Although operating and maintaining a power plant remotely is an emerging challenge, remote operations support is not a new concept. Power plants have implemented evolving remote monitoring and diagnostics technologies over the past twenty-five years as they fight to stay reliable and competitive. The focus was on executing early-warning diagnostics using advanced analytics and enabling access to off-site technical expertise for troubleshooting and response.
While some peaking or renewable-energy plants with relatively simple systems are already operated remotely today, the COVID-19 pandemic and recent weather emergencies in the United States created challenges for many more sophisticated power plants. They exposed vulnerabilities that spurred a demand for more comprehensive remote O&M solutions. Now, in addition to improving reliability and competitiveness, there is added focus on safety and quality decision-making.
In a pandemic, plants want to minimize the number of people on site, including operators, but especially external staff required for executing inspections and maintenance. And, in some instances, it may not be possible for external staff to reach the plant. This exposed the importance of having more digital connectivity and accelerated the need to perform some level of remote operation and maintenance support, allowing reduced presence at the plant. In addition to safer operation during emergency situations, reducing the number of people coming on and off the site can provide cost savings, reduce delays and allow plants more flexibility as they cope with workforce challenges and budget concerns.
A pandemic may be the most dramatic example of an event that can cause disruption, but history contains other examples of severe weather events or civil and social unrest which gave rise to similar concerns.
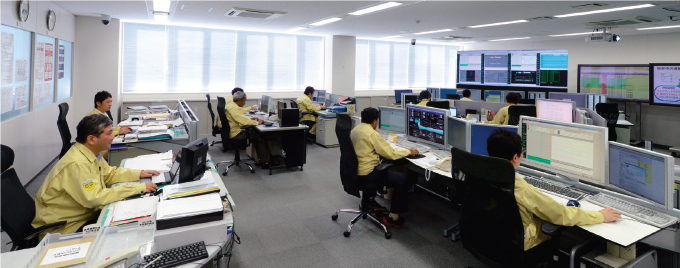
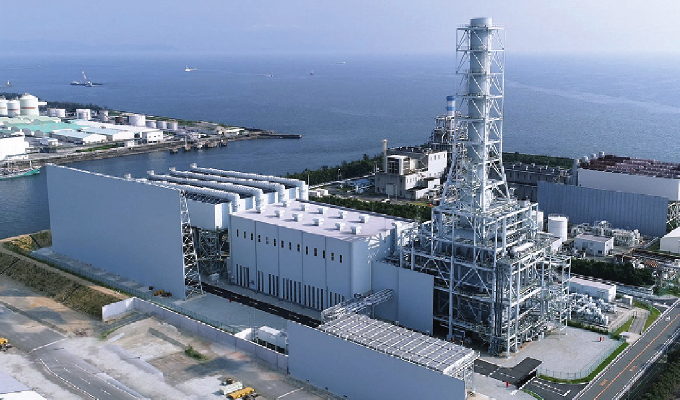
ADVANCED ANALYTICS: THE FOUNDATION
In 1999, Mitsubishi Power built the company’s first Remote Monitoring Center (RMC) in Takasago, Japan, and several others have followed. The RMCs allowed for the centralized collection and analysis of fleetwide data from power plants around the world and established the foundation for increasingly digitalized power plants. The RMC was the first step in the routine utilization of advanced analytics for power plants. Since then, digital solutions, like the growing Tomoni suite of intelligent solutions, allow plants to leverage the massive amounts of data from the thousands of sensors in the plant to provide insights, solve complex problems, and maximize overall power plant performance. Decades of experience gained from data analytics since 1999, throughout the fleet and on site at plants, have provided valuable lessons that lay the foundation for remote operation and increasingly automated maintenance, planning, and support, while facilitating the training and supervision of automated digital operations support solutions that utilize artificial intelligence (AI) and machine learning.
Mitsubishi Power’s Takasago Tomoni Hub and Orlando Tomoni Hub use integrated analytics to expand the O&M staff “virtually” by supporting the power plant with a team of experts on demand 24/7, 365 days a year. Additional support is provided by the Nagasaki Tomoni Hub in Japan, the Alabang Tomoni Hub in the Philippines, and the Duisburg Tomoni Hub in Germany. This allows for Mitsubishi Power engineers to troubleshoot and provide recommendations for operation and maintenance by utilizing the data from the plants to analyze, diagnose, and predict operational issues based on their expertise. Power plants around the world have benefited from remote monitoring and diagnostics for many years. Due to the nature of having a remote connection, an expert team can support multiple plants without ever going on site, especially during an emergency that complicates site access. In a crisis like the COVID-19 pandemic, the Tomoni Hub engineers can send settings updates to power plants by providing instructions and procedures for the on-site staff to implement. And, when a plant experiences unexpected issues, the Tomoni Hub can support it remotely. The team can also use the real-time data streaming from the plant to determine if there is the flexibility to move maintenance schedules to a better time by working with equipment and system designers co-located with the Tomoni Hubs to provide component-level risk assessments of maintenance deferral.
