Before we elaborate on the specific steps in the training and learning processes, it’s best to just re-emphasize an important fact: Accepting that the most important learning process begins at graduation should be the first and perhaps most important realization in an engineer’s training. While training plans will, of course, differ for different areas of specialization, it might surprise that the principles embodied in the specifics we chose to list here for “reliability improvement of fluid machinery” apply to every aspect of engineering specialization. The author’s experience fully supports the belief that meaningful training should progress in four or more distinct phases.
1. PHASE 1: READING TRADE JOURNALS
In the interest of continually obtaining work-specific technology updates and related training, the value-adding engineer must peruse trade journals. He or she should scan and retain (file electronically) articles on topics of potential interest. We might use our imagination to interpret scanning as viewing information on paper or by way of electronic scanning, preserving, and retrieving. One could also make copies of, or read, or tear out pages, from relevant trade journals. As mentioned, material of potential interest would be organized, filed, and electronically catalogued for rapid retrieval.
Companies with well-defined training plans would involve all employees that can benefit from the way these plans are implemented. The manager or supervisor would arrange for applicable Trade Journal 1 to be given to employee “A”. In reviewing this trade journal, “A” notices an article dealing with shaft couplings and sends copies to colleagues/co-workers “B”, “C”, “D”, etc. Applicable Trade Journal 2 starts on the desk of employee “B”, who notices articles on pivoted shoe bearings and wear-resistant V-belts. “B” makes copies of these two articles and sends them to “A”, “C”, “D”, etc.; likewise “C” sends articles of interest to “A”, ”B”, “D”, ” E”, and so on.
The once-per-month task of culling and reviewing suitable articles or conference proceedings may typically take ten to fifteen minutes and allow each participant to acquire a data bank of relevant cross-references. This author recalls an experience when, decades ago, he looked for a reference article and then called its writer. He or she asked for—and cheerfully received—priceless guidance on a subject matter related to the writer’s topic. That kind of networking proved of great value and became the anchor point for other communications.
2. PHASE 2: TECHNICAL BOOKS (ONE PAGE PER DAY, OR 200 PAGES PER YEAR)
Relatively few engineers purchase, or thoroughly read, technical texts after completing their formal education. Fortunately, however, there are training-oriented employers who encourage their staff to read and absorb relevant technical texts. For example, one such employer explained that his responsible professional employees are encouraged to purchase as many books as they can reasonably assimilate or digest in a year’s time.
During subsequent performance appraisals, the effectiveness of this policy was validated and reaffirmed on many occasions. Another company purchases pertinent technical texts and requires each technical employee to read a page per day. To the extent feasible and reasonable, these professionals are then asked to jot down what they discern as differences between their guidelines, work processes, hardware details, failure frequencies, maintenance intervals, etc., versus what others (and, in particular, competitors) are doing in these fields of endeavor.
The training value of this approach is immense. Certainly, the return on the investment of the time it takes to read a page a day and to make a two-sentence notation each week is huge. There can be no doubt that this well-focused training is priceless and benefits all parties for decades to come.
3a. PHASE 3, PART A: TRAINING THROUGH “SHIRT-SLEEVE SEMINARS”
In the 1970s and in pursuit of Phase 3 Training, one highly profitable multi-national company arranged for its equipment reliability technicians and engineers to share the responsibility of making seven- to ten-minute presentations at the conclusion of each routinely scheduled and mandatory safety meeting. The presenters would educate themselves on such topics as “how to properly install a centrifugal pump,” or “why steam turbines must be thoroughly pre-heated before full-speed operation.” Following the presentation, the presenter would distribute written copies of these one or two-page guidelines laminated in plastic. Plant management made sure that reasonable expectations were met. Therefore, enlightened managers made it clear that they wanted these guidelines to be read, consistently used, and fully adhered to. Reliability engineers, mechanical work force, and operating personnel were told that compliance was mandatory, not optional.
In this manner, the “shirt sleeve seminar” presenters taught themselves by networking and communicating with knowledgeable people inside and outside the facility. As they made their presentations, they transferred their findings to the entire plant. At this location, equipment failures due to human error and other causes were minimized, and everyone profited from the well-tested approach. There should be no reason for not adopting it elsewhere with equal success. Minor modifications may accommodate many different needs.
