In oil fields around the globe, a giant silhouette can be seen methodically and rhythmically raising its head into the sky and dropping back down to earth, with each motion pumping gallons of vital oil from deep underground up to surface. These familiar beam pumps, also known as a pumpjack or—more colorfully—as a nodding donkey, are at the heart of oil field production in hundreds if not thousands of myriad locations.
However, the conditions in which one can establish an oil field are not always the best environment for the machinery, controls, and drives necessary to keep production flowing. In fact, maintaining the precision and efficiency of these machines in harsh surroundings is one of the main challenges as oil exploration expands into new territories.
A MORE EFFICIENT NODDING DONKEY
Invertek Drives has supplied products to a number of oil field beam pumping projects in China, reducing energy consumption by more than 10 percent. Optidrive P2s are being used to control the pumping rate on beam pumps in the Qinghai oil field energy saving retrofit project. Qinghai oil field is located in the Qinghai plateau, Qaidam Basin.
Founded in 1955, it was one of the earliest oil fields to be established after the founding of the People’s Republic of China (PRC). Located at an altitude of 8530 to 9842 feet (2600 to 3000 meters), it is the highest oil field in the world. The surrounding natural environment is extremely challenging, so a key requirement for the project was to achieve a high level of reliability from the drives.
THE RIGHT CHOICE
Optidrive P2 was chosen for this project because the user recognised the benefits arising from its superior performance, unique motor control, and strong reliability. This is particularly important in harsh environments such as Qinghai.
The advanced performance, features and functionality of Optidrive P2 offers excellent motor control capabilities with easy to program, flexible parameters and technology that is so sophisticated it can run in open loop without the need for position sensors, inefficient dynamic braking resistors, or complex regeneration systems normally associated with this type of application. The system is simple to install and free from DC bus voltage fluctuations and voltage surge problems.
THE P2 IN QINGHAI
The customer in the Qinghai project had previous experience of using Invertek’s variable speed drives and trusted the P2 to deliver significant energy and maintenance savings—so far thirty-eight Optidrive P2s have been installed at Qinghai and have run smoothly since December 2012.
“The volume of oil that can be extracted from any oil well will vary depending on the underground conditions and the age of the well. The P2 can detect the slightest changes and will adjust the speed of the pumping cycle accordingly, thereby optimising pumping output and energy efficiency. The P2 can also maintain the motor torque within pre-set maximum and minimum limits ensuring that the beam pump can be operated smoothly throughout each cycle reducing mechanical stress and saving energy on a per cycle basis,” adds Invertek Drives Technical Manager Kes Beech.
“The P2 enclosure is also rated to IP55, making it the perfect self-contained product for this type of application.”
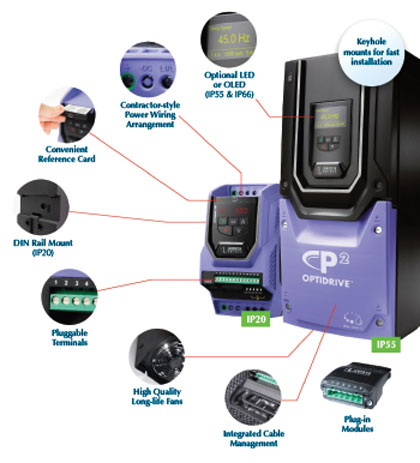
FUTURE PROOFING
Regenerated energy is stored within the mechanical system as kinetic energy during the pumping stroke and reused later, when required. This approach provides a reduction in the maximum motor current of 40 percent during normal operation of the counterbalanced pump, whilst also reducing the starting current and can result in the average running current being reduced by more than 10 percent.
Using Optidrive P2 drives also ensured that the site was “future proof” thanks to the inbuilt PLC function, which provides opportunities to develop bespoke beam pump operating functions in the future. A further consideration for our customer was the access to DC Bus terminals; in the future this may allow some of the operating power to be developed from Photovoltaic sources. This is particularly important in energy efficiency projects such as Qinghai.
COMMITMENT TO DRIVE TECHNOLOGY
Invertek Drives has a long history of supplying variable speed drives to oil field applications in China and many other countries around the world including Canada, Brazil, and Venezuela. Its state-of-the-art UK headquarters houses specialist facilities for research and development, manufacturing, and global marketing. All operations, including research and development, are accredited to the exacting customer focused ISO 9001:2008 quality standard.
- Short-term benefits: P2 offers cycle by cycle variation in speed resulting in energy savings of up to 10 percent.
- Long-term benefits: Optidrive P2 has the ability to vary the overall speed of a pumping system in line with the changing characteristics of a particular oil well to maximise pumping output and optimise energy usage. P2’s smooth operation also reduces mechanical stress and hence the need for maintenance.
The company’s products are sold globally by a network of specialist distributors in over eighty different countries. Invertek Drives’ innovative Optidrive range is designed for ease of use and meets with recognized international design standards for CE (Europe), UL (USA), and CTick (Australia).
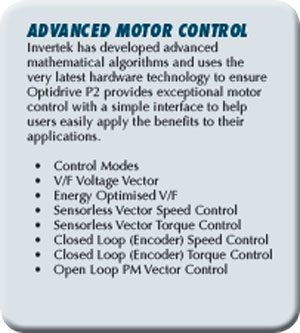
DRIVE SYSTEM EFFICIENCY
With today’s ever increasing energy costs, efficiency has long been a key factor in relation to drive system component selection. In many cases, an efficiency figure can be arrived at by simply multiplying the efficiencies of the various components together to find a combined efficiency figure, however this may not tell the whole story. The efficiency of components such as drives, motors and gearboxes can vary considerably with speed and load, hence simply combining the “headline” efficiency figures can often be very misleading. In reality, the efficiency curves for the whole system should be overlaid, to provide a true efficiency figure for the system across the desired speed and load range.
Modern AC inverters will typically have an electrical efficiency of around 98 percent, which represents the different between the electrical output power compared to electrical input power only. A further factor that is often overlooked is the efficiency of the motor control strategy employed by the drive. This can have a significant effect on the overall system efficiency, and is often not considered when energy saving calculations are made.
Optidrive P2 has been designed to work with both standard induction motors, which typically meet the IE2 efficiency standards currently in place in Europe, and the latest generation of high efficiency PM motors designed to meet the future IE4 requirements.
This means that an efficient drive can be purchased now, allowing for a future update of the motor without requiring a change to the installed drive. Furthermore, Optidrive P2 has been designed and developed to work with all PM motors, and control them with optimum efficiency, providing the most efficient PM motor control available.
_______________________________________________________________________
ABOUT THE AUTHOR
Dr. YongKui Man is the CEO of Invertek Drives China Ltd. and professor of electrical machines and drives at Northeastern University in Shenyang. Invertek Drives Ltd. is dedicated to the design, manufacture, and marketing of electronic variable speed drives for controlling electric motors. For more information, call 44.0.1938.55.68.68 or visit www.invertekdrives.com.
_______________________________________________________________________
MODERN PUMPING TODAY, October 2013
Did you enjoy this article?
Subscribe to the FREE Digital Edition of Modern Pumping Today Magazine!
