Headwinds over the past several years have taught oil and gas companies to maintain strict cost disciplines and be more efficient than ever. Organizations and budgets were cut, and investments were limited.
Yet, at the same time demand for energy continued to grow. And now as the oil and gas companies expand their portfolios towards future energy markets, like renewables, there is a realization that the need for efficient operations and maximized production uptime is more prevalent than ever.
DISRUPTION, INNOVATION, AND TRANSFORMATION
As oil prices begin to rise, producers are firmly adopting digital technologies to impact planning, building, and operations of assets while maintaining their capital discipline. Producers have already made great strides in technologies and applications in which plants with volatile processes or remote locations can be operated with low or no local human involvement. This trend will progress for more than just safety or cost reasons, but also for the productivity benefits.
It is these same technologies that will provide the transformational step change to enable oil and gas companies to move into the broader energy ecosystem.
However, the real game changer—or disruption—lies in integrating these technologies in a way that drives the evolution from connected operations, to collaborative operations and ultimately autonomous operations to achieve maximum value.
“Digital” has become more important than ever in today’s industrial space. It has been shown that by properly using digital technologies, the oil, gas and chemicals sector can reduce capital and operating expenditures by up to 30 percent.
The same technology will have a massive impact on tying the entire energy ecosystem together. However, getting such results is not just about doing things better but rather doing things differently.
VISUALIZATION, ANALYTICS, AND MACHINE LEARNING
These technologies are moving companies to an era where critical assets equipped with smart sensors now tell people what is wrong, long before failures even occur. Providing operators with quick access to hundreds of years of data and analytics, rather than relying on the experience of individual employees, increases efficiencies, reduces downtime, and avoids costly shutdowns. When data and technologies across a plant, and even across enterprises, are integrated into a holistic view, this opens whole new approaches to how operators and experts collaborate and use asset information and process analytics for quick decision-making and lost time prevention.
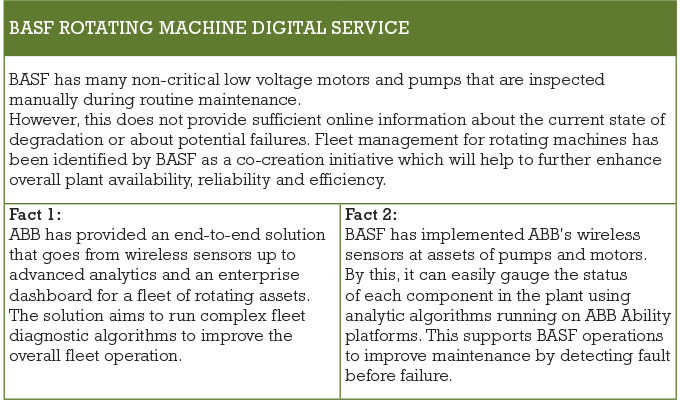
CLOUD-BASED TECHNOLOGY
This technology creates an ecosystem connecting the workforce in a way that enables it to collaborate anywhere—and in real-time. For example, moving SCADA to the cloud allows managers and operators to have complete information for their facilities while on the go.
CONNECTED OPERATIONS
The future will bring more enterprise-wide use of remote-enabled condition monitoring technologies, predictive and descriptive data analytics, and advanced process control applications so that operational effectiveness of plants can be understood in near-real time. This provides the right blend of technology, expertise, and information. Providing the correct information when it is most needed means the best decisions can be taken. By continuously collecting and analyzing data, and through special algorithms, early warnings can be in place to reduce any risk to a process or plant.
ARTIFICIAL INTELLIGENCE
Furthermore, new digital technologies and the rise of artificial intelligence (AI) are enabling totally new designs and concepts. ABB, as one of the world’s largest automation technologies providers and robotics manufacturers, and with its acquisition of machine and factory automation leader, B&R, will drive the integration of different automation technologies for an autonomous future.
