The ongoing pressure and temperature changes within pump systems can create an environment where bubbles can form and can’t escape. In these instances, cavitation can occur as the pump moves water from one chamber to another. Under its Goulds Water Technology brand, Xylem recently conducted a study to determine the cause and solution of one particular instance of cavitation.
DEFINING CAVITATION
Pump cavitation in an impeller is the result of a drop in the pressure of a moving liquid through the impeller’s eye. This reduced pressure causes bubbles to form, as the pressure of the liquid continues to fluctuate and drop, the bubbles collapse.
Implosions of these vapor pockets can be so rapid that a rumbling or cracking noise is produced, which sounds like rocks passing through the pump. The hydraulic impacts caused by the collapsing bubbles are strong enough to cause areas of fatigue on the metal impeller surfaces and a decrease in pump performance may be noted, depending on the severity of the cavitation.
TYPES OF CAVITATION
There are several different types of cavitation, including:
- Suction recirculation cavitation, in which turbulence of the fluid releases entrained gases into the suction piping.
- Vaporization of the liquid within the pump caused by a loss of suction head or an increase in suction temperature.
- Vane passing syndrome caused by too small an impeller to cut water clearance.
- Air ingestion on the suction side of the pump, which allows air and bubbles into the suction of the pump.
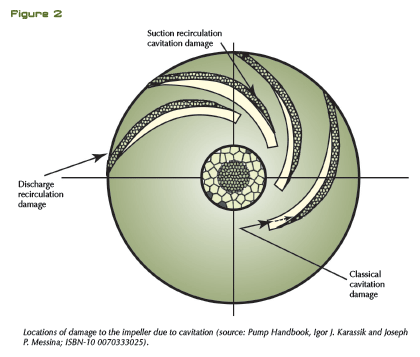
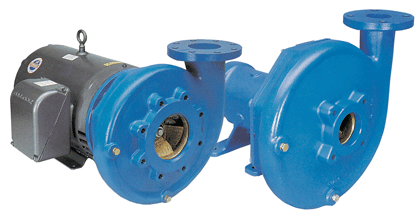
CAUSES AND SYMPTOMS OF CAVITATION
Cavitation can be caused by reoccurring restrictions in the suction piping or a host of intermittent incidents. Reoccurring restrictions include: a foot or other valve in the suction piping that sticks; an object that is plugging or clogging the suction piping (i.e., a loose rag, grass or other natural debris, and so on); a collapsed pipe liner which restricts the piping at higher velocities; a blocked filter or strainer; and air that is introduced into the suction side of the pump reducing capacity.
Intermittent incidents that cause cavitation are many and may include
Inconsistent tank levels: The level in the suction tank increases, which decreases the differential head across the pump, or the level in the open suction tank decreases causing vortex issues that allow air into the pump suction. Running several pumps simultaneously can decrease the supply level too much.
Change in temperature: When the sun heats the suction piping too much, it can raise the liquid temperature close to its vapor point causing cavitation. A discharge recirculation line, piped to the pump suction, can also open and heat the incoming liquid, the tank can be heated too much to de-aerate the fluid, or the tank could be pumped dry.
Change in pressure: The vapor pressure of the pumped liquid can get very close to atmospheric pressure, causing the pump to cavitate every time it rains, or due to a packed valve in the suction piping that is at a negative pressure causing air to leak in through the packing.
Other: The suction lift could be too high causing an increase in pipe friction to reduce the suction head, or a booster pump could malfunction or leak excessively.
3656 and 3756 M and L Group cast iron and bronze pumps from Goulds Water Technology, with 18BF 60 horsepower, 1800 RPM, as used by LAD Irrigation (Western Hydro) at the Pasco, Washington, job site.
EVALUATION OF CAVITATION DAMAGE
Cavitation damage to a centrifugal pump may range from minor pitting to catastrophic failure depending on the pumped fluid characteristics and duration of cavitation. However, most of the damage typically occurs within the impeller, resulting in a pockmarked, rough surface along the underside (classical cavitation) or visible side (suction recirculation) of the vane’s leading edge.
These two types of cavitation—classical and suction recirculation—generate noise and vibration, as well as damage. They can be distinguished by a careful inspection of the damaged impeller.
