By Raffaello Leptratti, Siemens
By now most people have heard about digital twins, but many still struggle to articulate how the technology can benefit their business. Most understand the technology—that digital twins are virtual models that allow for the digital simulation, validation and optimization of parts, products, and processes. However, when people think of digital twins, they often only consider how it can be used to speed product development, an early and powerful use case.
MONETIZING THE DIGITAL TWIN
Advanced users of digital twins know that when connected with a digital thread through an industrial Internet of Things (IoT) platform, the technology transforms the entire value chain. A fully integrated, “closed-loop” digital twin can extend from product design to production, to logistics, to field performance and service, including entire manufacturing facilities and parts of the supply chain. This closed-loop digital twin integrates product digital twins, production digital twins and performance digital twins, and they continuously gather and deliver data back to where it’s needed in the value chain.
Translating knowledge of these technological capabilities into business benefits is crucial to return on investment. To start that translation, here are the top five benefits you can achieve by implementing a closed-loop digital twin.
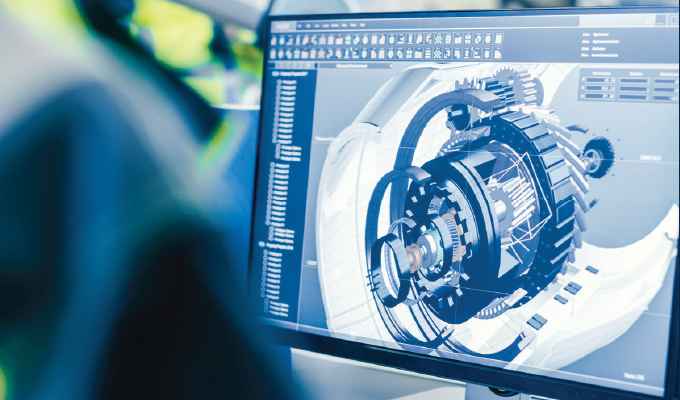
1. FEEDBACK LOOP
The feature that enables the performance digital twin is the feedback loop, which delivers the most potent benefit derived from a closed-loop digital twin. The feedback loop allows for real-time performance data from the production line or products in the field to be immediately—and continuously—applied to product design, manufacturing engineering and production. With an integrated digital twin, the feedback from each part of the process communicates real-time data through the system to other parts of the process, helping to identify areas of improvement—and across the value chain, which enables faster decision making and stronger collaboration. In a marketplace defined by fast-changing customer demand and the need for continuous improvement, manufacturers must become increasingly agile and flexible in order to survive and thrive. The instant, automatic feedback combined with enhanced collaboration helps them do so.
2. PRODUCT QUALITY AND INNOVATION
The most often cited benefit of digital twins is their increased competitive advantage. Most importantly, the feedback loop connects professionals’ ability to enable manufacturers to introduce new products to the market faster, but they also support innovation in other ways. Sensors on products in the field deliver vital data to engineers about the product during customer usage, enabling them to quickly identify ways to improve the product or create a new one before the customer realizes they need it. The ability to monitor product usage also enables product-as-service business models, whereby manufacturers sell the outcome, not the product. Aircraft engine manufacturers, for example, sell flying time, helping customers reduce capital budgets, and manage maintenance, repair, and overhaul work. The data also allows manufacturers to provide end customers with information about how to most efficiently use and continuously improve their use of the product.
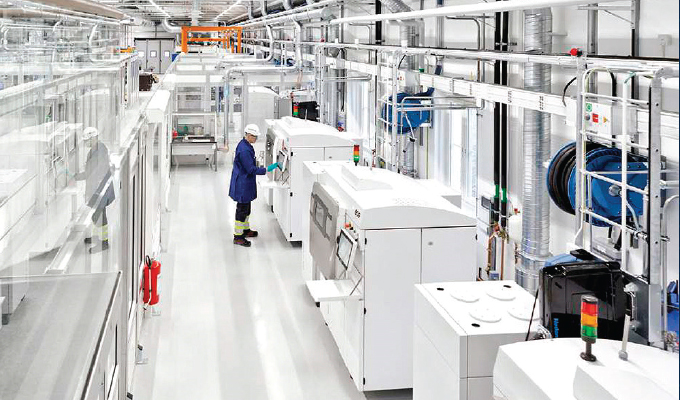
3. PRODUCTION QUALITY
A digital twin can improve quality and compliance of product designs and production processes by allowing multiple, quick, what-if scenarios and by validating designs and processes virtually. With the industrial IoT connecting your product and production digital twins, you can almost instantaneously gather all the data a machine produces and compare expected vs. actual performance. As the production line is engineered or the product is manufactured, real-time data ensures quality by identifying out-of-spec products or equipment, which can help pinpoint anomalies, design flaws, defects, and so on, and allows for fast countermeasures. With a digital twin that is not connected with an industrial IoT platform, it is extremely difficult to centrally collect the relevant data and deploy the computing power to effectively process and analyze it.
