Highly viscous substances demand robust equipment up to the task of proper handling during processing. No matter which industry, viscous media from peanut butter to polymers dictate the characteristics required of a pump properly engineered to transfer them from one processing step to the next in a productive and timely manner.
Add to that wish list a pump that supplies durable performance, decreases downtime, minimizes maintenance, and gives a long service life that keeps capital expenditures under control.
A gear pump can fulfill this wish list of specifications and is one viable option among pump styles to transport high-viscosity fluids in manufacturing operations. Engineered design modifications and simplified disassembly have made gear pumps suitable for hygienic applications, expanding their popularity in the food processing and pharmaceutical industry. A quick examination of the general features of a gear pump can help determine if this style pump can address your fluid handling requirements.
HOW DOES A GEAR PUMP WORK?
A gear pump is a positive displacement pump with a compact design that uses two gears positioned inside a pump housing. As the driving gear rotates, it draws fluid into the inlet port and carries it around the outside of the gear teeth to the outlet port. The gear teeth mesh, creating a seal between the inlet and outlet ports.
Flow rate is determined by gear speed. Temperature can impact pump performance. Gear pumps are ideal for applications that need consistent or measured fluid flow.
THE ADVANTAGES OF GEAR PUMPS
Precise Metering Capabilities
Some gear pumps are compatible with servo motor-driven filling equipment, resulting in a pump that offers flow rates with precise metering. The gears transfer materials mechanically in a smooth, pulse-free flow using interlocking and rotating cogs or gears. This clockwork-style gear action aids in the accurate metering of a fixed volume of fluids.
The more compact the design and the shorter the shafts, the better the gear pump’s ability to eliminate deflection at high pressure. This particular design aids pump efficiency, flow rates and durability. When comparing gear pumps for sanitary purposes, look for close tolerances for the pump’s gear clearance.
Tight tolerances allow the pump’s intake suction and the interlocking gear action to prevent slippage. The greater the slip, the more likely fluids can leak back into the inlet. Close tolerances promote tightly controlled fluid movement and more precise metering.
Pump High-viscosity Fluids
The gear pump design handles products with high viscosity or centipoise—up to 100,000 centipoises in some cases—and works best with materials that have some degree of lubricity, such as fats, oils, and glycerin, but also polymers, paints, chemicals, and petroleum products.
Maintain Product Integrity
Gear pumps mitigate shear stress and degradation by exerting low shear forces on the fluids being transferred. The close tolerances between the gears minimizes agitation to preserve product integrity and quality.
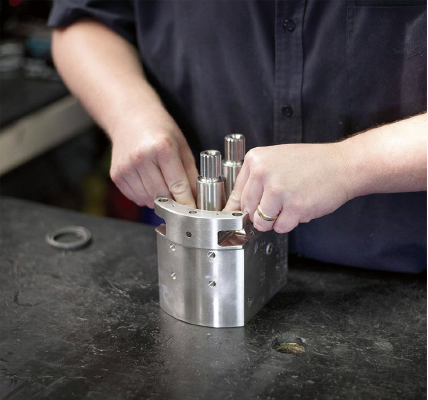
WHEN TO SELECT A GEAR PUMP INSTEAD OF A LOBE STYLE OR AODD PUMP
A scenario that would call for a gear pump instead of an air-operated double diaphragm (AODD) pump is when precise and consistent flow rates are critical. The gear pump design allows for accuracy and uniformity when pumping fluids, such as a filling operation that requires precise volumetric control. Gear pumps are ideal for applications such as precise dosing or metering of fluids.
In contrast, AODD pumps, while extremely versatile and capable of handling a wide range of fluids, may exhibit variations in flow rates due to their reciprocating diaphragm action.
The same reasoning applies to lobe pumps. Lobe pumps feature a different gear configuration and can be classified as a sanitary pump also. However, lobe pumps are equipped with a bigger cavity than gear pumps, leaving them unable to accurately meter process fluid.
In addition, a gear pump presents a more economical choice compared to a similarly sized lobe pump. In filling operations for example, a gear pump might cost approximately half that of a similarly sized lobe pump.
WHEN NOT TO SELECT A GEAR PUMP
Gear pumps are not recommended for abrasive substances, which can damage or wear down the meshing gears within the pump. In addition, while gear pumps work well for metering and precision filling, their design and primary action does not fit within operations with large bulk flow rates.
When a processing situation requires clean-in-place (CIP) operations, a lobe pump might make a better choice than a gear pump. A gear pump is designed for clean out of place (COP) processes, but the higher temperatures required for CIP can cause swelling of the Teflon-based gear in a 3A sanitary gear pump.
MAINTENANCE CONSIDERATIONS FOR GEAR PUMPS
Maintenance is a necessary “evil” that costs companies time and money and often requires skilled labor. Each maintenance cycle represents downtime or lost production. In addition, skilled laborers are scarce in many industries. The less time and complex pump maintenance requires or specialized tools and equipment, the better.
Gear pumps do need to be disassembled to be cleaned. While generally easy to maintain, this process of taking it apart and subsequent reassembly can be challenging. Highly viscous products can cake and collect inside, particularly near the bushings.
A gear pump with a clean or simplified design makes maintenance much easier for sanitary operations. This style will feature:
- One-way assembly to ensure accuracy and mitigate damage
- Easy disassembly in a minimal time period using ordinary tools
- A pump body milled from a single piece of stainless steel
- A design that eliminates front supports for a flush front cover for easier cleaning
- Fully polished TIG welding to eliminate visible welds on the pump
When in doubt, talk to a trusted contact at a reputable pump manufacturing firm to help narrow the possibilities. It helps to find a company that has a diverse product line to pinpoint the pump style that will supply the features required. Optimize efficiencies and recoup initial costs by choosing the best pump style for your operations.
FOR MORE INFORMATION
Unibloc Hygienic Technologies is an industry leader in precision-engineered positive displacement pumps, air–operated double diaphragm pumps, and drum pumps, as well as valves, strainers, bubble traps, oil coolers, and sight glasses. The company is known for industry leadership under its various brands: Unibloc pumps, Flotronic One-Nut AODD pumps, Hygenitec flow control products, and Standard Pump industrial products. For more information, visit www.unibloctech.com.
MODERN PUMPING TODAY, February 2024
Did you enjoy this article?
Subscribe to the FREE Digital Edition of Modern Pumping Today Magazine!