On the website of tomato producer Guy & Wright, the company (established 1928) describes itself as “being complete idiots; building our own AD plant.”
Fifteen years ago, when the first 63,500-cubic-foot digester was built on the 100-acre site in Hertfordshire, England, John Jones (great grandson of the Guy half of Guy & Wright) could be forgiven for wondering what on earth he’d taken on. As if producing hundreds of tons of top-quality tomatoes each year wasn’t enough to think about, he was now coming to terms with that very steep biogas learning curve of feedstocks, temperatures and digestates.
A decade and a half on, with a second, 247,200-cubic-foot digester, no energy bills, and enough excess power to sell for the equivalent of 1,500 homes, Guy & Wright are a shining example of how to survive and thrive though diversification into renewable energy.
None of us could have predicted the sudden, massive leap in energy prices that are such a challenge today, but even in the early 2000s, rising fuel costs were already a big concern for John Jones. In the heat-thirsty production of tomatoes, he knew he had to act in order to protect and develop the family business.
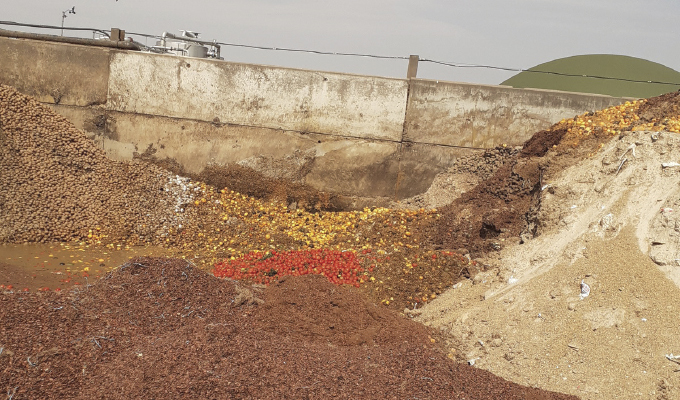
STARTING THE TRANSITION
At first, five natural-gas-powered 115kW micro-turbines were installed to produce hot water, electricity, and carbon dioxide. This process enabled Guy & Wright to apply for ROCs (renewable obligation certificates), which at the time, allowed generators of renewable energy to sell on and receive a premium, as well as the wholesale electricity price. But with those gas prices rising steeply, Guy & Wright soon reached the point of no return, investing in a 500kW CHP (combined heat and power) engine from Edina, converting three of the five turbines to run on biogas.
The investment in carefully-sourced equipment also saw the start of what has become a long and productive relationship with Börger; best known for its rotary lobe pumps, but also makers of key farming/biogas kit.
In 2008, a Börger Multi-crusher was put into operation to reduce feedstock particles down to 8 millimeters to enhance the anaerobic digestion process. One might expect there to be no shortage of waste from growing so many tomatoes, but John Jones’ son, Rob, who now runs the biogas operation, soon saw that tomato leaves were not only extremely difficult to break down but also low in calorific value.
MILKSHAKE CONSISTENCY’
So, as the never-ending fine-tuning of the AD plant continues, locally imported waste now includes citrus fruits, potatoes, grain and cocoa powder—plus processed DAF sludge from an ice cream manufacturer. This provides liquid to help create a “milkshake” consistency that the digesters will benefit from far more than a consistent supply of more solid material.
“The Börger Multi-crusher certainly proves itself as a very durable and effective piece of kit for the demands of an AD plant,” says Rob Jones. “We keep one Multi-crusher as a spare so that in any eventuality, we can keep operating—with two always on the go, plus an additional unit now on order. They work very well for us.”