4. PROCESS EFFICIENCY
Deploying digital twins on the plant floor environment drives efficiencies across the entire manufacturing process. Simulating every aspect of the plant eliminates the need for time-consuming physical prototyping, while also ensuring an optimal configuration of a plant’s layout, processes, and control systems during the design of a factory. Just as product digital twins can expedite product development, production digital twins can accelerate and validate manufacturing process planning and commissioning. Once the product and production twins are connected via an industrial IoT platform, actual production line performance data can be fed back to the virtual models. With this closed-loop, you can more quickly understand how to optimize the assets and work on the factory floor, which enables you to implement efficient processes, prevent costly downtime, optimize workflow, and predict when preventative maintenance will be necessary.
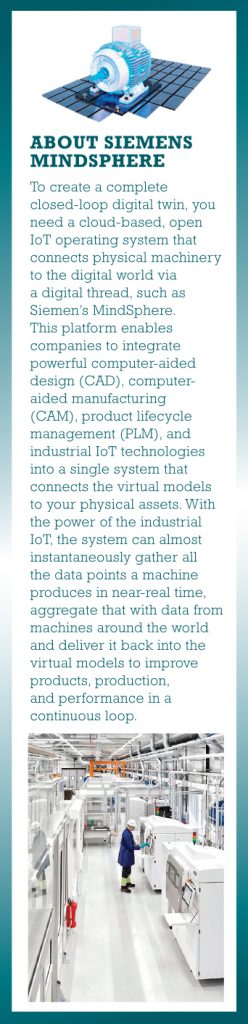
5. PROCESS STANDARDIZATION
You’ve likely heard the adage “without standards, there can be no improvement,” which prompts manufacturers to identify and standardize critical elements and steps in processes to ensure quality and to determine how the process can be improved. With a digital twin, you can establish far more detailed process standards on how the product will be built and can monitor them more closely and in real time.
For example, a diagnostics provider, Affidea, leverages digital twins to drive standardization of its CT scanning process. With half of its 145 CT scanners at more than 230 diagnostic centers in sixteen European countries collecting imaging and radiation dose data, Affidea has identified ways to improve the process, so it can perform scans at the lowest radiation dose while maintaining diagnostic accuracy.
THE FULLY INTEGRATED DIGITAL TWIN
While the thought of achieving all the benefits of digital twins might sound unattainable, it’s important to note manufacturers that are successfully implementing an integrated digital twin system and process do so one step at a time, but with a vision of end-to-end connectivity. As they reap the benefits with each deployment, they are building the manufacturing business of the future.
Integrated digital twin systems and processes are not merely nice-to-have functionalities that will convey a competitive advantage to those who deploy them. Instead, integrated digital twins will form the backbone of future manufacturing businesses, just as mechanization, mass production, and automation did in previous industrial revolutions. Be forewarned, creating an intelligent infrastructure where design, manufacturing, automation, and supply chain are seamlessly connected and in sync with customer demand is the prerequisite for delivering innovative products to market quickly and efficiently. Soon, every manufacturer will need to deploy an integrated, end-to-end digital twin strategy.
FOR MORE INFORMATION
Raffaello Leptratti is vice president of business development and marketing at Siemens. Formerly Siemens PLM Software, Siemens Digital Industries Software reflects the depth of software offerings across a broad spectrum of industry domains. Amid unprecedented change and the rapid pace of innovation, digitalization is no longer tomorrow’s idea. Siemens Digital Industries Software takes what the future promises tomorrow and make it real for its customers today. For more information, visit www.sw.siemens.com.
MODERN PUMPING TODAY, November 2019
Did you enjoy this article?
Subscribe to the FREE Digital Edition of Modern Pumping Today Magazine!
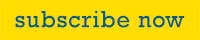