Compatibility in any relationship, from marriage to roommate and rock group to dance troupe, is essential if that relationship has any chance of flourishing. A relationship that is not “compatible”—defined as “the ability to exist or occur together without conflict”—will soon reach its end as the parties learn that they are unable to co-exist effectively with each other.
The same principle holds true for the equipment and raw materials and finished end products that are used and produced in industrial-manufacturing applications. In this case, achieving compatibility is paramount when the fluids that are involved in the production process may be hazardous, corrosive, caustic, viscous, or particulate-laden. Specifically, industrial pumps—along with their wetted components—that are used for fluid-transfer processes must be fully compatible with the fluids being moved. Any incompatibility between the pump and the medium that it is tasked with transferring can potentially result in leaks or breakdowns that can compromise the production process, while also creating an unsafe working atmosphere for site personnel and the environment.
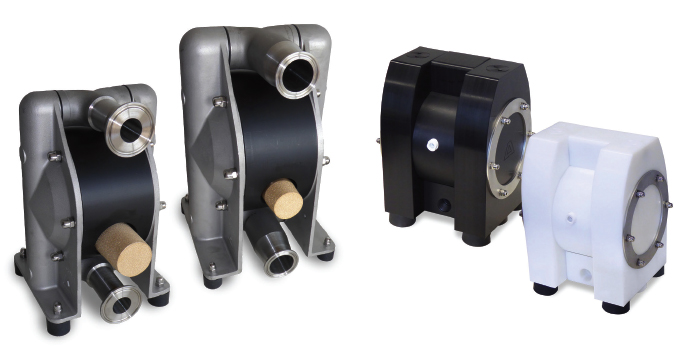
THE CASE FOR AODD PUMPS
Over the years, the use of positive displacement (PD) air-operated double-diaphragm (AODD) pumps in high-volume transfer operations with hazardous or corrosive high-value fluids has grown in popularity. The reasons are obvious: because of their utilitarian design, AODD pumps are highly flexible, reliable, durable, and resilient when used in even the toughest pumping environments. This is due to the fact their method of operation gives them the ability to self-prime, deadhead, and run dry with low shear, which allows them to immediately begin pumping when turned on and handle sensitive materials. Their seal-less design also virtually eliminates the risk of leaks developing, which makes them ideal for handling hazardous materials. As PD pumps, they are also able to quickly reach and maintain desired flow rates throughout the entire duration of the product run.
All of these features are making AODD pumps a first-choice option for general loading, unloading, and transfer operations in a wide range of industries, such as chemical processing, paints and coatings, food and beverage (including hygienic or sanitary applications), mining and dewatering, oil and gas, plating, lubrication and machinery, and semiconductor.
The true genius that makes AODD pumps perfect for use in such a wide array of industries and fluid-handling applications is in their simple design and highly repeatable method of operation. Operation begins when compressed air enters the pump through its air distribution system (ADS), which moves one of two diaphragms away from the center of the pump. Simultaneously, the second diaphragm is pulled toward the center by the shaft that connects both diaphragms. This creates a vacuum that forces the fluid into the inlet manifold, which lifts a valve ball off its seat. This enables the fluid to travel to the outlet where it is discharged into the piping. At this time, the ball valve reseats and the piston (diaphragm plate) pulls the diaphragm away from the center of the pump, allowing the other diaphragm to enable fluid to enter its half of the pump, from where it is discharged.
Knowing how AODD pumps function, it becomes obvious that the twin diaphragms play an indispensable role in ensuring proper operation. In other words, the diaphragms can be considered the “heart” of the AODD pump.
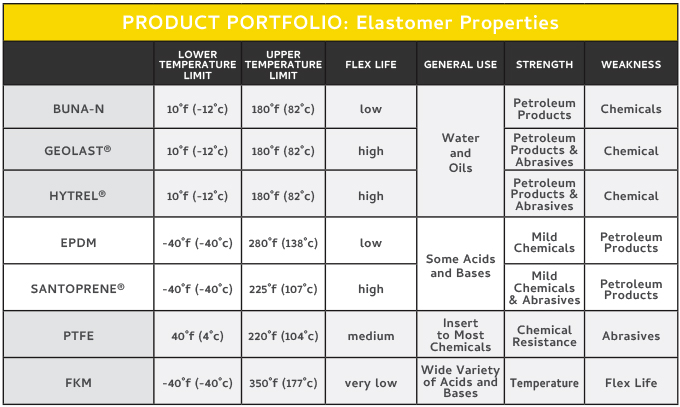
DOING DUE DIAPHRAGM DILIGENCE
So, facility operators cannot consider diaphragms as nothing more than throwaway parts for their AODD pumps. They must perform their due diligence in order to ensure that the diaphragms they outfit their pumps with are compatible (there’s that word again) with the fluids that will be handled. Not having accurate application information—most notably fluid properties and operational temperature—before outfitting an AODD pump makes selecting the proper diaphragm a challenge.
