By Matt Hale, HRS Heat Exchangers
The term “disruptive technology” can be found everywhere across wastewater treatment, from conferences to whitepapers, and from small industrial and manufacturing sites to large municipal wastewater treatment plants. There is no doubt that disruptive technologies have the power to transform sustainability in the water sector, but it is important to realize that a technology does not need to be new in order to be disruptive. The widespread use of previously niche systems, or the novel use of well-established technologies like heat exchangers, can be equally transformative.
WHAT IS MEANT BY DISRUPTIVE?
A disruptive innovation is typically described as one that creates a new market or value network, leading to the displacement of market-leading businesses and products. High profile examples from everyday life include the Internet, mobile phones, Amazon, and television streaming services. However, it is also evident that while the terms disruptive innovation and disruptive technology may be new, the fundamental idea is not. From the Iron Age overtaking the Bronze Age, to the invention of gunpowder, the steam engine and the internal combustion engine, human history is littered with examples of transformational developments that have changed the course of global civilization.
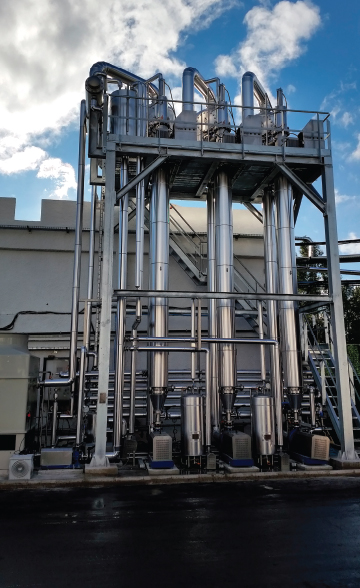
PART OF A WIDER AGENDA
The current high level of disruptive technological development and implementation is itself part of a wider industrial development, which is often referred to as Industry 4.0. This fourth industrial revolution refers to the increased use of technology, automation, and data across industries as diverse as agriculture and healthcare; and water treatment and the environmental sector are no different. While some people dismiss Industry 4.0 as a marketing buzzword, there is no denying the effects that digitization, data capture and analysis, and automation are having across the economy.
EXAMPLES OF DISRUPTIVE TECHNOLOGY
There have been plenty of disruptive developments in the treatment of wastewater streams through history, from sewer systems and trickling filters, to the use of activated sludge, anaerobic digestion, and nutrient recovery. Some of the current areas that have the most potential for disruption, either because they are new, or because they are becoming increasingly common, include:
- Decentralized wastewater treatment: The development of smaller, decentralized treatment technology has the potential to improve levels of sanitation and access to clean water around the world. A number of universities and companies are working on practical solutions for sustainable, small scale wastewater treatment units.
- Phosphorus recovery: Economic, political, and environmental factors are already combining to make the recovery of this valuable nutrient from waste streams and sludges routine at commercial wastewater treatment facilities. Consultants are also turning their attention to phosphorus recovery at smaller scale installations, such as septic tanks and agricultural effluent.
- Wastewater mining: While the recovery of some key nutrients, such as phosphorus, is now common, an improved understanding of the scarcity of resources and moves towards the development of a true circular economy means that the next generation of wastewater treatment plants is likely to include physical, chemical, and biological systems to recover key materials (including carbon, nutrients, and rare metals) for reuse in processes as diverse as farming, food production, and industrial manufacturing.
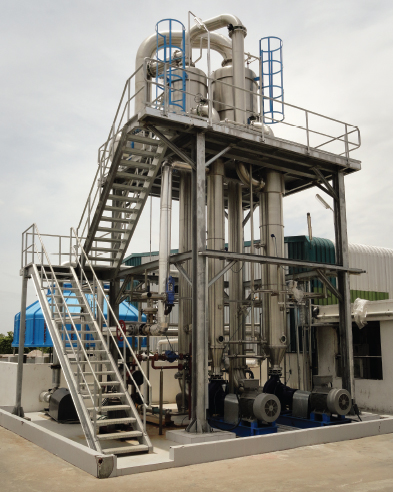
USING EXISTING TECHNOLOGY FOR DISRUPTIVE PURPOSES
There are many drivers for the adoption of all or some of these techniques in wastewater treatment, including environmental, economic, and social factors. However, the good news for companies wanting to evaluate and introduce such technology is that the techniques already exist.
For example, many of the processes described above involve some form of evaporation to concentrate residues for extraction and as part of the purification of wastewater streams. As heat transfer and evaporation specialists, HRS Heat Exchangers already produce a range of heat exchangers and systems that are suitable for any or all the above processes. The patented HRS Unicus series of scraped surface heat exchangers are particularly suitable for use in evaporation systems, such as those used for ZLD and material recovery.
The HRS evaporators used in ZLD systems are run at lower pressures to reduce the boiling point of the liquid, enabling multi-effect evaporation. In multi-effect evaporation, steam from a previous evaporation stage is used as the thermal energy for the next stage, which works at a lower boiling point. In this way, multiple evaporation stages are combined, delivering considerable energy savings. For many components, crystal precipitation is also favored at lower temperatures; so, lowering the evaporation temperature helps to boost product recovery rates.
The HRS ZLD process consists of an evaporation concentration phase where a concentrated solution is concentrated as much as possible. From that point on there are two possibilities:
- Concentration to maximum solubility without the formation of suspended solids. This is then followed by a cooling step which causes solids precipitation and separation of the solids which are formed; the liquid fraction is then returned to the evaporator. This method can be applied for a product that has a sharp change of maximum solubility with temperature.
- Concentration to just above the saturation point, followed by a separation tank where the solids and liquids are separated. The liquid fraction is then returned to the evaporator. This method can be applied for a product which solubility does not change too much with temperature.
Both the evaporation and cooling steps result in a high degree of material fouling on the inside of the equipment. To combat this, HRS Unicus Series scraped-surface evaporators are used, as they maintain thermal efficiency and remove fouling as it occurs in the evaporation process. In addition, HRS R series scraped surface heat exchangers are also used for cooling the crystal-loaded slurry that is obtained in the crystallization tanks.
FOR MORE INFORMATION
Located in Atlanta, Georgia, HRS Heat Exchangers is part of the HRS Group, which operates at the forefront of thermal technology, offering innovative heat transfer solutions worldwide across a diverse range of industries. With approaching forty years’ experience in the wastewater sector, specializing in the design and manufacture of an extensive range of turnkey systems and components, incorporating our corrugated tubular and scraped surface heat exchanger technology, HRS units are compliant with global design and industry standards. For more information, visit www.hrs-heatexchangers.com.
MODERN PUMPING TODAY, July 2020
Did you enjoy this article?
Subscribe to the FREE Digital Edition of Modern Pumping Today Magazine!
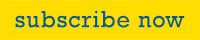