The Otay River Pump Station (ORPS), which pumps seven to nine million gallons of raw sewage per day to the South Bay Water Reclaimation Facility for water recovery, had a problem in the large 50-foot-long by 10-foot-wide by 30-foot-deep wet well. A floating blanket of grease and debris, sometimes as thick as 4 feet, would occur on a regular basis. The City of San Diego had been contracting two vacuum trucks to clean out the station every three to four months at a cost of approximately $50,000 to $100,000 per year. As the City has had good experience replacing their clogging non-clog pumps with Vaughan Chopper pumps they turned once again to Vaughan Company for a more cost-effective solution.
CHOPPER PUMPS AS CONDITIONING PUMPS
Vaughan Chopper pumps are ideal for use in pump stations and lift stations as conditioning pumps (patented with additional patents pending). When used as a conditioning pump, a submersible Vaughan Chopper pump is fitted with a nozzle to provide high-velocity mixing, and is placed in the problem wet well on a portable stand. The purpose of the conditioning pump is to recirculate and chop the contents of the wet well.
Recirculating the wet well contents through a Vaughan Chopper pump chops and mixes not only the grease and debris that can accumulate as a floating layer, but also chops and re-suspends heavier debris that can accumulate on the wet well floor. This homogenization of the wet well contents not only prevents buildup of grease/debris in the wet well but also helps to prevent clogging of the non-clog pumps typically used as dewatering pumps for these stations.
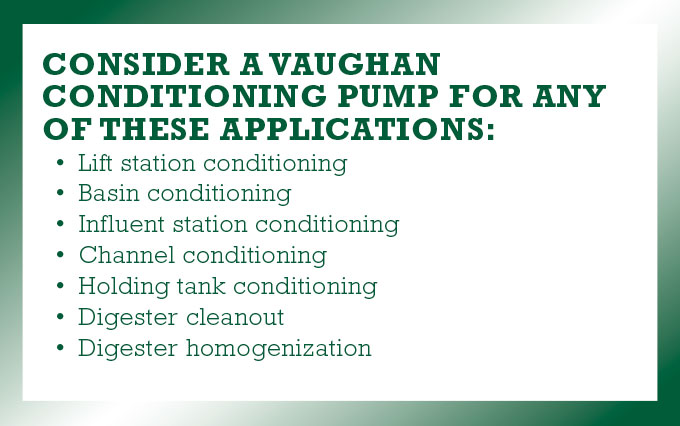
HELPING THE BOTTOM LINE
The economic benefits of using a chopper pump as a conditioning pump apply in several different scenarios to lessen the impact of costly clean out cycles and maintenance.
Reduce the Vacuum Truck Visits
By re-suspending and removing floating solids that have accumulated on the floor, a conditioning pump reduces—and in most cases eliminates—the need for costly vacuum trucks, saving thousands of dollars each year.
Existing Non-Clogging Pumps Experience Clogging
If the large pumps you are currently using in the station (wet well or dry well) are clogging on solid filled liquid they are trying to pump, it can be a costly endeavor to replace the pumps. Some pumps can cost you upward of $350,000 to replace. A conditioning pump solves this problem at a fraction of the cost. You can put the conditioning pump into the wet well and chew up all of the rags and solids so that the existing pump won’t get clogged.
Floating Layer of Grease and Debris Accumulated
Lift stations/collection pits tend to form floating mats that standard lift station pumps cannot pump out. If left unattended, the layer will continue to thicken until you eventually need to call in a vacuum truck to suck off the thick layer. This results in thousands of dollars in maintenance and dumping fees. A conditioning pump can get rid of unnecessary third-party cleaning cycles and the unwanted costs that come along with them, by recirculating/conditioning the pit until the mat disappears.
Settling Solids on the Floor of the Wet Well or Sump
When solids fall out of suspension, they create a “settling layer” at the bottom of the tank, resulting in costly third-party cleanout cycles. A conditioning pump re-suspends these solids so the duty pumps can actually pump out and remove the solids, and also save you from those costly clean out cycles.
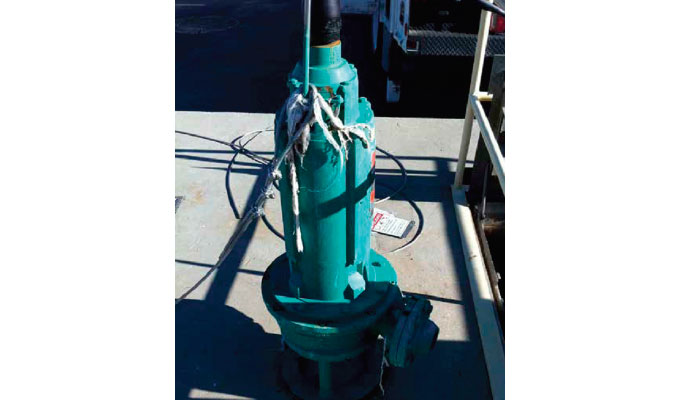
This Vaughan Chopper pump eliminated a 4-foot mat of grease and debris, plus paid for itself in two and a half months.
INNOVATION THAT PAYS FOR ITSELF
For ORPS, Vaughan Company selected an 8-inch submersible chopper pump with a 25 horsepower, 1,200 rpm motor with mixing nozzle and portable stand. In eighteen months of use with the Vaughan conditioning pump the wet well has not required cleaning. Based on the cost of the pump and installation the pump paid for itself in two and a half months of use.
FOR MORE INFORMATION
Dale Vaughan is president of Vaughan Company. Since company founder Jim Vaughan invented the world’s first chopper pump in 1960, Vaughan Company has been a leader in pump technology for municipal, industrial and agricultural applications. Proudly made in the USA, Vaughan’s in-house experts use computational fluid dynamics (CFD) to analyze flow patterns and velocities within its pumps to optimize efficiency, performance, and reliability. For more information, visit www.chopperpumps.com.
_______________________________________________________
MODERN PUMPING TODAY, October 2018
Did you enjoy this article?
Subscribe to the FREE Digital Edition of Modern Pumping Today Magazine!
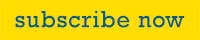