Since 1986, All-Flo has developed both metal and plastic AODD-pump models that have been engineered to provide reliable, trouble-free service in even the harshest pumping conditions. Regarding diaphragms, all All-Flo diaphragms are constructed of high-quality materials and their design, along with that of the diaphragm plates that hold them in place, enables them to produce reliable and repeatable performance.
All-Flo offers seven elastomer materials for its diaphragms, which gives the user a full range of options that can meet the specific needs of the liquid-transfer application. G series (right) and D series (left) pumps are available with single piece diaphragms (diaphragm and plate).
In general, the factors to consider when selecting a diaphragm include product characteristics, process temperature, application-specific requirements (i.e., FDA material of construction) and the diaphragm’s flex life. Another element to consider when selecting the diaphragm is the length of the stroke; some application/diaphragm combinations require a short-stroke pump configuration to ensure proper operation.
To aid its customers in finding the right diaphragm, All-Flo offers a complete seven-diaphragm portfolio that is available in rubber, thermoplastic elastomer (TPE), and polytetrafluoroethylene (PTFE) materials of construction. All have been engineered to be used in specific fluid-transfer applications based on the type of fluid that is being moved:
- Buna-N®: Buna-N, which is also referred to as “nitrile,” is a rubber compound that provides excellent performance in applications that involve petroleum-based fluids such as leaded gasoline, fuel oils, kerosene, and turpentine. Buna-N provides low to moderate flex life and moderate abrasion resistance.
- Ethylene propylene diene monomer (EPDM): EPDM rubber is an excellent choice for use in extremely cold temperatures or when pumping dilute acids or caustics. EPDM diaphragms are most commonly used in the manufacturing, food, pharmaceutical, and paint and coatings industries. Their flex life is lower than many other diaphragm materials, but they do exhibit good abrasion resistance. EPDM is also a good choice where statically dissipative materials are being handled.
- Fluoroelastomer (FKM): FKM is a rubber compound that uses vinylidene fluoride as its monomer, which allows it to be used with a wide variety of acids and bases. It does have very low flexibility, but can be the best choice in applications where fluid temperatures can reach upwards of 350 degrees Fahrenheit (177 degrees Celsius).
- Geolast®: Geolast is a TPE that exhibits enhanced oil-resistance and low oil swell, which makes it perfect for the handling of petroleum products. While equivalent to Buna-N in most of its characteristics, Geolast does offer a higher level of flexibility and good abrasion resistance, all at a lower cost than fabric-reinforced Buna-N.
- Hytrel®: Also a TPE, Hytrel delivers high flex life and excellent abrasion resistance. It also offers superior sealing or seal energizing due to its low compression set.
- Santoprene®: Another member of the TPE family, Santoprene is constructed of cured EPDM rubber, which helps make it ideal for use in various applications, including the transfer of acidic and caustic liquids. It also has excellent flex life, abrasion-resistance properties and a wide temperature range that makes it the go-to diaphragm in many chemical and industrial applications. Some Santoprene formulations can also be used in sanitary fluid-handling applications.
- PTFE: As an almost entirely chemically inert compound, PTFE can be used with a wide range of fluids. It is especially compatible with corrosive fluids such as aromatic or chlorinated hydrocarbons, acids, caustics, ketones, and acetates.
To further assist its end-user clients, All-Flo has created a Chemical Compatibility Chart that lists 907 materials that can be handled by an AODD pump and rates the level of compatibility (most compatible, minor effect, severe effect, and not compatible) with the seven different diaphragm materials.
