By Colin Guppy, Sundyne LLC
The chemical industry is an integral part of the global economy—contributing roughly $6 trillion annually, or almost 10 percent of the world’s GDP. Chemical Processing permeates thirty-four industries, and directly or indirectly supports more than 120 million jobs in fifty-eight countries.
The production of chemicals requires high volumes of liquids that need to be pumped around a plant. Most of these raw materials are harsh and hazardous in nature—presenting risks to the health and safety of plant personnel and the environment.
But every day, everyone touches items made from chemical processing. The food we eat, the water we drink, the buildings we live and work in, the vehicles that transport us, the medicines we consume, the energy we use for heating, cooling and lighting, and the packaging products that move goods from point A to B all require chemicals. Ten of the world’s most common chemical processing applications are:
- Chlor Alkali: for the production of chlorine and caustic soda
- Plastics: for bottles, packaging and thousands of other uses
- Polymers: for thousands of products, including batteries/fuel cells
- Pharmaceuticals: for drugs and biologics
- Purified Terephthalic Acid (PTA): for polyesterand clothing
- Acids: such as sulfuric, phosphoric and nitric
- Peroxides: for bleaching agents
- Ammonia and Urea: for fertilizers and hundreds of other products
- Insecticides: for agriculture
- Herbicides: for consumer products.
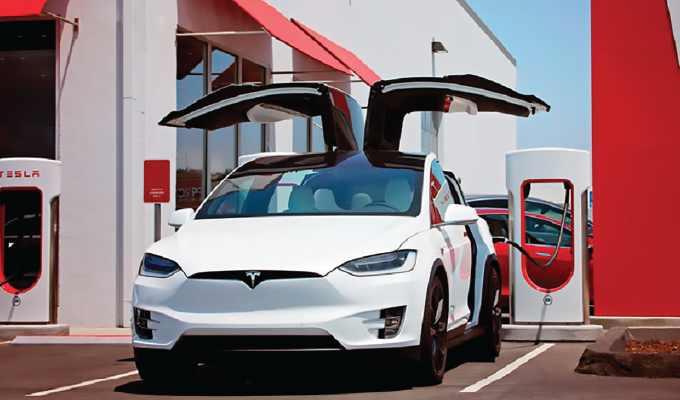
The Top 10 Advantages that Magnetic Drive Seal-less Pumps Offer Versus Sealed Designs:
- No seals or seal support systems
- Complete fluid containment
- Zero emissions
- Reduced installation costs
- Reduced maintenance costs
- Longer MTBF intervals
- Maintenance time/skills can be used elsewhere
- No EPA monitoring/documentation
- Improved operator safety
- Protection for the environment
WHY SEAL-LESS PUMPS ARE PREFERRED FOR CHEMICAL PROCESSING APPLICATIONS
Who should consider switching from sealed pumps to seal-less pumps? The answer includes any of the following:
- Applications with legislative and liability risk compliance
- Units needing to improve reliability
- Duties that are hard to seal
- Applications/fluids that react with moisture/air
- Any plant seeking to meet higher MTBF goals.
Operators that switch from sealed to seal-less pumps can realize a number of benefits, such as: eliminating the mechanical seal, which eliminates product leakage; reducing the pump’s footprint; minimizing (or eliminating) alignment issues; and each of these items results in a higher MTBF. From a cost perspective, switching to seal-less pumps reduces installation costs—because there are no seal support systems or utilities. It requires less instrumentation and it significantly reduces the amount of maintenance required over the life of the pump, resulting in a lower total cost of ownership.
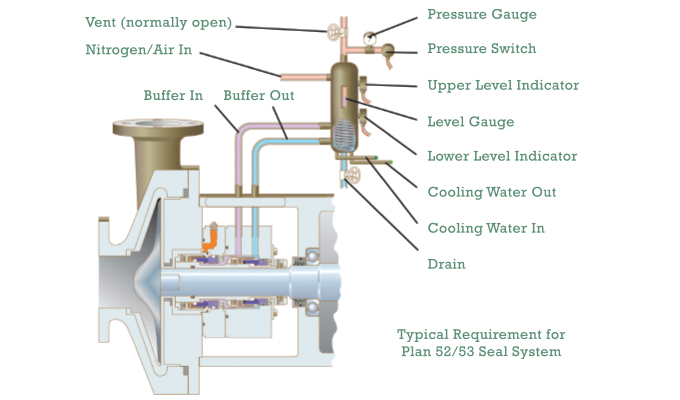
A LOOK AHEAD
Standards play a key role in the chemical industry. In next month’s conclusion, we’ll take a closer look at the peace of mind—both within the industry and for customers—that comes from a thorough understanding and implementation of performance and safety requirements throughout a plant.
FOR MORE INFORMATION
Colin Guppy is Sundyne’s chief commercial officer. He is responsible for developing strategies and tactics for Sundyne’s chemical industry sector. He can be reached at colin.guppy@sundyne.com. Sundyne has assembled industry-leading brands that provide customers with a wide range of fluid and gas handling services and solutions. Brands like Ansimag, HMD Kontro, and Marelli have broadened the original Sundyne portfolio for a wider range of markets. Sundyne equipment can be built to most standards, including ANSI, ISO, and API. For more information, visit www.sundyne.com or www.hmdkontro.com.
MODERN PUMPING TODAY, October 2020
Did you enjoy this article?
Subscribe to the FREE Digital Edition of Modern Pumping Today Magazine!
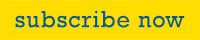