- Classical cavitation: Damage is located on the non-visible or underside of the vane. It starts near the leading edge and can extend up to two-thirds of the vane length before the pressure causes the bubbles to implode. In order to evaluate the damage, one must feel or look at the underside of the vane with a mirror.
- Suction recirculation: Damage is on the visible or pressure side of the vane’s leading edge. If tip recirculation, or discharge recirculation, has occurred, damage will be on the visible or pressure side of the vane near shroud walls (Point Y of figure 1).
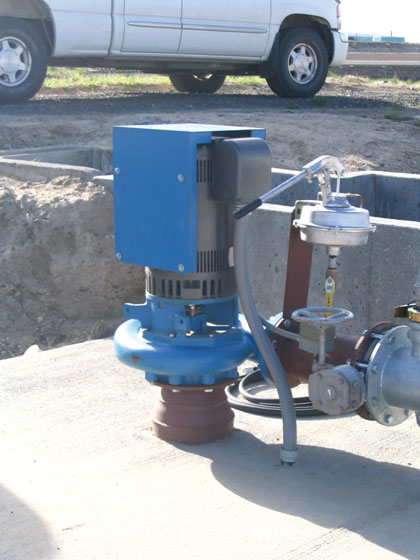
Identifying the cause of instances of cavitation can help determine the best course of action to address and resolve it. Early detection and solution implementation will prevent long-term damage and unnecessary downtime incurred from cavitation issues.
GWT representatives had the idea to install straightening vanes in the suction piping to help prime the vertically mounted configuration.
CASE STUDY: SUCTION RECIRCULATION CAVITATION
An irrigation pump that was mounted in the vertical position was cavitating throughout the usable flow range 500 to 1600 gallons (1893 to 6057 liters) per minute. The pump was returned to Goulds Water Technology (GWT), a Xylem brand, for inspection, as well as performance and vibration testing. The results of this testing indicated that there were no vibration issues and the pump was returned to the customer to verify proper field installation. The pump was reinstalled at the customer’s site but continued to exhibit the same vibration problems.
After collaboration and problem-solving sessions between GWT service representatives and Western-Hydro, a primary GWT distributor in Washington, two GWT representatives flew to the job site to review proper pump and pipe installation and made sure net positive suction head (NPSH) requirements were being met. The findings of this installation and NPSH audit concluded that all proper installation and operation procedures were correct; however, the pump cavitation issues during operation remained.
The GWT representatives considered two new ideas as possible solutions to this perplexing situation. The first was to add a vent connection in the seal chamber. Since the pump was mounted in a vertical position, the seal chamber was not being properly vented, and therefore the presence of an air pocket during pump operation could cause cavitation. To test this theory, the pump was disassembled and the seal chamber machined to include an additional vent connection. A hose and valve were also fitted to the vent connection. The pump was then reassembled and started. During pump operation, the seal chamber vent valve opened allowing any air pocket that may have been present to disappear. Even after several minutes with the vent valve open, the pump still showed symptoms of cavitation.
Recirculation cavitation (also called rotating stall or separation) is a term used to describe the formulation of vapor-filed pockets. This type of cavitation is less well known and understood than classical cavitation, though it is more common. It is most often caused by suction recirculation as shown at Point Z in figure 1.
This damage would be on the opposite side of the vane as that which would occur with classical cavitation (see figure 2). This continuous recycling results in noise, vibration and pressure pulsations. These results imitate classical cavitation.
STRAIGHTENING VANES
The second solution that GWT representatives explored was to install straightening vanes in the suction piping. The straightening vanes would reduce flow disturbance entering the pump’s impeller eye. The straightening vanes were installed and the pump was primed and started. Almost immediately the cavitation noise disappeared.
Over the next hour, the pump operating conditions remained smooth and without cavitation. The straightening vanes corrected the irregular flow velocities entering the impeller’s eye, which caused the water flow separation that lead to suction recirculation cavitation.
ABOUT THE AUTHOR
Kyle Schoenheit is the global product manager, Americas for Xylem’s Applied Water Systems business unit. For more information, visit xylemappliedwater.com.
MODERN PUMPING TODAY, July 2013
Did you enjoy this article?
Subscribe to the FREE Digital Edition of Modern Pumping Today Magazine!
