide a tortuous path preventing the inward or outward passage of the unwanted materials or fluids. Unfortunately, the effectiveness of plain labyrinth seals is rather limited and does not sufficiently discourage fluid migration. This is especially so in pillow block applications where shaft angularity must be expected between the shaft and the housing.
Contacting Face Seals
In the second category, i.e. contacting face seals, industry has for many decades employed a number of bearing protector geometries. Commencing with many decades of lip seal experience, contacting geometries have progressed to technically advanced dual-face magnetic seals (see figure 3), with the latter finding acceptance by truly reliability-focused users. Until early 2006, however, neither the basic lip seal nor the dual-face bearing protector had been designed with shaft misalignment in mind.
The latest development in bearing protector seals takes care of all reasonable misalignment concerns on pillow blocks. As can be seen from figure 4, the new spherical contour design allows protector seals to adjust. Either contacting or non-contacting bearing protector configurations will now accommodate angular shaft-to-housing misalignment while fully permitting the effective sealing of the bearing lubricant space.
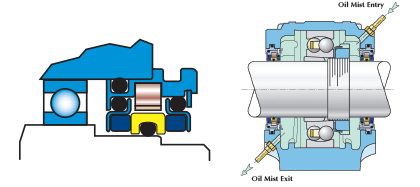
Figure 3: Dual-face (contacting) magnetic bearing protector seal and applied in pillow block arranged for oil mist lubrication (source: AESSEAL plc, UK, and Knoxville, TN).
OLD STYLE BEARING PROTECTOR SEALS VS. NEWLY ENGINEERED CONFIGURATIONS FOR PILLOW BLOCKS
Over the years there have been inventions incorporating two elastomeric members located on either side of a projection from a carrier. The elastomers are then held in place by a squeeze-fit against the sides of the split pillow block and the design relies on the relative elasticity of the elastomeric members to accommodate angular misalignment between the carrier and pillow block housing. These older style configurations use frictional drive rings on the rotating member connected to the shaft to force. The rotating member thus attempts to force the stationary carrier into alignment with the rotating shaft. This, then, raises technical issues for pillow blocks that merit our consideration:
- Expect wear between any frictional rings loosely located in a rotating component and making contact with the stationary carrier. The worn particles risk being dispersed adjacent and into the sealed bearing lubrication fluid. Whenever that happens, the contaminants degrade the lubrication medium and premature bearing failure results.
- Suppose the elastomeric members are resiliently mounted between the carrier and pillow block housing when the equipment is aligned. Forced into misalignment, one of the two elastomeric members will compress over part of its periphery whereas the compression on the second elastomer will be relieved over part of its periphery. Likewise, the compressive forces change at the remaining portions of the periphery of both elastomer components. This irregular circumferential compression force is transmitted through to the frictional rings, again accelerating the wear.
- All frictional contacting members positioned between two counter-rotating surfaces wear both the contacting member and often the surface of the rotor/stator as well. Frictional rings are thereby causing wear grooves in the shaft, leading to potentially expensive equipment repair cost outlays.
- The equipment shaft-to-housing is angularly rotated about the centerline of the bearing. With double spherical roller or ball bearings employed in spilt pillow blocks, the rolling elements are in angular motion. Any sealing member not rotating in the exact same plane is thus resisting the angular motion. Hence, there is further wear and potentially accelerated deterioration of both bearing and equipment.
Because they are equipped with an engineered self-aligning joint, the PB versions or “Pillow Block Models” of either the latest generation dual-face magnetic bearing protector seals (see figure 3) or the dual-dynamic O-ring bearing protector seals shown in figure 4 are able to avoid all of these issues. In each case and as long as the self-aligning joint feature is chosen, the elastomers are subjected to uniform, constant squeeze forces or pressures. There is no spring-like force on the stator trying to push it back into a position perpendicular to the housing face.
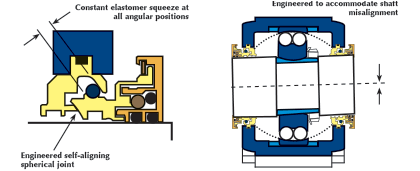
Figure 4: Advanced non-contacting bearing housing protector seal for pillow block, shown in aligned (a) and misaligned positions (b) (source: AESSEAL plc, UK and Knoxville, TN).
KNOW HOW TO PROTECT YOUR PILLOW BLOCKS!
By way of recap, the purpose of a bearing protector seal is to prevent the ingress of fluid, solids and/or debris into a bearing chamber. Likewise, bearing protector seals are used to prevent the egress of fluid or solids from a bearing chamber. Reliability-focused users go to great length to prevent premature bearing failure. They can now also rely on two different styles of well-engineered bearing protectors that fully accommodate the inevitably occurring shaft misalignment on pillow blocks.
_______________________________________________________________________
ABOUT THE AUTHOR
Heinz P. Bloch, P.E., is one of the world’s most recognized experts in machine reliability and has served as a founding member of the board of the Texas A&M University’s International Pump Users’ Symposium. He is a Life Fellow of the ASME, in addition to having maintained his registration as a Professional Engineer in both New Jersey and Texas for several straight decades. As a consultant, Mr. Bloch is world-renowned and value-adding. He can be contacted at heinzpbloch@gmail.com.
_______________________________________________________________________
MODERN PUMPING TODAY, July 2013
Did you enjoy this article?
Subscribe to the FREE Digital Edition of Modern Pumping Today Magazine!