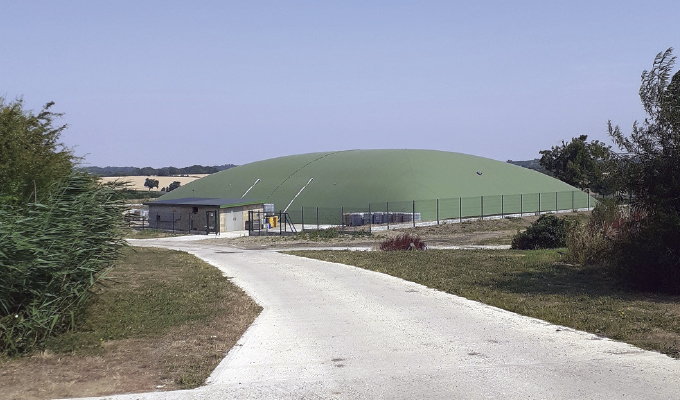
BUILT ON—AND FOR—SUCCESS
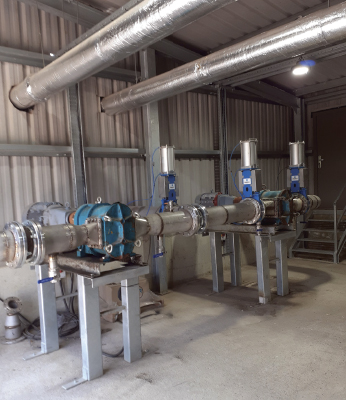
Based on the proven Börger Rotary Lobe Pump, the Multi-crusher chops coarse material to ensure that downstream machines and pumps operate smoothly. The Multi-crusher homogenies mediums at throughput volumes of up to 11,300 cubic feet per hour. In addition to food waste, it can handle fibers, pieces of wood, plastics, membranes, and textiles across a wide range of applications.
The team at Guy & Wright adds, “Investing in our first CHP was a real turning point, and as we’ve grown the biogas plant, converting (covering) our old lagoon into a secondary, 247,200-cubic-foot digester, we’ve not hesitated to invest in more Multi-crushers from Börger”.
The covered lagoon at Guy & Wright produces enough gas to run two of three CHP engines—and also provides retention times of up to six months, compared to most biogas plants where it is just thirty days. Every last bit of gas is extracted”.
Guy & Wright secured another Börger Multi-crusher when it began taking in liquid animal bi-products, for which they also needed a (7.5kW) Börger pump. Utilizing this type of byproduct (via a new pasteurizer) has provided another important string to the Guy & Wright bow, enhancing biogas yields by having a feedstock with a high calorific value and also less digestate to deal with.
Two biomass boilers are also now in the fleet of machinery, providing much-needed additional heat to the nursery during winter. Hot water is stored in a buffer tank so that it can be used on demand. Guy & Wright have also become the first company in the biogas industry to take exhaust gas from a CHP and convert it into carbon dioxide for the glasshouses. The gas is cleaned by a special system of catalyst bricks that absorb harmful gases; leaving the resulting carbon dioxide (which is piped into the glasshouses) at perfectly safe levels. This also aids the photosynthesis of the tomatoes, resulting in more plentiful flowers and fruits.
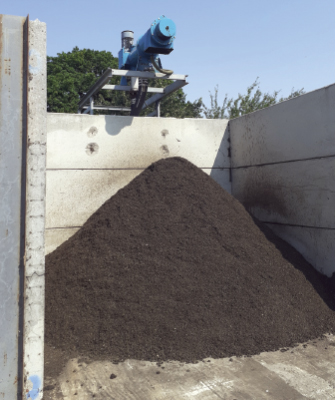
ADDING THE NEW BÖRGER SEPARATOR
Always looking for improvements, Guy & Wright turned to Börger again to address the dwindling capacity of the plant’s open lagoon. Working together with four nearby farms, there had been problems with blockages during spreading with an umbilical system, but that’s all changed for the better now, thanks to the purchase of a Börger Bioselect Separator.
Using a purely mechanical process, liquid is separated from solids in the medium, so that nutrient-rich (PAS 110-approved at a maximum of 2 millimeters) organic matter can go back to the land as a top-quality fertilizer. A combination of separation machine and two Börger Rotary Lobe Pumps, the Separator is load-triggered. The feed pump only conveys the volume that the Bioselect is able to process. The high-density solids discharge pump determines the degree of thickness.
“We no longer lose capacity in our lagoon,” concludes the team at Guy & Wright. “This is due totally to the Börger Separator, which protects it. Works an absolute treat.”
FOR MORE INFORMATION
Börger designs, produces, and sells pumps, chopping units, and entry technology for pumping low to highly viscous and abrasive media—including its core component, the patented Rotary Lobe Pump. Börger’s guiding principle has always been to make things better. In the meantime, Börger manufactures many other products. For more information, visit www.boerger.com.
MODERN PUMPING TODAY, December 2022
Did you enjoy this article?
Subscribe to the FREE Digital Edition of Modern Pumping Today Magazine!