3b. PHASE 3, PART B: PRESENTING TO THE PLANT STEERING COMMITTEE
The most successful process plants often have three division managers report to the plant manager. The division managers oversee and manage the disciplines manufacturing, human relations, and process-technical. Under the manufacturing division manager, we have seen two department managers, one for operations and one for maintenance. These two managers are appointed with the understanding that they will be asked to switch their respective positions when asked to do so by the plant manager. This “hat-switching” may be ordered in random intervals of three to fifteen months, and with at most eight hours advance notice. The effect has always been of staggering importance and benefit.
Hat-switching resulted in both department managers rapidly achieving full competency in each other’s original discipline of choice. They strengthened their bonds of cooperation and never practiced the destructive game of “one-upsmanship,” that is, the dangerous finger pointing that so often undermines trust and progress. Reporting to the technical manager are department heads for new projects, reliability engineering, and others. Section Heads report to department heads. Similar organizational arrangements report under the HR division manager.
The plant manager is supported by a steering committee whose membership includes the three division managers and several department heads. This steering committee invites staffers below the level of section head to make ten- to fifteen-minute presentations on how they do their job, what they would do different if it were within their power, what they would do if they were given $10 million and would have to spend the money for improvements, and how they personally have added value to the enterprise. These presentations monitor the pulse of an organization. They inform and even teach managers, enhance the sense of self-worth of the employee, and give high visibility to the presenter.
4. PHASE 4: OFF-SITE MEETINGS AND TECHNICAL CONFERENCES
It may be noted that Phases 1 through 3 cost the employer next to nothing. The degree with which employees carry their load should determine the extent to which they will be involved in plans that include the next phase: Phase 4, offsite training. By mutual agreement between employer and employee, the person may now progress to receiving Phase 4 training. He or she would attend conferences and workshops that require fees, travel expenses, and accommodations paid for by the employer. After an employee returns from such offsite training, she or he will have to compose a 300-word report on things learned. The report must explain how these learnings could be used at his or her place of employment. One facility found that it was best to link or combine handing in this brief report together with the employee’s expense statement.
The report is later disseminated throughout the company. Report writers benefit from refreshing their recollections, as will the various technical employee-recipients and their managers. Name recognition is established, and the contributor’s sense of accomplishment is certainly enhanced in the process. Everyone benefits from the experience. The greatest hazard is that managers or supervisors are lax in their enforcement of having these one-page-maximum reports written and issued. Non-enforcement sends the message that nobody cares, and that the employer is happy with maintaining a below-average peer rating. It seems the employer’s claim to optimizing the development of technical employees should not have been taken seriously.
ROLE STATEMENTS AND FUTURE TRAINING PLANS
Already during a job interview engineers about to graduate from college would be wise to explore the role they expect to fulfill. Very soon after starting work the engineer should express strong interest in receiving a written role statement from his or her superior. Role statements define expectations. If no such statement is forthcoming, engineers are encouraged to put their understanding on paper and ask the responsible manager for review, input, recommended changes or concurrence. Unless there is agreement on the engineer’s role, “performance exceeding expectation” is as improbable as the same person simultaneously dancing at two wedding receptions located 7,000 miles distant from each other.
Likewise, during the job interview, an engineer about to graduate should ask about the training opportunities made available or endorsed by the prospective employer. The interviewee must have a goal in mind and this goal must involve professional growth and learning. Learning is obviously a two-component process. While one party offers it and the other absorbs it, the ultimate benefits are shared by both. That being the case, each has a commitment to make and to honor. Serious forethought and cooperation are needed to achieve optimized professional training.
And one more thing: Many opportunities will present themselves to the motivated technician whose formal schooling did not go beyond High School or past a two-year college. No worry, though, because a good non-degreed technical person will add far more value to an enterprise than an indifferent, often disruptive, or highly opinionated engineer. Role statements are helpful to all. Again, role statements define expectations.
As an example, a company could identify a self-motivated employee and ask this employee if he or she would be willing to be the custodian of an electronically stored and searchable engineering library. In the case of reliability professionals dealing with turbomachinery, pumps, gears, shaft couplings, etc., they would then be asked to identify useful Technical Conference Proceedings, published articles, and related information on the chosen range of topics. As mentioned before, the material needs to be indexed and, in one form or another, made accessible to one’s peers and other individuals that would be helped by the reference material.
