By Dave Eifert and Eike Wedekind, Phoenix Contact
Just a few years ago, it was extremely difficult to monitor and maintain distributed stations. The reason for this was that the remote systems were either unable to communicate with a control center, or communication involved a great deal of effort and expense.
Today, all installations in remote distribution and collection systems, such as water, gas, or electricity supply pipelines or even transportation technology applications, must be connected to a central control system. This allows smaller installations such as pumping stations, transformer stations, or transformer substations to be monitored and controlled remotely. This connection presents new challenges for the technology.
Remote control and remote maintenance have since become the established standard in communication. Remote systems or external stations can be easily connected to the control center using a wide range of telemetry methods. Standardized transmission is made easier thanks to defined, standardized protocols. The predictive maintenance, made possible as a result of this, enables huge cost savings.
But which communication method is best suited to the relevant application?
This article will provide the reader with a practical selection guide to the communication mechanisms and media for remote maintenance and remote control technology that are relevant to them.
DIFFERENCE BETWEEN REMOTE CONTROL AND REMOTE MAINTENANCE
In industrial communication, there is a vast difference between remote control and remote maintenance, even when using identical technology. This often leads to confusion when it comes to selecting the right communication media. The particular features of the different applications are described below.
Even predating all the talk about the industrial internet of things (IIoT), central control systems have been used to operate systems and machines in ever-more distant locations. In addition, the installed systems are constantly growing in complexity. This often leads to problems when needing to diagnose and correct errors in the event of a fault. In the event of a fault, there is much more to it than just remote maintenance. Thanks to developments in recent years, complete support and monitoring of the production process are now possible.
REMOTE CONTROL TECHNOLOGY
Continuous monitoring of important process data can be realized by using suitable remote control technology. System status is continuously displayed in the control center. The required logging of flow rates or liquid levels, for example, can be stored centrally for many years, in compliance with regulatory requirements. Thanks to special protocols, process data can be transmitted securely over wide area networks, even with low bandwidth and with poor transmission quality.
Communication used to be performed via dedicated wiring with discrete digital and analog signals. As processes became more complex, more information was needed from the process, and it was possible to process this information in control systems, the discrete lines were, in many cases, replaced by serial connections via permanent line modems. Stations that did not have dedicated permanent line connections were connected via analog dial-up connections, leased permanent lines, or wireless systems. More recently, cellular communication connections have been used. One of the disadvantages of dial-up connections is that there is no permanent connection to the control system and, as with voice telephony, connection establishment takes some time. Recently there has been a clear move away from serial transmission paths toward IP-based communication. Modern communication options such as Internet, VPN, cellular up to 5G are also integrated in remote control technology.
COMMUNICATION PROTOCOLS
There are specific protocols for every type of industrial communication. In factory automation, fieldbuses with defined transmission paths utilize one of several specific protocols optimized for the applications found in discrete manufacturing. Even the cables are often specified, and process information is usually exchanged cyclically, with very high determinism between the controller and I/O station, HMIs, and other nodes.
Another group of industrial protocols originates from the time of serial communication via permanent lines. These are mostly what are referred to as polling protocols. One example is the Modbus protocol, which is used worldwide.
A typical feature of this form of data exchange is that the control system polls each external station in a round-robin fashion. These communications are not deterministic—that is, it is not possible to predict how long it will take to poll any particular remote node, nor the entire system. Polling either only identifies changes or transmits all data points to the control system. However, in the event of a lost connection, it is impossible to later determine what happened at the external station during this time, or whether specific threshold values were exceeded. The advantage of these protocols is their easy parameterization. The disadvantage is the setup of time dependencies, which can be labor-intensive.
With the introduction of remote control technology and the associated expansion of systems, a new type of industrial protocol was needed. Previously, a physical connection was required between the control system and the external station, which limited the amount of data that could be sent. Over time, cellular communication networks have become more commonly used to connect external stations to the control system. As a result, it was no longer possible to use time-critical polling protocols.