VALIDATION AT GRID-CONNECTED PLANTS
In addition to the progress in supporting remote O&M made through the Tomoni Hubs, significant advancement in the development of remote O&M technologies has been made and continues at the grid-connected power plants that Mitsubishi Power owns and operates. Located in Takasago, Japan, T-Point laid the groundwork for many of the Tomoni intelligent digital solutions of today, including remote operation. The new, digitally enhanced T-Point 2, which entered full commercial operation in July 2020, already incorporates technologies for remote operation and backup control rooms on its journey to becoming the first autonomous power plant. T-Point 2 will utilize a control room at the Takasago Tomoni Hub to validate the use of remote operation on an advanced-class gas turbine combined-cycle plant (GTCC) and its control systems through long-term remote operation. It is also validating several innovative concepts that automate plant operation tasks and leverage remote asset performance management technology throughout the plant and its balance of plant (BOP) to more effectively manage plant maintenance.
During the construction of T-Point 2, augmented reality was utilized for site walkthroughs and equipment placement via mixed-reality headsets. This new approach was used to validate the technology to qualify it for the ongoing maintenance of the plant. Being able to observe equipment condition and have real-time access to design documentation and remote expert assistance would enable inspections and outage scope definition with fewer people in person, while still providing abundant subject-matter expertise. This technology has subsequently been used to support outages at several customer-owned power plants, accelerating the use of these remote support technologies, and further refining them for broader adoption at plants around the world. This allows the best experts to support multiple issues at geographically separated plants without the lost productivity and potential schedule impacts associated with travel to one plant at a time.
Mitsubishi Power is providing total plant O&M for its own power plant at T-Point 2 and continues to gain invaluable experience in applying remote operation and maintenance technologies that are minimizing the need for on-site manpower and leveraging remote technical expertise on this fully integrated GTCC.
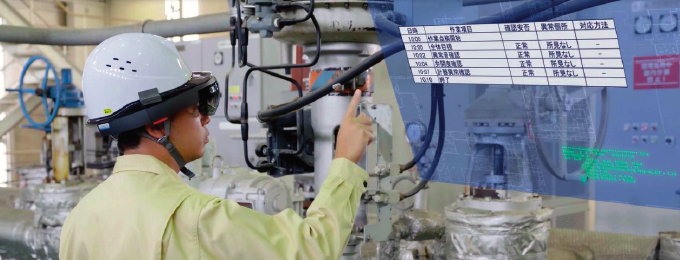
ADVANCEMENT THROUGH DIGITALIZATION
The key role of digitalization is to enable data visibility, data analytics, and automation that improve reliability and productivity, making power plants more profitable and resilient. Remote operation and maintenance support cannot exist without proper digital support tools in place. Digitalization is pivotal to advancing remote technology by reducing the need for a fully staffed, on-site workforce through automation and remote access to expert technical support. This will assist with a diminishing or less experienced workforce and managing crises that affect the workforce, while improving efficiency, increasing power plant competitiveness, and boosting income.
The first and foremost priority of any digitalization initiative is cybersecure communications and the protection of data flow. Power plants need a system that protects their ability to continue to reliably produce power and keep hackers out while automating the monthly maintenance of the control systems as much as humanly possible. For example, DIASYS Netmation is the Mitsubishi Power control system platform, and features such as the Netmation Secure Gateway and the Netmation Protect Pack, as well as the latest operating system upgrades, provide compliance with North America’s NERC-CIP, NIST Cybersecurity Framework, and other global requirements by providing server-level and client-level security. A global crisis like the COVID-19 pandemic can magnify cybersecurity and controls updating issues. Controls upgrades become even more important to keep a power plant protected at all times.
Once cybersecure connectivity is in place, the data flow enabled by digitalization makes data-driven condition-based maintenance and risk assessment of planned maintenance deferral possible. Such advanced maintenance planning is always valuable but is vital during emergencies. The option to safely postpone or eliminate a planned outage wouldn’t be possible without data-driven risk assessment and decision-making. Data from the plant allows engineers to predict when issues may occur and adjust to a revised condition-based maintenance schedule that can often accommodate outside factors like a global pandemic, weather disruption, or social unrest.
