By Heinz P. Bloch
In part 1 of this series, we asked the question, “who should repair canned motor pumps?” For decades, the answer, according to the manufacturer’s then standard recommendation, was to return the CMP units to a highly experienced repair facility. Today, however, there are many installations that exceed an MTBR (mean time between repair) of eight years. If an issue is clearly confined to the wet end (i.e., the pump), a facility may still choose to ask its in-house experts to dismantle, diagnose, and possibly repair the pump. Removing the pump from the canned motor is not difficult, so on-site repairs are becoming more common. Below, we’ll examine some of the efficiency facts related to CMPs as well as their performance in different running conditions. Lastly, we’ll look at how new developments can best be instituted in today’s applications.
EFFICIENCY FACTS
Perhaps, and often quite wrongly, it had been assumed (in 2008 and the years leading up to it) that CMPs consume more energy than traditional pumps. However, even in 2008 a European CMP expert refuted this incorrect belief. He noted that, in over thirty years of applying CMPs, he had never seen a CMP consume more energy than the traditional pump it replaced! While he had once assumed higher consumption to be indicative of a worn conventional pump or the successor CMP being merely a better hydraulic selection (curve fit), he now believes that the original units were overly optimistic on their published efficiency and never included many losses, such as those attributable to couplings and seals.
He related his experience with one manufacturer of conventional pumps that always tested its units with lip seals instead of braided packing or mechanical seals. Some years ago, this expert was made aware of a company that let it be known they would evaluate quotes (bids received) based on input kW. As a result, the “guaranteed” horsepower went up almost 10 percent over some bidders’ published curves. The expert advised the owner-purchasers’ specifying teams to request an input kW value for the equipment offered. He noted that prominent CPM manufacturers will gladly comply since they, of course, supply both pump and motor.
As of 2019, most purchasers are aware of how the games are being played and make valid comparisons.
SOLIDS AND DRY RUNNING
In 2008, the average user/purchaser expressed disappointment that he could not send trash through bearings and close clearance components. Of course, the CMP vendor attempted to educate interested users on the limitations of the equipment and asked repeatedly about process stream and fluid properties. Many failures that in the past were blamed on “solids” or “dry running” were in fact initiated by internal flashing of the fluid. Flashing may have been due to users not understanding heat balance or just plain ignorance by the supplier. Even more important, there has often been insufficient failure analysis or follow-up by the manufacturer to determine the true root cause of a failure.
One interesting factor is always maximum heat rise; it occurs on a CMP after shutdown due to the latent heat trapped in the motor. However, this concern can be addressed by proper motor sizing, purging the motor after shutdown, or other methods—provided the buyer and a knowledgeable manufacturer cooperate. What was an issue for some in 2008 was a non-issue for others who adhered to proper procedures throughout.
In 2019, as in 2008, consider it the user’s and manufacturer’s responsibility to ask many questions. Both user and manufacturer should provide solid answers, not unsupported or inaccurate guesses. Pursue questions on maximum (short term) allowable temperature rise of the pumped fluid. The answers to such questions are easy to obtain. If informed users know what they are pumping and accurately describe the process fluids involved, the fact that they are about to purchase a CMP is of secondary importance.
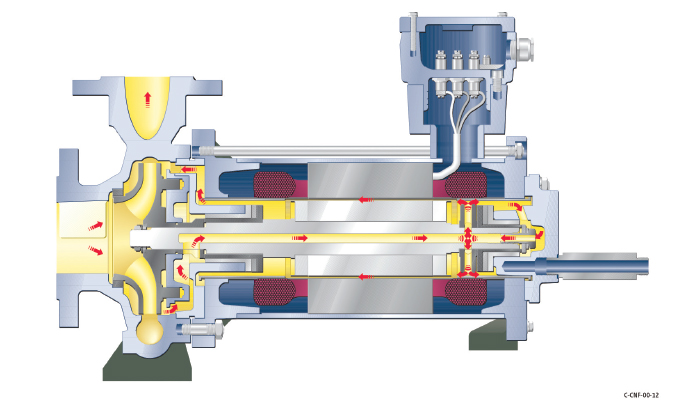
DECADES OF EXPERIENCE
Long before 2000, Kenneth Fischer collected CMP data from hundreds of CMPs at Hoechst-Celanese, a large process plant near Frankfurt, Germany. He also documented highly favorable MTBR and maintenance cost information at one of Texas A&M University’s International Pump Symposia. The proceedings of these gatherings are available. Chances are the earlier Pump Symposium Proceedings also addressed many user concerns and gave clues as to failure statistics. Good books and conference proceedings are still the one investment with the highest payback for motivated readers.
In 2019, user companies are more reluctant to publish asset reliability statistics than they were in previous decades. A refinery in one of the former USSR satellite countries submitted very favorable feedback on their approximately 300 CMPs to a widely read trade publication but withdrew the comprehensive article two or three weeks before scheduled publication. User companies believe that successes give them a competitive advantage which should be kept from the competition. However, competent vendors know how their products hold up in the real world and will gladly disclose these impressive statistics in closed-door meetings with future clients.
LAZINESS OR CONSERVATISM?
In 2008 and even in 2019, the buyer leaves pump procurement decisions to the design contractor. Some EPCs (engineering/procurement/construction) that are tasked with selecting pumps may place undue emphasis on initial cost. Moreover, the future advancement of an owner’s or EPC’s project manager is often linked to project costs coming in under budget or saving a day or two on the commissioning schedule for the plant. Accordingly, the different managers involved are not always incentivized to build highly reliable plants. Yet, common sense should convince us that if procurement decisions are based on initial cost and schedule only, then conventional pumps will likely be chosen. The equipment owner is then saddled with the consequences for decades to come.
Also, and sadly, CMPs might have gotten a bad name when, in early stages of development, certain vendors oversold the then existing true merits of CMPs in times past. While the merits of today’s well-designed CMPs are indisputable, there is nothing that cannot be mislabeled, maligned, misunderstood, mistreated, or destroyed. We have never seen an exception to this rule.
Fortunately, considerable and indisputable progress has been made since 2008. As was brought out earlier in this article, today, in 2019, there are entire oil refineries that operate only with canned motor pumps. Many hundreds of CMPs are often installed in Western European plants—many thousands of pumps overall. We are encouraged to report that some U.S. facilities have now fifty or more CMPs in their plant and that quality is being emphasized a bit more than first cost. With the help of competent CMP manufacturers, fewer inaccurate and often misleading cost calculations are finding their way into responsible corporations or design offices. That, we believe, is a highly desirable development from which all can benefit.
REFERENCES
- Bloch, Heinz P., “Fluid Machinery: Life Extension of Pumps, Gas Compressors and Drivers,” De Gruyter Publishing: Berlin, Germany. ISBN 978-3-11-067413-2 (available March 2020).
- Bloch, Heinz P., “Understanding Canned Motor Pumps” Lubrication Management & Technology, September/October 2008.
FOR MORE INFORMATION
Heinz P. Bloch resides in Montgomery, Texas. His professional career commenced in 1962 and included long-term assignments as Exxon Chemical’s regional machinery specialist for the United States. He holds B.S. and M.S. degrees (cum laude) in mechanical engineering from the New Jersey Institute of Technology’s Newark College of Engineering (“NCE”) and was honored as one of ten inaugural inductees into NCE’s “Top 100 Hall of Fame.”
MODERN PUMPING TODAY, January 2020
Did you enjoy this article?
Subscribe to the FREE Digital Edition of Modern Pumping Today Magazine!
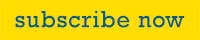