Laguna Beach County Water District (LBCWD) provides water services to around 25,000 residents within 8.5 square miles of Southern Orange County. The district receives approximately 1.14 billion gallons of water per year from the Colorado River and Northern California which is stored in twenty-one reservoirs. To deliver safe reliable water to its customers, the district operates and maintains thirty-six pumps; fourteen pumping stations; 3,500 valves; 900 hydrants; 8,000 customer meters; and over 135 miles of distribution pipeline.
While LBCWD is a relatively small operation with forty staff—twenty of whom are working as field crews, it is a forward-thinking water utility that has been moving from paper to digital over the last several years. Bobby Young, engineering manager at Laguna Beach County Water District, says, “More recently, in the last six months we have moved most of our operational management to Sedaru and rolled out Fieldforce to manage our day-to-day operations. With real-time mobile work management and network intelligence for pipes, valves, hydrants, customer meters, pumps, and so on, our work crews can do their job better with information at their fingertips and have the ability to complete work records before they leave a site.”
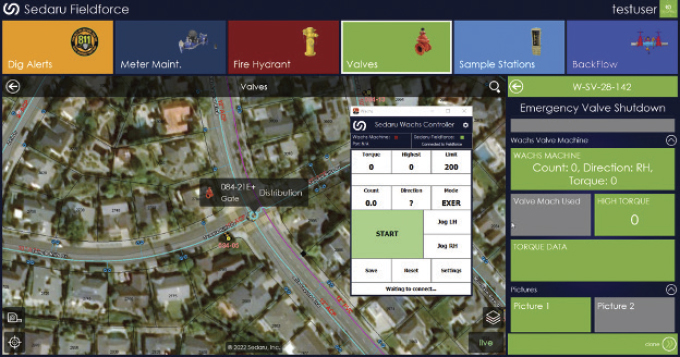
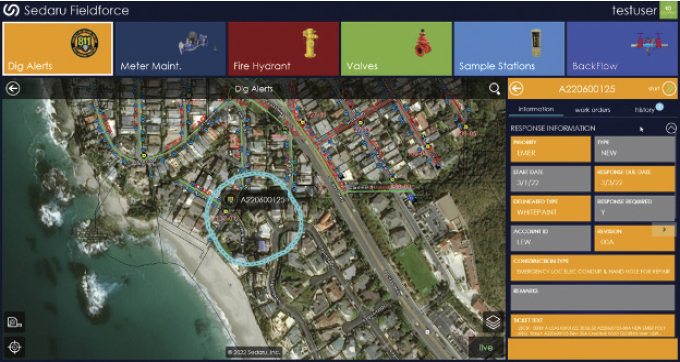
INFORMATION DRIVEN MAINTENANCE
LBCWD uses the new platform for its maintenance programs including hydrant, valves, meters, sample stations, backflow, pumps, water mains, laterals, water leaks, and emergency pumps. Work orders get assigned to a field crew who can see the work location on a GIS map and layer in assets that may affect or be affected by the work that needs to be done. The geographical display gives crews a holistic view of the work area so they can see where the water is coming from and where it is going. Crews can update progress in real time in the field and schedule additional work if needed and move on to the next job.
Having records of past work often helps field crews to resolve issues, so they see the value in record keeping which motivates them to add more data. LBCWD is working on building a strong historical baseline. “The more data we can collect, the better we can plan and predict situations before they become an issue,” says Young.
As more utilities are finding, when they replace one manual process with a technology solution, it accelerates additional advancements. In 2016 LBCWD switched to advanced meter infrastructure (AMI) that ended manual meter reading, but inadvertently lead to ending meter box inspections. This resulted in the need for a new metering maintenance program to check the 8,000 meter boxes every year or so, as they were no longer being monitored during their billing cycle.
The new program is run efficiently through Sedaru tracking the progress of the two-person field crew as they record findings in the field. If needed they can write a ticket for construction in the field if the job is outside of their scope, before moving on to the next box. Young says, “This used to be done with paper, amounting to potentially 8,000 slips, and as you can imagine it was not uncommon for a slip to be misfiled, or not make it to inventory ordering, or the work order to not get into the right hands. Now all of this is tracked in real time, and most valuable is the building of a historical baseline that will allow us to see trends, such as certain meters that need checking more often than others.”
INTEGRATION WITH EXISTING SOFTWARE
LBCWD uses Wachs valve machine in support of its valve exercise program. Using an advanced application integration (API), Sedaru now remotely operates the Wachs valve machine, while automating field data collection, eliminating the need for manual data entry to be completed in the office and automatically updating the valve status in real-time.
811/Utility Locates service, or DigAlert as it is known in California, is also integrated into the platform saving LBCWD time by automating the process. When a DigAlert ticket comes in, Sedaru parses the ticket information into the utility’s GIS, digitizes each ticket’s attributes, and presents the location on a map. The program reports all tickets and prioritizes those qualified as an emergency. If a ticket falls within the utility’s service area, the program automatically creates a work order.