Enabling the automation of repetitive activities and record-keeping through digital solutions is an important step to shifting an operator’s focus to more imperative tasks that are more difficult to automate. Understanding the operator’s regular activities and the amount of time needed for execution will set the priorities for automated tasks. Combining automation with more focused on-site operators and remote support technology allows for a more effective on-site team to operate and maintain the plant.
Additional support to help on-site operators focus on things that only they can do effectively comes from the latest advances in digital control systems, such as the latest version of the Mitsubishi Power control platform, Netmation 4S. Among other advancements, “4S” self-performs continuous system diagnostics and adds capabilities for online logic simulation and loading, making on-site operators more productive and increasing opportunities for remote support.
Digital solutions to support on-site staffing, such as remote combustion tuning, have already proven beneficial during the COVID-19 pandemic. These solutions work through a secure gateway to access computers at the plant to see the logic, manipulate fuel fractions, move load, access the diagnostic monitoring system, and monitor emissions changes. Remote rotor balancing is also being performed at distant sites that are difficult to get to, through balancing monitoring software that enables expert balancing assessments to be made remotely. Critical activities like combustion tuning and balance weight calculations can now be accomplished by specialized subject-matter experts without requiring them to travel to the plant. It is also important to be able to remotely introduce control settings changes, software patches, logic modifications and other crucial updates. During the COVID-19 pandemic, which limited personnel on site to only those who are essential, the Tomoni Hubs were able to give procedures for controls updates to the on-site staff to manage the update and support any issues remotely.
The biggest advantage of providing remote O&M support is timing, even if there is not a major disruption taking place. With the travel component eliminated, technical experts can work with more plants in the same amount of time. Because of the importance of doing more O&M support remotely and expanding the reach of its technical expertise, Mitsubishi Power is focusing on additional technology development in this area.
One such development activity is the creation of a digital ecosystem that allows rapid digital access to the mass of important data related to the plant such as manuals, procedures, root cause analyses, key maintenance, and operational experience, as well as fleet experience of similar plants. This will provide further support to on-site O&M activities and help to fully leverage the benefits from remote operation and maintenance. This ecosystem includes an off-site data historian, cloud-based data, digital manuals, and inspection reports, in addition to the ability to quickly search for the appropriate document. Every day, all of these different data sources, many currently paper-based, are being accessed to make decisions. Not only will creating this digital ecosystem benefit remote technology, but it will also make the information more readily available on mobile devices, which could transform how business is done today. Without the digital ecosystem, full automation is not possible, as humans are relied on to seek out and manually input the information. Eliminating this repetitive task could free up a plant operator’s time and give them the right information to make better decisions on plant operation and maintenance.
FUTURE DIRECTION FOR TOTAL PLANT REMOTE OPERATION AND MAINTENANCE
While technology is well on its way to enabling remote operation and maintenance, some important steps are needed. Robust communications need to be in place beforehand, so off-site operators and subject-matter experts can help, making cybersecurity a prerequisite. Cybersecurity is an ever-changing issue that will need constant support and maintenance to ensure data and communication channels remain safe. A secure and stable connection will be critical as well. A loss in connectivity during remote support could cause major issues at the plant. Operating procedures will need to be implemented to ensure the best balance of remote and local operation, including backup strategies, as well as the best balance of automation and human intervention.
The biggest step needed is a real-time integration of all systems, including integrating and automating documentation and remote record searching. There needs to be an updated, centralized resource to document everything done in the past and the current settings throughout the power plant. This all-encompassing record of plant status and history will fuel AI-based O&M strategies and is critical to total plant automation. It can be used to build a virtual model of the plant. By documenting all changes in a virtual model, a plant can connect simulation tools to understand the result of changes before they are made at the plant. When there is an issue, like a trip, a virtual model reflecting total plant performance will allow subject-matter experts to determine and support rapid resolution without going on site.
The future holds a wealth of opportunities for making power plants smarter, better supported, and more resilient to disruptions such as global health emergencies, major weather events and social conflicts. Mitsubishi Power is committed to steadily applying the latest technological advances to make those opportunities a reality. At T-Point 2, Mitsubishi Power is validating the building blocks of the smarter power plant of the future, which will be capable of various levels of remote support and autonomy, and applying those building blocks to make existing and new power plants resilient and sustainable.
FOR MORE INFORMATION
Mitsubishi Power is leading the development of the smart power plant of the future with Tomoni, a suite of intelligent solutions enabled by decades of O&M and plant knowledge. Our solutions use advanced analytics and are driven by customer collaboration to deliver powerful financial and environmental advantages For more information, visit www.changeinpower.com/tomoni.
MODERN PUMPING TODAY, February 2022
Did you enjoy this article?
Subscribe to the FREE Digital Edition of Modern Pumping Today Magazine!
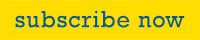