The needs of fluid-handling operations are as varied as the kinds of liquids they handle. For those that mix fluids together, some might require small-batch blending while others need to mix large quantities. Some operations need only gentle mixing while others may require vigorous agitation.
Thankfully, there’s a piece of equipment that can step up to fulfill the needs of nearly any fluid-blending operation—the portable mixer.
Portable mixers come in a variety of shapes and sizes, with each model designed for specific applications. Properly designed and engineered mixers can provide the operator with many years of trouble-free service in a wide variety of blending or mixing operations. When configured and utilized properly, the right mixer can handle a number of important tasks, including suspending or dissolving solids, dispersing immiscible liquids, blending fluids of varying viscosities, and dispersing small amounts of gases in liquids.
So, how do you know what the right mixer is for your operation? This article will identify the variables that should be considered before choosing the mixer technology that will result in an optimized mixing or blending operation.
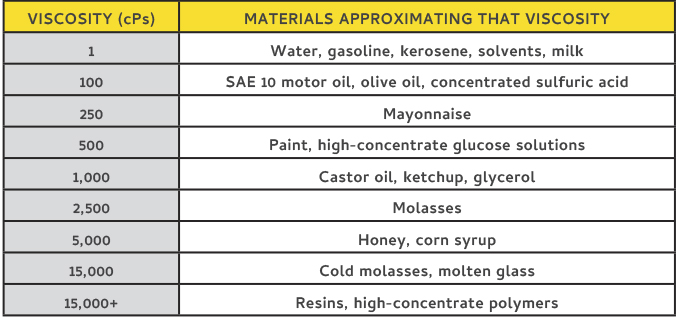
FLUID VISCOSITY
One of the first and most important things to consider when selecting a mixer is the viscosity of the liquids being handled. In fact, the type of mixer and its related components can only be selected once viscosities of the fluids are known.
Various mixers can handle commodities with viscosities ranging from 1 to more than 25,000 centipoise (cPs), including paints, varnishes, polymers, textile dyes, pharmaceuticals, food products, and soaps. Operators should keep the following information in mind when selecting the perfect mixer for the specific fluid type.
PORTABLE MIXER CATEGORIES
Once the viscosity of the fluid in question has been determined, the next consideration is the types of portable mixer categories.
Batch Size
For smaller mixing applications, the optimal style of portable mixer is lab and pail. Lab and pail mixers are best suited for, as their name suggests, mixing in small vessels for labs or industrial applications where a liquid product is provided in a pail. For industrial applications requiring larger containers or higher mixing speeds, drum and tote-tank mixers are the most commonly used. Tote (IBC containers) sizes can vary anywhere from 220 gallons to more than 500 gallons, whereas drum mixers are utilized with the 55-gallon drums in which many industrial chemicals are shipped. Most models of portable mixers are either gear-driven with speeds of 350 or 420 revolutions per minute (rpm), or direct-drive, with speeds of 1,750 rpm. Most can be fitted with variable-speed drives or air motors that can provide variable speed, if needed.
Mounting
The ideal mounting configuration varies depending on the application at hand. The three main types of mounting configurations for mixers are c-clamp, flange mount, and angle riser. C-clamp mounts normally feature an adjustable angle of entry controlled by a ball-and-socket design. Flange mounts attach to a flange that is located on the lid of the drum, tote, or bulk tank. Angle risers provide a fixed 10-degree angle of entry into the mixing vessel.
Props
Like mounting configurations, there are three common types of portable mixer propellers: 1.0 pitch, or marine prop; square pitch; and super pitch. A 1.0 pitch is one of the most effective pumping devices, while super pitch has a 1.5 pitch that delivers high pumping rates at the tradeoff of a higher horsepower requirement.
Shafts
Ideal shaft length is determined by the positioning of the mixer’s propellers. A good rule to follow is to position the mixer propellers 1 to 2 propeller diameters from the bottom of the tank (only position the prop 1 diameter from the bottom when mixing slurries or products with solids) to gauge shaft length.
MIXER AGITATION RATE
Different applications necessitate different agitation rates, so it is important to know the degree of agitation required. Agitation rates range from mild to violent, with tank turnover varying from 1/2 turns to more than 3 turns per minute.
- Mild: 1/2 to 1 tank turnover per minute.
- Medium: 1-1/2 to 2 tank turns per minute.
- Vigorous: 2-1/2 to 3 tank turns per minute.
- Violent: Greater than 3 tank turns per minute.
Consult with mixer manufacturers to determine the prop’s pumping rate for a specific model type and size at the various rpms at which they will operate. These rates are normally measured in gallons per minute of water pumped. Use this information to select the right agitation rate. For example, a 100-gallon tank of a water-like chemical requires vigorous agitation, or 2-1/2 turnovers. Knowing that a 4-inch square pitch prop at 1,750 rpm delivers a pumping rate of 250 gallons per minute, a portable mixer could be selected. Keep in mind, however, that as liquid viscosity increases the pumping rate decreases.
MIXER POSITIONING
The positioning of the shaft and prop within the mixer container is vital to enabling any portable mixer to blend, dissolve or disperse effectively.
In most mixing applications involving small cylindrical tanks of 1,000 gallons or less, the mixer is clamped to the side of the container. Effective mixing patterns will be achieved if the mixer is angled 10 to 15 degrees away from the vertical, either off-center or on-center. When mixing a slurry, angling the mixer 15 to 20 degrees off the tank’s centerline will result in good material turnover. On-center angling is better for gentler mixing and creates a vortex. Vortexing occurs when the contents of the tank swirl around the walls of the tank without much top-to-bottom turnover; this creates a less-efficient mixing operation and the possibility of uneven mixing or blending.
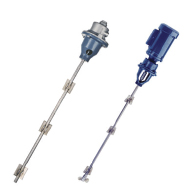
Cylindrical tanks with capacities of more than 1,000 gallons may require that the mixer be mounted directly in the center of the tank with the shaft in a vertical orientation. In this configuration, it is recommended that the operator put baffles on the walls of the tank in order to prevent the contents of the tank from turning in the direction of the mix, or creating an inefficient vortex. When this occurs, the mixing action in the tank will be poor.
Be advised, though, that the presence of vortexing during the mixing or blending process is not always detrimental. For example, creation of a vortex is desirable when solids or powders are added to the top of the batch, or liquids need to be drawn rapidly into the batch. The level of vortexing also becomes less severe with fluids that have higher viscosities.
CONCLUSION
It’s a fact that portable mixers play a key role in industrial manufacturing or fluid-handling applications. The right mixer can streamline any operation and provide operators with a consistent, hassle-free experience. By ensuring that you select the proper mixer for your specific situation, you can gain an important advantage toward optimizing any fluid mixing application.
FOR MORE INFORMATION
Eulis Ester is a product manager for Neptune®, a leading provider of reliable and safe handling of critical chemical fluids for water-treatment processes and agriculture applications. She can be reached at 909.222.1310 or eulis.ester@psgdover.com. Neptune is a product brand of PSG®, a Dover company. PSG is comprised of several leading pump companies, including Abaque®, All-Flo™, Almatec®, Blackmer®, Ebsray®, em-tec®, Griswold®, Hydro™, Mouvex®, Neptune®, Quantex™, Quattroflow®, RedScrew™, and Wilden®. For more information, visit www.psgdover.com/neptune.
MODERN PUMPING TODAY, August 2022
Did you enjoy this article?
Subscribe to the FREE Digital Edition of Modern Pumping Today Magazine!