By Stephan Wild, HOMA Pump Technology
Especially when pumping chemically aggressive and abrasive waste water, as well as liquid chemicals, pumps must be particularly resilient and robust. A common problem is that the shaft seal and cable inlet are attacked and destroyed by the fluids. This causes the medium to enter the motor housing, which—at worst—can lead to a total failure of the pump. In addition, the non-resistant metallic components corrode through contact with the aggressive media, which reduces the performance of the pump and can also cause a defect.
HOMA Pump Technology has therefore developed a comprehensive range of stainless steel submersible pumps. The individual series CH, CTP, CMX, CV, CVX, and CK are equipped with discharge connectors from 2 inches to DN 150. The CH430 series is characterized by a compact and robust design, which allows flexible use in the chemical industry and the transport of bilge water in shipping.
The units are made of resistant, investment cast stainless steel, which means vibrations are absorbed more effectively, with less resultant stress on the bearing and mechanical seal. This increases the service life and considerably reduces maintenance intervals.
BUILDING RESILIENCE AGAINST AGGRESSIVE FLUIDS
In order to reliably and safely convey chemical fluids and wastewater contaminated with chemicals, the pumps used must be particularly resilient. If the shaft seal or cable inlet is decomposed by the medium, the aggressive chemical fluid gets into the motor compartment, ultimately causing the pump to fail.
Moreover, non-resistant metallic components may corrode due to contact with the medium being handled, resulting in reduced functionality or a pump defect. The various stainless steel submersible pumps in the CH, CTP, CMX, CV, CVX, and CK series from HOMA Pump Technology—designed with discharge connectors from 2 inches to DN 150—are suitable for continuous operation in the chemical industry and for the disposal of chemically contaminated wastewater.
The highly resistant investment cast stainless steel used makes the series resilient against aggressive fluids. In addition, contaminated water containing solids such as sand and sludge can also be pumped. With the CH430 series, the contaminants can have a particle size of up to 0.4 inches. Due to its compact and robust design, this stainless steel unit is versatile and can be installed and operated on either a stationary or mobile basis. This makes it ideal for use in the chemical industry and for the disposal of abrasive, chemical wastewater.
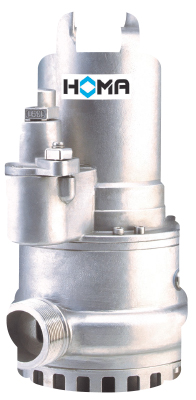
USE OF HIGH GRADE STAINLESS STEEL ENSURES TROUBLE-FREE PUMPING
To ensure continuous pumping, individual components of the CH430 series, such as the motor housing, impeller and pump housing, are made of stainless steel 1.4436. The motor shaft is manufactured with stainless steel 1.4462, while the various mechanical connecting parts use stainless steel 1.4571. The mechanical seal is available as an encapsulated version so that the spring of the seal does not come into contact with the pumped medium. This eliminates the need for bellows, which tend to be a fragile component. The strainer is installed on the pump housing and the pump block, which is made of highly resistant investment cast stainless steel, is fully floodable and sealed against pressurized water. This allows aggressive media and chemicals with a pH value of 3 to 14 to be conveyed. Liquids can be transported at temperatures of up to 104 degrees Fahrenheit (40 degrees Celsius). Levels of 140 degrees Fahrenheit (60 degrees Celsius) can also be sustained for brief periods.
Thanks to the investment cast stainless steel and the accordingly robust design of the pump, vibrations are absorbed more effectively, resulting in low susceptibility to failure and a long service life. The design also subjects the bearing and mechanical seal to less stress, which significantly reduces the maintenance intervals and increases the service life. The submersible pumps are also available in an explosion-proof design in line with the ATEX Directive II 2 G Ex c d II B T4(T3).
HIGH EFFICIENCY AND AUTOMATIC MONITORING VIA APP
The unit features a high degree of efficiency. The hydraulic requirements are factored in at the project planning stage using flow simulation software, in order to guarantee optimum pump design. This results in early insights into the achievable efficiency level, which is reflected in the low energy consumption of the pumps. Of course, it depends on the respective application scenario. In addition to the calculation software, the company’s own stator winding system influences the result and contributes to the high efficiency levels. The components of the series can therefore be adapted to specific order scenarios, as requested by the customer.
The pumps can be regulated and monitored fully automatically by an additional controller. Faults during a pumping process are automatically reported by the controllers to a mobile device via an app, and can therefore be rectified promptly. The fill level in the sump, the current measurement function and the thermal condition of the winding can be monitored. At the same time, maintenance intervals, delay times, start-up delays, and rotational direction detection are displayed. This ensures trouble-free operation when pumping chemically aggressive, abrasive media, and chemicals.
FOR MORE INFORMATION
HOMA Pump Technology was founded in 1946 by Hans Hoffmann Sr. as a repair business for electric motors. Over the course of more than seventy years, it has developed into a globally active, medium sized industrial company. The company is still family-owned and is now managed by the second generation, by Dr Klaus Hoffmann and Frank Schröder. The head office is in Neunkirchen-Seelscheid, near Cologne in Germany. From this location, sales are carried out via around sixty sales offices and distributors worldwide. HOMA specializes in the design and manufacture of submersible pumps and systems. The units are mainly used for building drainage, construction site drainage and surface drainage, as well as municipal and industrial water disposal and treatment. For more information, visit www.homapump.com.
MODERN PUMPING TODAY, January 2020
Did you enjoy this article?
Subscribe to the FREE Digital Edition of Modern Pumping Today Magazine!
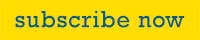