By Logan Walz, Oerlikon Balzers
Because machine tools constantly cut and grind away material at high RPMs to shape a workpiece, carbide cutting tools are often used instead of hardened steel to retain a sharp cutting edge and lengthen tool life. However, when highly-abrasive materials such as CFRP/GFRP/sandwich materials, graphite, Al alloys and ceramics are machined, even carbide tools can be prone to rapid wear.
In such cases, further hardening cutting tools with a variety of specialty coatings can significantly prolong wear resistance and service life. For cutting tools that are extremely expensive, this not only reduces costs but speeds overall cycle time as well.
These coatings, applied to machine tools such as taps, reamers, end mills, drills, inserts, counter sinks and other cutting tools, come in a variety of styles from physical vapor deposition (PVD) coatings up to proprietary diamond coatings.
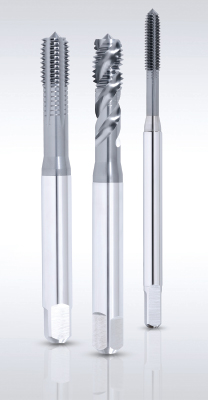
NEED FOR GREATER ABRASION PROTECTION
In a growing number of industries, manufacturers are continuing to place more emphasis on design and weight reduction. Subsequently, designers are increasingly using composite fiber reinforced plastics in many parts. However, these composites are exceedingly rough on cutting tools.
“The problem with the carbon and graphite fibers is that they are very high-strength and extremely abrasive,” says Volker Derflinger, a senior manager for Oerlikon Balzers, a company that has been producing specialized coatings for components and tools for more than thirty years. “For cutting tools to withstand heavy wear, a specialty coating with a very high resistance to abrasion is needed.”
In industries like automotive that require stronger, lighter materials, aluminum silicon alloys are also used. However, the higher the silicon content, the more abrasive the material.
“With aluminum silicon alloys, there are very hard silicon particles embedded in the aluminum,” says Derflinger. “When you have to cut the material, the silicon content is extremely abrasive and can rip up the carbide tool. Even tooling with typical protective hard coatings can degrade very quickly.”
HIGH-PERFORMANCE COATINGS
When it comes to machining very abrasive materials, uncoated carbide tools experience accelerated wear. To increase tool life, high-performance coatings can provide a vital protective barrier.
According to Derflinger, the ideal coating would have qualities such as a very hard, protective surface that, at the same time, maintains the sharp cutting edges that enable clean and precise cuts, while speeding production time.
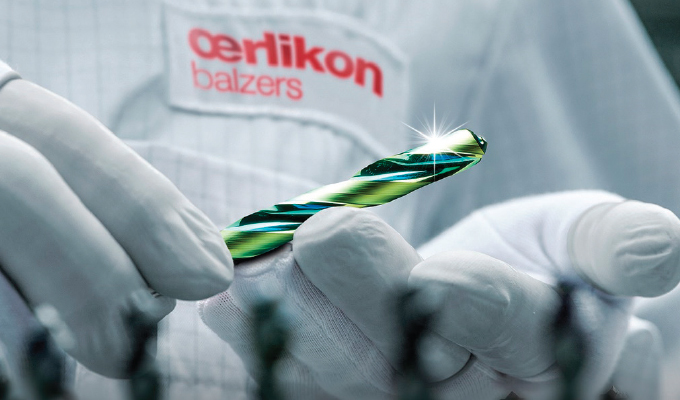
PVD COATINGS
One alternative that is increasingly being utilized in these industries are strong, non-hazardous, Physical Vapor Deposition (PVD) coatings. PVD describes a variety of vacuum deposition methods that can be used to produce thin coatings. PVD is typically used to coat tools and components at relatively low coating temperatures of 302-932 degrees Fahrenheit (100-500 degrees Celsius), which avoid altering the fundamental material properties.
Among the PVD options are several carbon-based coatings available that provide a unique combination of extreme surface hardness and low friction coefficient properties. One example, BALINIT Hard Carbon by Oerlikon Balzers is used for the machining of non-ferrous materials, including aluminum alloys with up to 12 percent silicon content (AlSi-12). The coating is also ideal for CFRP and GFRP materials, if the volume of fibers is not too high.
“The Hard Carbon coating works on CFRP and GFRP, but only when the fiber content is on the lower side,” explains Derflinger. “The more fiber content, the more abrasive the material is and then you need an even harder coating.”
The BALINIT Hard Carbon coating is thin, smooth, and has high hardness (40-50 GPa), making it well suited for applications that require superior wear protection. In addition, the thin, smooth application helps to maintain sharper cutting edges.
As an example, at a Malaysian manufacturer producing HDD aluminum alloy baseplates, coated carbide end mill tooling exhibited less abrasive wear, and produced 95 percent more parts with 55 percent lower production costs than untreated tooling.
The combination of coating hardness along with a low friction coefficient can also dramatically improve production even with dry machining.
In an application involving CFRP and thermoplastics workpieces, for instance, a Hard Carbon-coated counter sink tool produced 180 percent more parts than an uncoated tool. In another comparison, a coated carbide end mill doubled the parts produced with dry machining, compared to an untreated tool using lubricant.
DIAMOND COATINGS
When carbon content in composites or silicon content in aluminum alloys becomes too high, cutting tools typically require a diamond coating to prevent wear.
Traditionally, polycrystalline diamond (PCD) cutting tools have been utilized in such instances. PCD is a composite of diamond particles sintered together with a metallic binder. Diamond is the hardest, and therefore the most abrasion resistant, of all materials.
