Municipal wastewater applications are notorious for the difficult—sometimes bizarre—solids that make it into the flow system. These applications pose several difficulties including the presence of non-biodegradable solid waste. You’re open to the public, so you’re never sure what you’re going to encounter, from underwear to Barbie dolls! Diapers and other plastic-reinforced cloth are an especially tough non-biodegradable solid.
Don’t wait until solids build up and clog your pump. Instead, avoid downtime by using these five ways to prevent submersible pump failure:
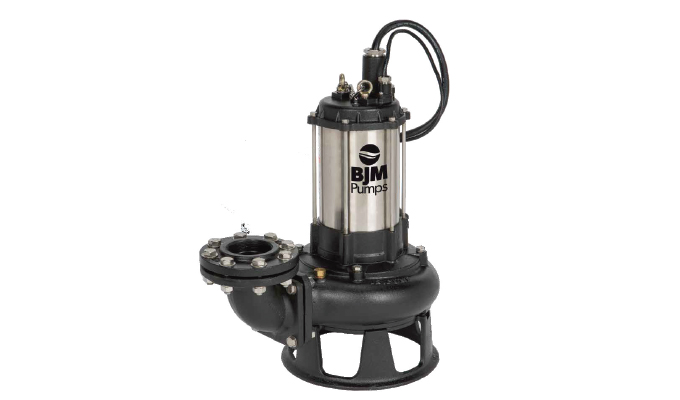
1. USE A SHREDDER PUMP TO CUT TOUGH SOLIDS
Submersible solids-handling pumps are each designed for a specific function. Using the correct pump for your given application helps to prevent pump failure, unnecessary maintenance, and downtime. Municipal wastewater solids can be very hard to break down, so submersible wastewater pumps need to be more robust. Submersible shredder pumps are ideal for these applications. Taking their name from the shredding action, shredder pumps reduce the size of solids to pass through the pump. Lower-horsepower pumps in particular need a heavy-duty shredder to break solids up before they pass through the pump.
2. RIGHT-SIZE YOUR PUMP
Once the solids pass through the pump into the discharge line, they tend to fall out of suspension and can lead to plugging of lines or pump discharges. To address this, ensure that the pump maintains a certain fluid velocity—a good rule of thumb is a minimum velocity of seven feet per second. However, this guideline requires that you first size the pump correctly.
To shred solid waste and help prevent pump failure, it’s important to right-size your pump for the correct horsepower:
- 2, 3, and 5 horsepower shredder pumps need to have enough power and cutting ability to prevent solids buildup and clogs. Hardened stainless steel assemblies are ideal such as the type 440 steel used in our SKG Series shredder pumps to shred and pass the majority of modern wastewater solids. Industrial wastewater applications typically have more predictable waste streams, allowing a customer to size a pump more on the desired flow and head, rather than maximizing torque to ensure shredding.
- 7.5-20 horsepower shredder pumps feature a larger motor and sufficient solids passage to shred and pass tough solids. For larger pumps used in municipal wastewater collection, BJM offers our SK series shredder pumps with a tungsten carbide-tipped shredder to break up difficult solids.
Consult an experienced supplier to ensure you select the right pump for your application.
3. INSTALL A CHECK VALVE
Another effective way to help prevent pump failure is to use a check valve attached to the discharge (outlet) of the pump to prevent back-flow and keep fluid and solids from re-entering the pump. Check valves are typically inexpensive, work automatically, and are available in many different types and sizes for different applications. Make sure to specify the correct cracking pressure (the valve’s minimum operational upstream pressure) for your given application.
4. CHECK YOUR SEAL FAIL CIRCUIT
For a simple maintenance solution, install and periodically check a seal fail circuit—a device monitoring for the presence of moisture in the seal chamber. These low-maintenance devices give you a visual or audible warning when your pump’s seals begin to fail. For example, BJM’s Seal Minder® is our seal fail circuit which is standard-supplied on many of our shredder pumps. There are two seals on a BJM pump—when the first fails, water begins entering the seal chamber. By using the Seal Minder® you’ll receive an early warning to service the pump and replace the seal before water gets into the pump motor, which will prove catastrophic to its operation.
Maintenance time depends on your specific wastewater application, but we recommend replacing your seals annually. Just be sure that whenever your seal fail circuit light comes on, do it right away! Remote monitoring in the control panel saves you maintenance time spent pulling the pump to check the seal chamber oil.
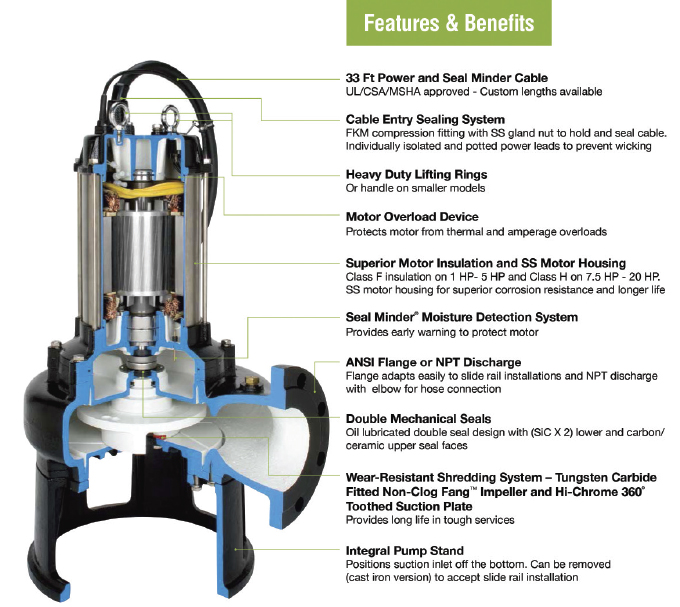
5. SOURCE HEAVY-DUTY PUMPS FOR HARSH APPLICATIONS
Some applications are especially damaging to submersible pumps, including saltwater, high water temperatures and high chemical concentrations. BJM shredder pumps constructed of both cast iron and stainless-steel can handle a wide variety of applications, including those with corrosive materials. We also offer robust pumps with high temperature protection (up to 200 degrees Fahrenheit [93 degrees Celsius] water temperatures).
WHAT’S YOUR NEXT STEP?
Contact a highly-trained, expert sales engineer to help you with your pump needs and to optimize your application. Make sure your pump supplier is familiar with your industry, the type of solids you’re pumping, and any special requirements you may have.
ABOUT THE AUTHOR
Steve Mosley is regional manager for BJM Pumps. BJM Pumps, headquartered in Old Saybrook, Connecticut, has been providing fluid handling solutions for industrial and municipal services since 1983. Over its thirty-year history, BJM Pumps has grown quickly by supplying world class pumps and accessories, priced competitively, through its global network of stocking distributors. For more information, visit www.bjmpumps.com.
MODERN PUMPING TODAY, May 2019
Did you enjoy this article?
Subscribe to the FREE Digital Edition of Modern Pumping Today Magazine!
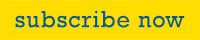