By Klaus Helmrich, Siemens Digital Industries
The sci-fi-sounding, near-magical benefits promised by Industrial Internet of Things (IoT) advocates are fast becoming a reality, and one place they’re taking hold is on the plant floor for maintaining equipment. The transition is bringing unheard of capabilities, including autonomous maintenance in which the system essentially determines and carries out all aspects of maintenance.
Siemens’s MindSphere is an IoT operating system that streamlines the move from previous maintenance methods by connecting factory assets and providing a central view of machine performance and health. In addition, using MindSphere enables manufacturers to grasp the outputs of maintenance tasks, allowing them to make informed decisions that support manufacturers’ operational and business needs.
INDUSTRIAL IoT AND PRESCRIPTIVE MAINTENANCE
Industrial IoT-based maintenance systems can reduce downtime to near zero, eliminate unnecessary maintenance and the need to stock expensive replacement components, and shorten the time required to identify the root cause of machine failures. At a higher level, they help industrial organizations boost asset availability while also infusing greater automation into the process. Put simply, the latest approach, dubbed prescriptive maintenance, solves the age-old problem of ensuring plants operate efficiently and productively.
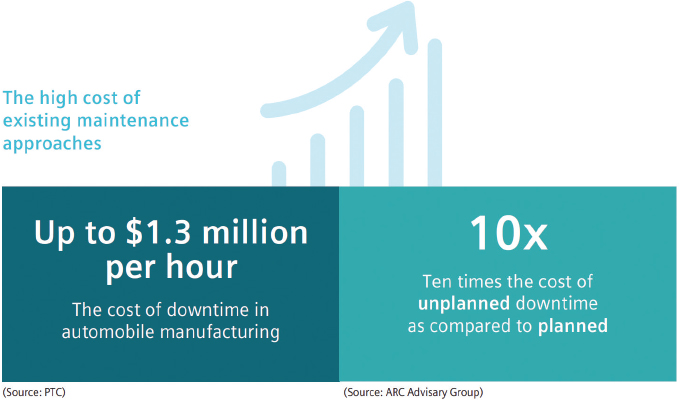
From a financial perspective, there is a dire need to shift to more effective maintenance practices. Recent research from PTC calculates the cost of downtime in automobile manufacturing at up to $1.3 million per hour, while the ARC Advisory Group estimates the cost of unplanned downtime is ten times that of planned downtime.
However, even as most manufacturers are generally aware of what’s possible with an Industrial IoT-based approach to maintenance, the question remains for most: How do I transition from my current maintenance routine to an IoT-based approach as quickly and inexpensively as possible?
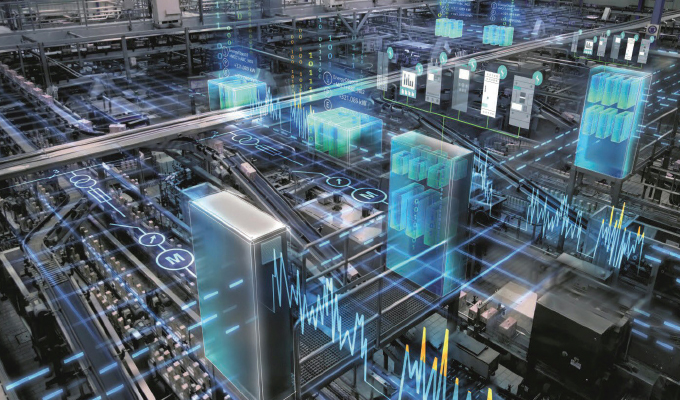
THE EVOLUTION OF MAINTENANCE
To understand how manufacturers transition from reactive to prescriptive maintenance, it’s useful to understand each stage of the journey.
Reactive Maintenance
The most rudimentary form of maintenance is reactive. With this approach, also known as “run to failure,” maintenance and repairs are made, or the equipment is replaced, only when necessary; that is, when it fails. The process is inefficient and results in production and productivity losses from unplanned downtime and more seriously, costly mechanical failures. Using this method, it is difficult—if not impossible—to track down the root cause of failures. Also, manufacturers must stockpile replacement parts, which ensures quick repairs but also increases maintenance costs.
Scheduled (AKA Preventative) Maintenance
Moving to the next stage, maintenance is scheduled at specific intervals—regardless of machine health or performance—to reduce the frequency of reactive maintenance, including unpredictable, unplanned downtime, and equipment breakdowns. Instead, the goal is to keep equipment operating at peak efficiency.
However, schedules rely on information provided by the manufacturer or are based on a calculated average or expected lifetime, which doesn’t reflect what is really occurring. Some manufacturers learned to listen to their long-tenured operators who had developed a keen sense of the signals—for example, the smell of an overheated part, the unusual vibration or sound emanating from a worn component—that signaled a potential stoppage. An attentive, knowledgeable operator considers actual conditions, but he or she is not scalable.
Scheduling maintenance introduces new problems: It is expensive because parts are replaced or serviced before they need to be, and spare parts must be kept in inventory. It’s time-consuming because equipment must be repeatedly taken offline, interrupting production.
It’s error prone because it relies on outdated information. Some manufacturers at the more mature stage of scheduled maintenance address these issues by deploying modest amounts of automation. For example, companies have deployed enterprise asset management (EAM) or computerized maintenance management systems (CMMS), which maintain a computer database of information about an organization’s operations and enables some preventative maintenance techniques. Although these systems maintain information that helps plan, optimize, execute, and track needed maintenance, they still require significant manual work to retrieve, compile, and analyze data—a daunting, resource-intensive task.
A LOOK AHEAD
In part 2 of this series, we’ll take a look at the conflux of predictive and prescriptive maintenance. Often confused with preventative maintenance, predictive maintenance begins to make use of Industrial IoT capabilities to identify more precisely when equipment requires maintenance to get maximum uptime and reduce maintenance costs. Although predictive maintenance enables smarter and faster root-cause analysis, reduces unnecessary downtime, and provides visibility into the health of remote machines, prescriptive maintenance moves facilities to a more automated approach.
FOR MORE INFORMATION
Siemens Digital Industries Software, a business unit of Siemens Digital Industries, is a leading global provider of software solutions to drive the digital transformation of industry, creating new opportunities for manufacturers to realize innovation. With headquarters in Plano, Texas, and over 140,000 customers worldwide, we work with companies of all sizes to transform the way ideas come to life, the way products are realized, and the way products and assets in operation are used and understood. For more information, visit www.sw.siemens.com.
MODERN PUMPING TODAY, March 2020
Did you enjoy this article?
Subscribe to the FREE Digital Edition of Modern Pumping Today Magazine!
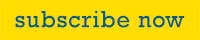