As a cutting tool material, PCD has good wear resistance but it lacks chemical stability at high temperatures and dissolves easily in iron. So, PCD tools are usually limited to materials such as high-silicon aluminum, metal matrix composites (MMC) and CFRPs.
In addition, PCD tools are geometrically limited in structure, and may be too rough or unrefined for the optimal machining of the wide range of non-ferrous materials. Finally, PCD cutting tools can also be quite expensive.
As an alternative, plasma-assisted chemical vapor deposition (PACVD) can be used to apply crystalline diamond structures in varying thickness and roughness. This can be highly advantageous for machining fiber-reinforce plastics, graphite, non-ferrous materials and ceramics. The diamond coating extends tool life while also improving cutting quality and surface finish.
With the PACVD coating process, a carbide cutting tool is sequentially coated by two different gasses in a heated vacuum container assisted by plasma. Each alternating cycle that built the atomic layer on the surface and the number of cycles thus controls the thickness of the final coating.
“As a cost effective, high-performance alternative, specialized PACVD-based diamond coatings can increase the service life of the tool,” says Derflinger.
Derflinger notes that standard PVD-applied metal-doped carbon coatings have a hardness of approximately up to 15 GPa, whereas a “diamond-like” carbon coatings ranges from 20-50 GPa. In comparison, a diamond coating reaches a hardness of 80-100 GPa. The PACVD process allows the diamond coating to be applied at varying thicknesses (6 μm to 12 μm), which can be customized to suit the application.
“Within any cutting process, the coating is constantly being removed,” explains Derflinger. “The thicker the coating, the longer it takes to wear it off. Once you are into to the carbide, the wear is accelerated further. So, a thicker coating normally gives a longer tool life, which then lowers manufacturing costs.”
In terms of satisfying such qualities, BALINIT Diamond Micro and Nano coatings are examples of PACVD-based diamond coatings formulated specific to the needs of a wide range of highly-abrasive, non-ferrous materials. While both are well suited to machining GFRP, CFRP, and ceramics, the rougher “micro” formulation is ideal for graphite.
With this approach to machining, carbide tools can be coated to enable the cutting of graphite workpieces with better quality and substantially greater speeds. Combined with significantly extended tool life, this allows even sophisticated workpieces and fine structures to be produced with a single cutter in a single clamping, which can help to eliminate cost-intensive reworking procedures.
When it comes to machining aluminum alloys, including those with high silicon concentrations (AlSi-17 or higher) and ceramic particles, the “nano” diamond coating can replace more expensive PCD tools.
In an application where a Duralcan composite workpiece comprised of ceramic particle-reinforced aluminum materials was drilled, a PACVD-based diamond coated cutting tool drilled twenty times more holes compared to even very hard “diamond-like” carbon coatings. The “nano” coating also works well with abrasive CFRP and GFRP materials.
In one example, production was significantly increased when a tool manufacturer drilled holes in CFRP/Al composite workpieces with the PACVD-based diamond coating. Compared to about sixty holes drilled with untreated tooling, approximately 380 holes were drilled with the PACVD-based diamond coating.
Finally, in the machining of ceramics, typically for the dental industry, both PACVD-based diamond coatings can substantially boost production and extend tool life while improving the surface quality of the workpiece.
As an example, when a micro ball nose end mill tool was used to machine a zirconium oxide workpiece for a dental application, a PACVD-based diamond coating produced about 900 finished parts, compared to about 100 parts for an untreated tool.
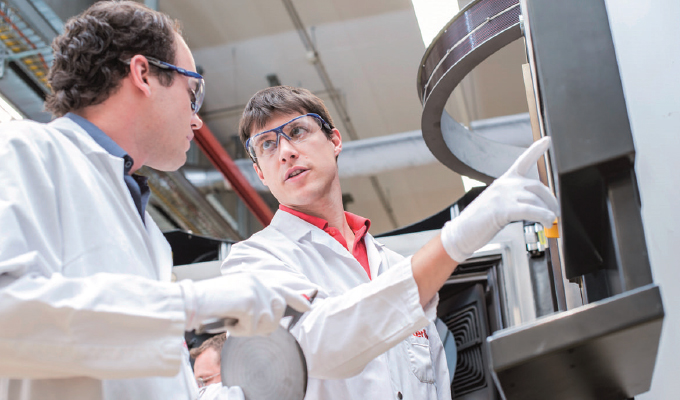
THE BOTTOM LINE
Some manufacturers may be inclined to use uncoated carbide cutting tools or traditional coatings because of their familiarity with such methods.
However, those that take advantage of the superior capabilities of high-performance Hard Carbon PVD and Diamond PACVD coatings will significantly harden carbide cutting tools and improve part quality. This will enhance production and tool service life, which also improves the bottom line.
Even if the cutting tool is expensive, you can put a hard coating on it and you will get a much better performance out of it,” says Derflinger. “That is why in the future more and more tools are going to have specialty coatings.”
FOR MORE INFORMATION
Oerlikon Balzers is one of the world’s leading suppliers of surface technologies that significantly improve the performance and durability of precision components and tools for the metal and plastics processing industries. For more information, visit www.oerlikon.com/balzers/us.
MODERN PUMPING TODAY, April 2020
Did you enjoy this article?
Subscribe to the FREE Digital Edition of Modern Pumping Today Magazine!
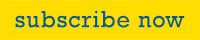