During performance appraisals, the employee and the manager, reviewer or performance appraiser would make an objective assessment of accomplishments by way of comparison with the previously agreed-upon role statement. Such an assessment would comprise all pertinent training issues and would obviously include measuring the employee’s progress regarding reading and disseminating technical material.
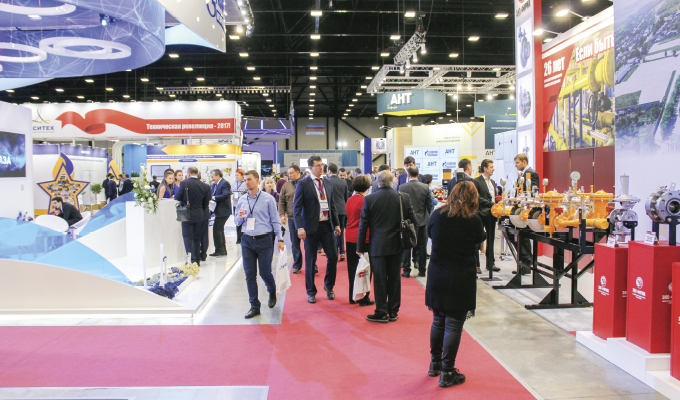
FAVORABLE RESULTS ANTICIPATED FROM ACQUIRING A MARKETABLE SKILL
By accepting help and by being willing to help others succeed, engineers will prosper. Moreover, they will gain an enhanced sense of self-worth if they truly pursue training that adds value. Engineers who succeed in acquiring a marketable skill both during formal studies and after graduating from engineering school can face the future with considerable confidence. Be sure to catch the two key words: Marketable skill.
Self-motivated engineers who implement and stick to the approaches briefly described here are very likely becoming employees who offer solutions to problems. Instead of becoming folks expressing “concern” over potential problems, they will delineate the discrete steps needed to address these “concerns” by actions that will avoid problems.
In conclusion, here are a few more things to ponder:
- Certainly not all that is labeled education is beneficial. Some education can be so academic as to lack substance; it would not pass a balanced person’s definition of a marketable skill. Training is a form of education. Take charge and make it relevant.
- Solving problems is more valuable than merely voicing concerns. Having a balanced approach allows us to see how far to go with an investigation, specification, or implementation.
- Don’t just wait for skill-enhancing training opportunities to present themselves. Instead, take the lead in creating some of these opportunities. Virtually all marketable skills are acquired through proper response to meaningful training. True focus and the acquisition of marketable skills will get us through life better than a mere education or a smattering of unfocused flavors of the year.
- Selecting a profession, craft, trade, or job simply because it is paying well is generally a mistake. Developing a passion for a job is equally inappropriate because spirituality and family should rank higher.
- Your work need not be of the style and substance that the company will go out of business when you leave. It should, however, cause fellow employees to take note that you are no longer there. Yes, you carried your fair share of the burden and you had been adding much value.
- As a new employee and while on your way to work every day, make it your goal to add value. Think ahead, dwell on the specifics of adding value on that day. Then, on the way home from work, ask how successful you’ve been in adding value to the enterprise. If you have not met your mark or personal goal, resolve to adjust on the following day.
- And finally, remember that in your job you will encounter designated leaders who either cannot or will not lead. When this happens, don’t give up. Only dead fish will always swim downstream. Where the flow is in only one direction and where there is nostalgia for a mis-remembered past, the future is murky.
Heinz P. Bloch resides in Montgomery, Texas. His professional career commenced in 1962 and included long-term assignments as Exxon Chemical’s Regional Machinery Specialist for the United States. He has authored or co-written over 800 publications, among them twenty-four comprehensive books on practical machinery management, failure analysis, failure avoidance, compressors, steam turbines, pumps, oil mist lubrication, and optimized lubrication for industry. Bloch holds a B.S. and an M.S. degree (cum laude) in mechanical engineering from Newark College of Engineering (NCE). He is an ASME Life Fellow and was awarded life-time registration as a professional engineer in New Jersey. He is one of ten inaugural inductees into NCE’s Hall of Fame, which honors its most distinguished alumni.