By Benson Hougland, Opto 22
In an era of increasing connectivity and technical capabilities, it seems like simple ideas should be, well, simple to achieve. Suppose you need to do something like:
- Log temperature data from a refrigeration unit into a database.
- Receive a text message if a warehouse door is opened after hours.
- Publish process flow and pressure data into a SCADA system.
- Send an air compressor’s total running time to a cloud analytics system Control a security light with your smartphone.
Simple ideas, right? But, in fact, while we can do all of this with current technology, it’s expensive, demands special skills, and involves many steps—all of which make any IIoT project far from simple.
IIOT PROJECTS ARE TOO COMPLEX
The majority of signals in the real world are basic wired switches, sensors, and transmitters, despite advances in smart wireless devices. Getting signal data where you want it to go is complicated. Take temperature data, for example. First, you—or someone you hire—needs to have the skills required to specify and procure all the numerous components of an I/O or PLC system that will work with a temperature sensor.
Then you must install an appropriate enclosure for the PLC and I/O, assemble them, and supply them with power. Next, you install a temperature sensor in the refrigeration unit, and connect it to a suitable input channel on a temperature input module mounted on the PLC rack. Then you program that PLC, using the vendor’s proprietary software, to configure the input channel for the correct signal type and to acquire and log the I/O data.
Next, you’ll likely need a PC with a software application that can read the PLC’s memory for the logged data, and translate the data into a format the database can understand. Finally, some software will need to log into the database and post, or insert, the logged, translated data. And if the database isn’t on premises, or in the cloud somewhere that’s accessible, good luck!
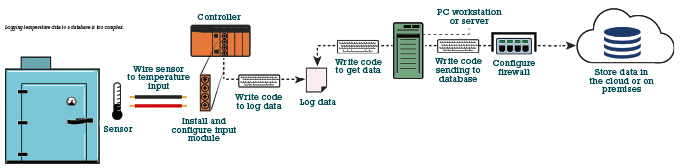
CONTROL SECURITY LIGHT
Turning on a security light from your phone sounds easy, but it still involves many steps. Once you have the light contact wired to an output on a PLC or PAC and the output configured, you’ll program the PLC to turn the light on or off based on an input from an HMI, which is usually running on a separate PC.
But if your HMI software program isn’t mobile-ready, you’ll need to find a different HMI package, buy it, and build new interface screens.
SEND COMPRESSOR ON-TIME
What about sending the compressor on-time to a cloud analytics platform? Again, first you must specify, buy, and install the right equipment. Then you wire a status contact on the compressor to a digital input module on the PLC, PAC, or controller to sense its on/off status.
After that, you program the PLC to configure the input and write ladder diagram or a function block to totalize how long the input is on, which will keep track of how long the compressor has been running. Next, you’ll need a gateway or other suitable computer that can read the PLC’s memory for the totalized data and provide that data to the cloud analytics package of your choice in a format it can understand.
Not simple.
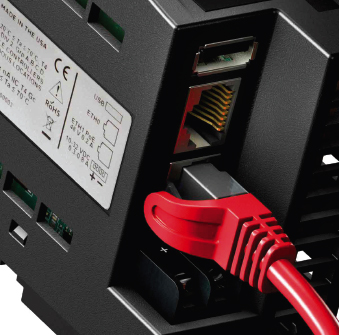
A COMPLICATED, COSTLY PROCESS
As we can see in just these few examples, meeting seemingly simple needs today is a complicated process. In many cases, you already have sensors, contacts, and transmitters in place with the data you need, but that data is locked in proprietary PLC systems behind someone’s control program. To access that data, typically you have to:
- Change the program in the PLC, PAC, or other controller to acquire the data you need.
- Purchase and activate necessary middleware (hardware and software, including licenses) with the protocols, languages, and translators required for your application.
- Configure and program middleware as necessary to move data where it’s needed.
- Understand and configure internet gateways and network connections, including server firewalls, security certificates, and user accounts.
- Establish communications between the PLC, PAC, or controller and the data’s destination.
MOVING TOWARD SIMPLICITY
The goal we’re trying to reach with the IIoT is a simpler process of gathering real-world signal data, communicating it, and making it available where it needs to be used. Whether you’re monitoring remote assets, acquiring data for analysis or regulatory purposes, controlling equipment and processes, or bringing visualization to operators and supervisors, you want to avoid complexity and the time and money costs that go with it. Fortunately, automation manufacturers are introducing newer kinds of I/O—called edge I/O—with features designed to help streamline IIoT projects.
KEY SIMPLIFIERS
These new edge I/O products do not require a PLC or industrial PC. Instead, they are designed as intelligent, distributed I/O devices to meet the needs of IIoT applications, especially those that require data acquisition or communications.
What are some of the key features of new edge I/O products that help simplify IIoT projects?
- Easy to spec and buy. A single part number includes everything you need: I/O, networking, processor, power, and embedded software. Edge I/O units don’t necessarily require a power supply, instead using power over Ethernet (PoE) for the unit’s processor as well as excitation for outputs and self-wetting discrete inputs. Typically, the cost is within many maintenance budgets.
- Compact and sturdy. Edge I/O products are small industrial units that can be placed almost anywhere. They operate within a wide range of ambient temperatures and comply with environmental requirements, including UL Hazardous Locations and ATEX approvals. Edge I/O is available in small form factors and may be DIN-rail or panel mounted.
- Web-based configuration. For maximum flexibility in diverse applications, edge I/O may include various kinds of multifunction or multi-signal (DI/DO/AI/AO) channels, all configurable via web-based software. It may also include intelligent features like counting, thermocouple linearization, minimum/maximum values, and digital totalizing, which run independently on the unit.
- Embedded software and protocol support. A secure, authenticated, web-based interface simplifies commissioning and troubleshooting with edge I/O. Additional software is embedded as well, typically for creating simple data flows to connect edge I/O with local or cloud-based software and services. IT protocols and OT protocols are both supported, and efficient data communication methods like MQTT add flexibility, performance, and security.
- Built-in security. To help you maintain cybersecurity, edge I/O includes a number of features to protect the unit and your data, for example, user authentication, data encryption, VPN support, security certificates, and a device firewall you can configure from the web-based interface.
By reducing the cost and complexity of IIoT projects, edge I/O makes your simple ideas much easier to achieve.
A LOOK AHEAD
One example of new edge I/O products is the groov RIO® family from automation manufacturer Opto 22. The first product released in the family is a compact remote unit with a communications processor and ten built-in I/O channels: eight software-configurable multifunction, multi-signal I/O channels and two Form C relays. In next month’s installment of this article, we’ll see how an edge I/O product like groov RIO could help with some of the simple applications we mentioned earlier.
FOR MORE INFORMATION
Opto 22 was started in 1974 by a co-inventor of the solid-state relay (SSR), who discovered a way to make SSRs more reliable. Opto 22 has consistently built products on open standards rather than on proprietary technologies. The company’s latest product line, groov RIO®, provides compact, autonomous remote I/O that is ideal for communicating field data in IIoT applications. All Opto 22 products are manufactured and supported in the USA. Most solid-state SSRs and I/O modules are guaranteed for life. The company is especially trusted for its continuing policy of providing free product support and free pre-sales engineering assistance. For more information, visit www.opto22.com.
MODERN PUMPING TODAY, June 2020
Did you enjoy this article?
Subscribe to the FREE Digital Edition of Modern Pumping Today Magazine!
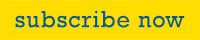