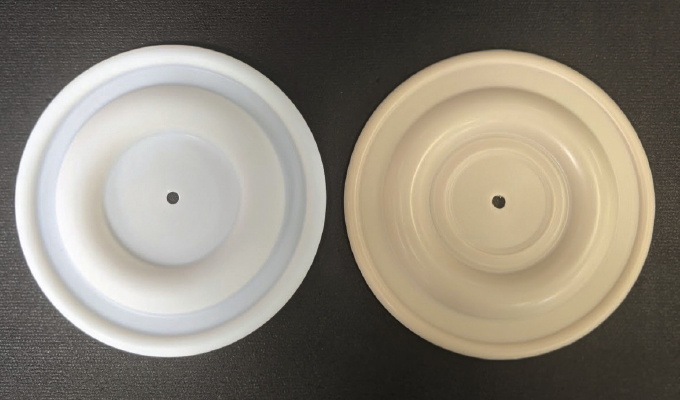
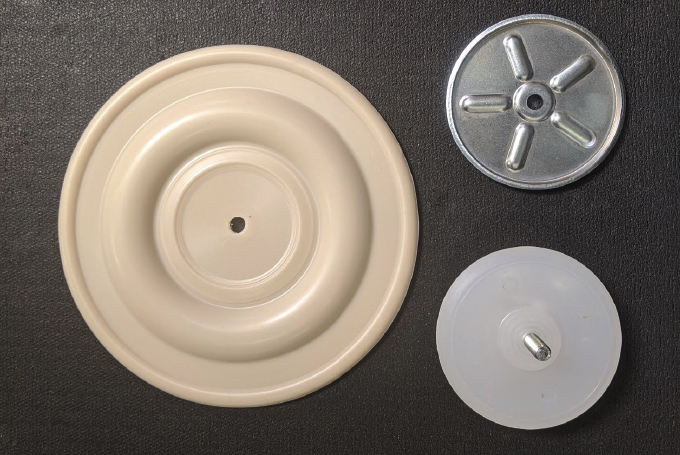
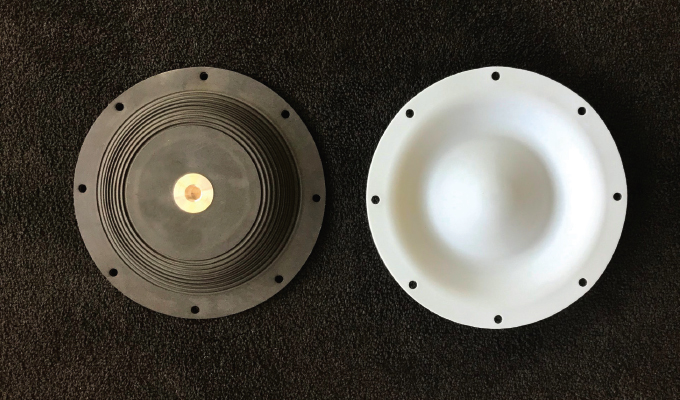
CONCLUSION
Whether pumping water, aggressive acids, food products, or solid-laden slurries, an AODD pump’s diaphragms must meet the needs of very specific handling characteristics as they relate to product compatibility. The challenge, in this case, is identifying and implementing the optimum diaphragm, one that will ensure safe, efficient, cost-effective, and trouble-free operation.
Choosing the correct diaphragm requires knowing and considering all of the process parameters. Because all of the parameters must work in perfect harmony in order to produce the best pumping solution, it is imperative that the user considers all options before settling on the diaphragm that will best optimize performance. This can be a daunting task for the uninitiated, so All-Flo offers assistance through its Chemical Compatibility Chart, which gives the user all of the information necessary to ensure that a chemically compatible diaphragm is chosen for the application in all instances.
FOR MORE INFORMATION
SAM GILBERT is a product manager for All-Flo, a leading manufacturer of air-operated double-diaphragm (AODD) pumps and fluid-handling solutions for industrial markets. He can be reached at samuel.gilbert@psgdover.com or 909.222.1319. All-Flo is a product brand of PSG®, a Dover company. PSG is comprised of several leading pump companies, including Abaque™, All-Flo, Almatec®, Blackmer®, Ebsray®, em-tec, Griswold®, Hydro Systems, Mouvex®, Neptune™, Quattroflow™, RedScrew™ and Wilden®. For more information, visit www.all-flo.com or www.psgdover.com.
MODERN PUMPING TODAY, February 2022
Did you enjoy this article?
Subscribe to the FREE Digital Edition of Modern Pumping Today Magazine!
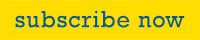