INDUSTRIAL INTERNET OF THINGS (IIoT)
Connecting field assets and equipment using sensors enhances monitoring and diagnostics. The IIoT helps build real-time insights on the operation of assets and whole processes, thereby helping to optimize utilization and maintenance planning. However, digital success, and ultimately the profitability of a business, hinges not on individual technologies but the integration of the IIoT. Key to this are collaborative operation centers and control rooms which pull the data from these sensors and devices together. They enable analytics reporting and monitoring, while presenting dashboards that are relevant to all stakeholders, including executives, production managers, operations personnel, and maintenance staff.
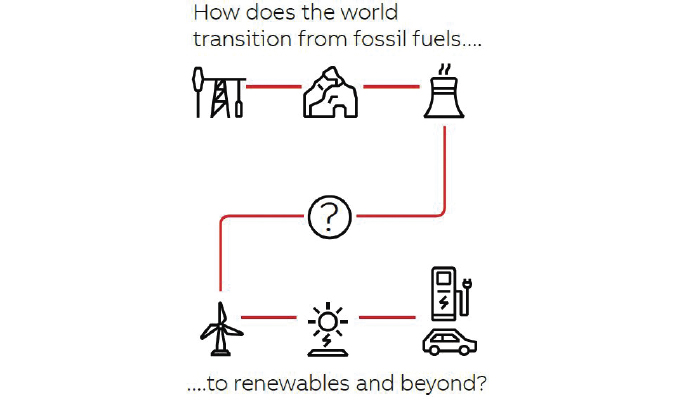
DIGITAL TWIN APPLICATIONS
A good digital infrastructure is almost impossible to implement without a digital model of the plant. A digital twin is a complete and operational virtual representation of an asset, subsystem or system, combining digital aspects of how the equipment is built (PLM data, design models, manufacturing data) with real-time aspects of how it is operated and maintained. The capability to refer to data stored in different places from one common digital twin directory enables simulation, diagnostics, prediction, and other advanced use cases.
A typical modern industrial device already creates a formidable digital data-trail. This includes CAD drawings and simulations during the design phase, information on location, connected equipment, and configuration from the integration phase, as well as subsequently collected utilization, diagnostic, and maintenance data. In addition to such definable, measurable, or observable data, algorithms can calculate or simulate non-observable parameters, both actual and predicted.
These data and algorithms typically already exist in various locations or formats. If they can be accessed from one virtual directory—the digital twin—this provides a comprehensive digital image of the physical equipment. More than being just a static description, this information can be used to simulate the behavior of the physical object. 3D visualization tools also allow virtual inspection and observation of the equipment and enhance understanding and insight.
COLLABORATIVE OPERATIONS
This approach transforms how every member of the supply chain works together during operations. Collaborative operations enable remote operations and fleet wide management. It uses digital technologies to monitor and analyze assets and processes. Collaborative operation centers help to maximize productivity and ensure safety always. They achieve this through decision supporting tools and the 24/7 remote availability of process and data engineers located in collaborative operations centers globally. These centers pave the way for the application of further technology advancements such as AI.
INTELLIGENT PROJECT EXECUTION
In the plan and build phase digital technologies are successfully streamlining project execution and integrating traditionally separate systems in the planning and build phase. Studies show that 64 percent of oil and gas projects experience cost overruns and 73 percent of them have scheduling delays. Streamlining project execution uses smart engineering technology to combine people, processes, tools, and standards. This not only results in 25 percent quicker schedule completion but can also reduce change orders by 50 percent and decrease costs up to 30 percent.
Because of cloud engineering, virtual factory testing and simulation, electrical, automation, instrumentation, and telecoms are no longer designed as separate systems, but instead are built into one collaborative environment, thereby optimizing customer objectives at every stage of the life cycle.
Taken together, intelligent projects and collaborative operations are perfectly complementary, spanning the full lifecycle of an asset with cost savings alone exceeding 35 percent if applied consistently.
Innovating together to transform projects and improve operations. ABB’s intelligent, integrated solutions help customers minimize cost, schedule, and risk across the energy industry. For more information, visit www.abb.com.
MODERN PUMPING TODAY, May 2019
Did you enjoy this article?
Subscribe to the FREE Digital Edition of Modern Pumping Today Magazine!
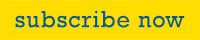