By Wes Byrne, U.S. Water
On the surface, it might seem that knowing when to replace the membrane elements in a reverse osmosis (RO) system would be simple. In attempting to keep it simple, many companies will use one or more of the following guidelines for replacing their membrane:
- Time, often after three years (the membrane manufacturer’s warranty period)
- An increase in the RO permeate conductivity, as related to their water quality requirement
- A designated reduction in the permeate/product flow rate as related to water demand
However, the reliance on simple limits may result in replacing the membrane prematurely. RO membrane elements have been known to last more than ten years, while still providing salt rejection and permeate flow rates similar to what they produced at their startup. Performance deterioration caused by membrane age occurs so slowly that age itself rarely plays much of a role in the life of the membrane. Rather, replacement it is more often related to how well the RO system is maintained.
If there has been an unacceptable decline in salt rejection that has occurred simultaneously with an increase in normalized permeate flow rate, it usually means that all of the membrane elements will need to be replaced, even those in a second pass if it received chlorinated permeate water from the first pass.
If a strong oxidant like free chlorine contacts the RO membrane, it may dramatically reduce membrane life. It should be understood that any exposure to free chlorine will damage the RO membrane, and the extent of damage will be related to the chlorine concentration and the amount of time it is in contact with the membrane. With continued exposure, the RO salt rejection will decline and the permeate flow rate will increase, the extent being best gauged by normalizing the permeate flow rate for any changes in water temperature and operating pressures.
Before assuming that all of the membrane elements need to be replaced, more insight about the problem can be gained by measuring the conductivity of the permeate water from each membrane vessel. Some rejection problems may be corrected by replacing only the membrane elements located in specific locations within the membrane vessel array, such as in the very lead end when there is excessive fouling caused by suspended solids in the inlet water. Poor performance from the concentrate-end vessels could be a symptom of scale formation, or it might simply be related to warmer water temperature when using low energy RO membrane.
If the RO salt rejection declines, profile the membrane vessel permeate conductivities to isolate the location of the problem and where membrane elements may need replacement.
Excessive fouling is the most common cause of reduced membrane life, which can be defined as allowing the RO feed-to-concentrate pressure drop to increase more than 15 percent or the normalized permeate flow rate to decline more than 15 percent. If biological particles and/or silicate clay particles are allowed to collect and compact against the membrane surface, it will take longer for cleaning solutions to wet out and completely remove the materials. If larger particles are allowed to collect and plug off the flow channels through the membrane elements, the cleaning solution will not be able to access those fouled regions. If cleaning does not restore the original feed-to-concentrate pressure drop or normalized permeate flow rate, then more aggressive cleaning may be needed, which is more easily accomplished with offsite cleaning.
Membrane surface fouling will cause the normalized permeate flow rate to decline, with fouling most severe in the lead-end membrane elements due to their higher permeate flow production. As these elements lose permeation, downstream membrane elements are forced to produce more water and subsequently suffer from increased fouling.
The inability to restore the normalized permeate flow rate with aggressive cleaning usually indicates that all of the (first-pass) membrane elements will need to be replaced.
Large biological particles can be shed into the RO feed water from biofilm present in the piping and system components located after dechlorination. These particles can get caught within the membrane spacing material of the lead-end membrane elements, which is more common with older RO membrane models that use a thinner spacing material, than the 34-mil spacing that is now common. They will cause the lead elements’ feed-to-concentrate pressure drop to increase, as well as across all the elements within their first-stage pressure vessels. If the pressure drop across the stage exceeds 60 psi, it can crush the concentrate-end membrane elements within the vessels.
If the first-stage pressure drop has not exceeded 60 psi, the problem can be corrected by replacing only the lead-end membrane elements. If an excessive pressure drop is allowed to occur, crushed concentrate-end membrane elements in the vessels may also need to be replaced.
A scale formation event can occur quickly for a number of different reasons, including the failure of a chemical injection pump or due to a poor upstream softener regeneration. Many types of scale/salts will cause the last-stage pressure drop to increase. Onsite cleaning is often successful if the scale is primarily composed of calcium carbonate, which will cause a substantial increase in the permeate conductivity from the effected membrane vessels. Sulfate scale is far less soluble than carbonates and its presence may result in the need to replace the concentrate-end membrane elements.
When scale formation causes an increase in the RO last-stage pressure drop that is not restored by cleaning, only the concentrate-end membrane elements will need to be replaced to restore original performance.
Silica scale formation may occur in geographic regions where the water source contains a dissolved silica concentration greater than 40 mg/L and the water temperature is somewhat cool. Silica scale will blind the membrane surface in the downstream elements, causing the normalized permeate flow rate to decline. As the concentrate-end membrane elements blind off in their permeation, the scale formation will work its way upstream as other elements are forced to produce more permeate.
With silica scale, the concentrate-end membrane elements will need to be replaced, the replaced percentage of the total being roughly proportional to the percentage decline in normalized permeate flow rate.
Knowing why RO performance has declined and which membrane elements are compromised will reduce the number of membrane elements that need to be replaced. It will also make it possible to modify the RO pretreatment, or possibly the RO cleaning frequency if appropriate, to potentially increase the life of the remaining and newly replaced membrane elements. If the specific mode of failure cannot be readily determined, the cost of a membrane autopsy would likely be justified.
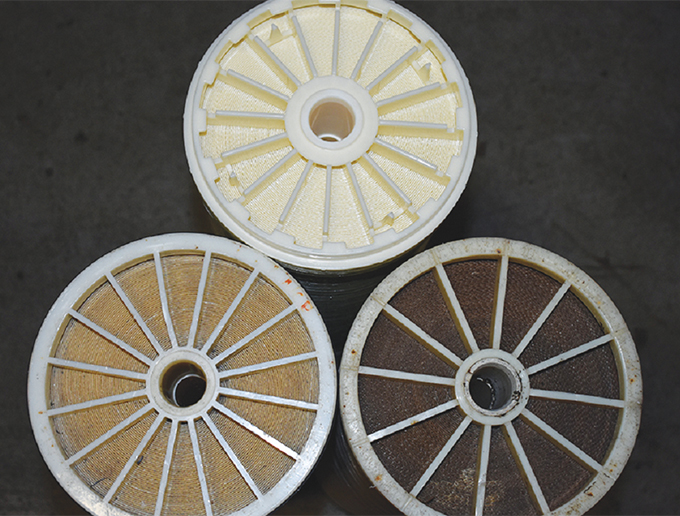
FOR MORE INFORMATION
U.S. Water is universally recognized as the most innovative and flexible provider of water and environmental management solutions in the marketplace by focusing on safe, economical, and environmentally sound programs for its customers. U.S. Water includes multiple locations and production facilities with representation and distribution centers nationwide and internationally. For more information, visit www.uswaterservices.com.
MODERN PUMPING TODAY, February 2020
Did you enjoy this article?
Subscribe to the FREE Digital Edition of Modern Pumping Today Magazine!
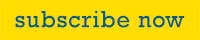