Being good stewards of natural resources like water and energy while still maintaining or even improving productivity is an ever-growing challenge for business owners and operators in search of sustainable solutions. That’s why high efficiency equipment has become a more viable option than ever. Specifying engineers across a variety of industries, including the mining, industrial, commercial, municipal and agricultural sectors, want to understand how high efficiency systems will work for their application needs. Will these systems not only deliver financial savings but also perform reliably with steady operation—using resources more intelligently without sacrificing equipment life, maintenance, and other operational concerns?
A growing solution for delivering higher efficiency with proven reliability is a pumping system built around a permanent magnet (PM) motor. PM motors are a proven technology many people use throughout their lives; automotive equipment, computer drives, vacuum cleaners and outdoor tools are just a few examples. The rotors inside PM motors are magnetized at all times due to the raw material selection and require no electrical power, making them more efficient—especially at reduced speeds and partial loads. PM motors operate more efficiently using rare earth magnets that perform with no slip. This translates into lower input power for the same output power, saving on operational costs every time the motor runs. In fact, running these in specific applications can provide energy savings that quickly offset additional initial investment costs. Motors with a 94 percent efficiency rating provide an investment payback of less than two years in most long- or continuous-run applications. This series takes a closer look at the benefits PM motors deliver in various applications.
LOWER OPERATIONAL COSTS AND INCREASED ENERGY SAVINGS
Energy used by induction motors to produce work can reach up to 97 percent of its lifetime cost, while the purchase price represents as low as 2 percent of its total cost of ownership (TCO). In contrast, a pumping system powered by a PM motor and optimized with a drive runs much more efficiently. This is especially true in a setting that requires continuous duty, where these savings can add up and will multiply over the years. PM motors run with an efficiency rate of up to 94 percent which is 10 to 12 points greater than a standard induction motor and delivers up to 21 percent energy savings when compared with its counterpart. The Hydraulic Institute rates the interior permanent magnet design as the best peak efficiency available when compared to any other motor constructions, including surface-mounted or even induction motors.
PM motors offer benefits whether the application requires constant or intermittent operation, since the PM rotor does not need to be magnetized. This concentrates all the power into motor shaft rotation for improved efficiency. Because of this power concentration, PM motor systems can run at a synchronous speed, providing improved hydraulic performance. With no slip, the motor speed is consistent and will not vary regardless of load.

LOWER OWNERSHIP COST CONSIDERATIONS
When looking for greater long-term savings and a lower total cost of ownership (TCO) over conventional systems, there are several other factors to consider that add to daily operating costs. In addition to the initial acquisition cost to purchase and transport the pumping system, TCO calculations for PM motors should include:
- Service costs per year: Service costs per hour times service hours per year.
- Downtime costs per year: Cost per downtime hour times downtime hours per year. Multiply each of the annual costs above by pump life span and add in the initial acquisition cost to calculate the TCO of a pumping system.
- Energy costs per year: To account for your system’s costs, consider the utilization of all components. Take the local cost per kilowatt-hour (kW/h) times hours of operation per day times the number of days the pump operates per year times the kW absorbed at duty point by the pump.
Here are examples of from our customers illustrating how permanent magnet technology can impact your energy costs per year and can deliver energy savings:
- A dairy application in Pickett, Wisconsin, relying on a 60-horsepower pump-motor assembly (PMA) that operates twelve hours a day for most of the year, can observe up to $3,500 in energy savings when its motor is replaced with permanent magnet technology design.
- Even with only eight-hour operation days, a 100-horsepower pump-motor assembly serving a municipal water system in Williamsburg, Virginia, achieves savings of up to $2,000 per year.
In the demanding mining market, a dewatering application in a mine site located in Parrish, Florida, requires a 175-horsepower submersible pumping set at depth of 2,000 feet. While their energy costs are slightly under the national average at only 10.0 c/kWh, their annual consumption can achieve energy savings of up to $4,000 in each well, if switched to a motor that leverages permanent magnet technology.
Many factors can improve return-on-investment (ROI) time, including energy consumption costs in the region. Additional considerations for cost savings include:
- Reduced startup/programming time. Select manufacturers have engineered their systems so that drives can easily be paired with a variety of motors in minutes—eliminating time wasted on programming.
- Reduced transportation costs. PM motors also feature a lighter and more compact size than standard induction systems, offering ease of installation while reducing freight and setup costs. In some cases, a more compact unit can be delivered to the jobsite quicker and more cost effectively.
- More efficient material selection. Select components have smaller size requirements. The system’s lower current means that specific components (like wire/cable and required VFD) might be smaller and less costly.
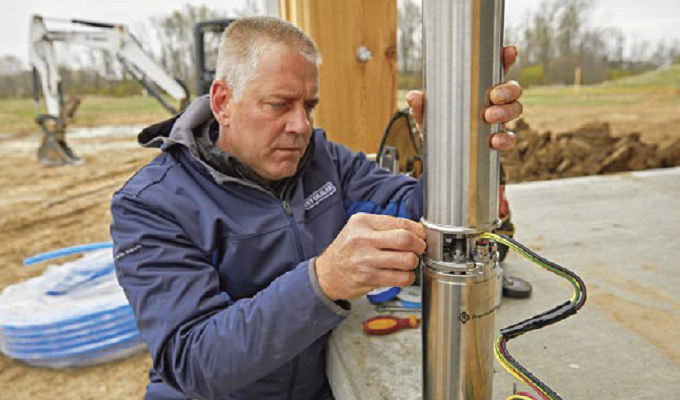
RELIABILITY
For any business using pumping equipment, reliability is critical. A more efficient pump is only as good as the consistent output it delivers. This is especially true in mining or municipal operations, where a down pump can have a catastrophic effect. PM motors in submersible pumping systems feature fewer moving parts as well as minimal aboveground components, which can mean easier initial installation and less scheduled maintenance down the road when compared to a vertical line shaft turbine installation.
When supplying water to homeowners and businesses, reliability equates to quality. PM motors should be National Sanitation Foundation/American National Standards Institute (NSF/ANSI) 61 certified and safe for drinking water systems to provide this peace of mind.
A LOOK AHEAD
In the second part of this series, we’ll expound upon more benefits PM motors can provide across different applications. When taken as a whole, the benefits of these efficient, reliable, and sturdy machines prove their value to pump operators time and time again.
FOR MORE INFORMATION
From groundwater to water treatment and more, Franklin Electric’s diverse product portfolio, combined with industry-leading technical support and service tools, helps save customers time and money. Franklin Electric is a global leader in the production and marketing of systems and components for the movement of water and energy. Recognized as a technical leader in its products and services, Franklin Electric serves customers around the world in residential, commercial, agricultural, industrial, municipal, and fueling applications. For more information, visit www.franklinwater.com.
MODERN PUMPING TODAY, October 2023
Did you enjoy this article?
Subscribe to the FREE Digital Edition of Modern Pumping Today Magazine!