Work orders can be automatically assigned based on location or an administrator can assign field personnel based on current location, expertise, or workload, and add any special instructions before sending to the field locator’s mobile device. Assigned tickets can be seen on a map and details can be drilled down in Field Force. The App has a tape measure feature that allows the field crew to determine the distance of the area, record information such as field status, pictures, and comments, and then automatically submit the Positive Response to DigAlert. By digitizing the process, LBCWD also gains an accessible historical record that provides defensibility in the event damage occurs.
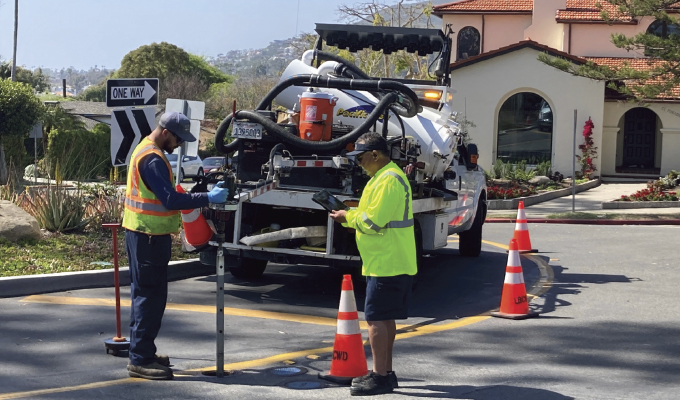
IMPROVED VISIBILITY INTO LEAK MONITORING
LBCWD is fortunate to not have a lot of leaks, but the old way of tracking on paper meant repair work was sometimes missed. The new platform allows work crews to monitor leaks when they are on-site, and instantly add or mark a change in a leak. Young adds, “Layering of information helps us to track and repair leaks when we are next in the area before it becomes a bigger issue.”
ACTIONABLE DATA
Having data on all assets organized both visually and in detail in one place, makes it easy to use. For example, in a redevelopment situation, LBCWD can look at a map and see what assets will be affected when a building gets torn down and rebuilt. The new build may require a different pressure zone, or a larger house may need a bigger meter etc. If a new development is going in, LBCWD can quickly see if there is water to the lot or if system improvements need to be made.
The more information that is gathered into the operational management system the more likely it is to become valuable throughout the utility. “Recording maintenance helps us budget for capital planning,” says Young. “As we build strong historical baselines, we expect to be able to be more proactive and plan for new challenges such as extreme weather events and measuring the benefit of new technologies and infrastructure improvements.”
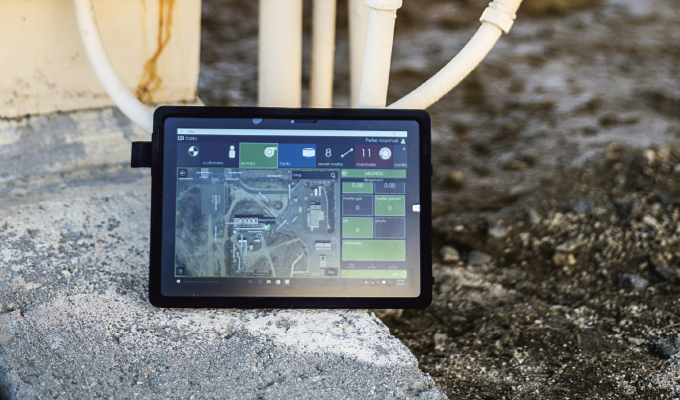
IMPRESSIVE TECHNOLOGY ADOPTION BY THE WHOLE TEAM
“Staff are building trust in the data stored in the management platform and so they are using it on a more frequent basis,” says Young. “Having a user-friendly experience for field crews to enter information is more appealing than scratching an instruction on a napkin or making a note on the back of a sheet and then remembering what to do with it when you get back to the office. That said, we are asking our workforce to do things differently and there are times when an iPad is hard to see in the sun, and it needs to be handled with care, which is not always easy to do in the rain or mud. So, we are asking people to do the best they can, and we are really pleased with the results.”
Overall, the benefits of having real time data in the field help crews to understand how decisions are being made, and how they can find efficiency. As water utilities are being asked to do more with less, these efficiencies, wherever realized, are helpful and crews know it.
Eric Callahan, engineering technician and GIS specialist for Laguna Beach County Water District adds, “I have been with the County Water District for twenty-six years and have gained a lot of knowledge during this time that has given me the ability to problem solve quickly and plan based on experience. However, as we hire new people, we need this knowledge to be transferable. Building our historical records is a valuable educational resource for new hires. On the flip side, our long-time employees have been asking for a better way to record and centralize information so it can be easily accessed, for quite awhile. We have tried a few programs over this digital journey, but the team has taken to Sedaru, in part because it’s extremely user friendly and customizable, and because it has become instrumental in running our everyday operations.”
FOR MORE INFORMATION
Trent Kamins is account manager for Aquatic Informatics. He and his team help utilities become more proactive and improve operations, maintenance, and asset management with digital solutions. Aquatic Informatics provide ongoing support and training for newly released features through regular software updates, ensuring that utilities get the most out of their data with the constant evolution of technology. For more information, visit www.aquaticinformatics.com.
MODERN PUMPING TODAY, June 2023
Did you enjoy this article?
Subscribe to the FREE Digital Edition of Modern Pumping Today Magazine!