Cellular communication networks are storage networks that can retain the individual data packets, which are then only reassembled again at the receiver. Once a connection has been established, the user no longer has to deal with data transmission. It is controlled by using TCP/IP, for example.
In certain geographic areas, cellular networks can experience intermittent outages. This behavior places new demands on a transmission protocol. It must provide internal security mechanisms to prevent data loss in the network.
BASIC REQUIREMENTS
A remote control protocol must feature the following in order to satisfy current requirements:
Bidirectional, Event-Oriented Transmission
It must be possible to send data to the external station and receive data from the external station simultaneously. For example, an external station must not be hindered by control system polling if it is transmitting an alarm message.
Storage of Process Information (In the Event of Connection Interruptions)
Some of the data in the processes is relevant for billing. Other data is just as critical for regulatory compliance. The data must not be lost as a result of a connection interruption and must be stored by the external station as historical data until it has been received by the control system.
Time Stamping of Process Information
For the control system to be able to reconstruct the data trend, the historical data must at least have an exact time stamp.
Time Synchronization
In order to reconstruct data trends using the time stamp, all of the system’s external stations must use the same time as the control system. A remote control protocol must therefore offer the option of synchronizing all devices in the system.
Serial Communication via Dedicated Permanent Cabling
In some systems, distributed system nodes are connected via the supplier’s dedicated permanent lines. One example is the connection of the remote pumping station to the central process control system. Serial communication is possible here because copper cables are traditionally installed along with the supply pipelines. With protocols according to IEC 60870-5-101 or IEEE 1815 (DNP3), for example, the system is equipped with communication standards that are established in remote control technology. This satisfies all requirements for secure remote control technology. In the event that the permanent line fails, the selected remote control protocol ensures that the data for a pumping station is stored in the remote control device.
Communication via TCP/IP (or UDP/IP) or Cables
If no dedicated cables are present, communication via a TCP protocol for networking distributed systems to the control system is a reliable method for data transmission. Protocols according to IEC
Depending on the protocol used, communication is event-oriented and prepared for the use of cellular-based hardware. In the event the communication infrastructure fails, the remote control protocol ensures that data is stored locally and automatically uploaded to the central control system once communications have been re-established.
Online Data
The process image data is read cyclically from the PLC and displayed in the control system via the OPC interface. Switching operations can also be performed from the control center.
Historical Data
Historical data is retrieved cyclically or in a user-controlled way. The time-stamped historical data is sorted in chronological order into *.csv files by the AX ODP server. The memory capacity in the PLC depends on the number of variables and the corresponding memory cycle.
Malfunctions, Alarms, and Messages
Malfunctions, alarms, and messages are transmitted to the control system by the substation in an event-oriented way. These can then be stored in chronological order and evaluated in the control system.
If the external stations are connected via the ODP server by means of GPRS, they can communicate with virtually any control system. In order to do this, the AX ODP server must be installed in the control center. The ODP server developed specifically for GPRS communication makes data for connection to the control system available via OPC. They are manufacturer-neutral and can communicate with every OPC-based control system.
REMOTE MAINTENANCE DISTINCT FROM REMOTE CONTROL
Remote maintenance describes remote access to a station for fault diagnostics or for maintenance purposes. This saves costs, as a technician does not have to be on site or travel long distances in order to return the system to operation. It also reduces downtime.
A LOOK AHEAD
In next month’s conclusion, we’ll examine the differing protocols for remote control as well as those not for remote control. Also, as cellular communication network and the Internet provide a solution for transmission over long distances and on a global scale, we’ll look over the history and future of these continuous connections.
FOR MORE INFORMATION
Phoenix Contact develops and manufactures industrial electrical and electronic technology products that power, protect, connect, and automate systems and equipment. Our products are used in many industries, including automotive, water/wastewater, machine building, power generation, oil and gas, and many others. For more information, visit www.phoenixcontact.com.
MODERN PUMPING TODAY, March 2021
Did you enjoy this article?
Subscribe to the FREE Digital Edition of Modern Pumping Today Magazine!
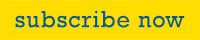