By Xavier Jauregui, Arc Machines Inc., and Matthias Schaffitz, Wolfram Industrie GmbH
In last month’s introduction to this series, we demonstrated how, in order to optimize the electrode for the respective process, extensive know-how about the tool is just as important as extensive knowledge of the area of application itself. In the following article, we’ll see how geometry also plays a critical role in tungsten electrode performance. It is significantly influenced by the grinding method used. For example, the surface is increased by abrasives with a coarse grain, which in turn ensures faster oxide evaporation. Furthermore, the roughness of the surface when processing with a coarse-grained abrasive varies from application to application.
GRINDING FOR A SMOOTH FINISH
Hand-operated and bench tungsten grinders are best left for preparing electrodes for manual GTAW applications, not mechanized processes. In an orbital TIG arc welding system with a modern power source with inverter and good arc start behavior, companies should use pre-ground tungsten electrodes that have been machined by robot-controlled CNC systems. These machines are able to produce the desired very fine surfaces.
In order to influence boundary layers, voltage drop, cathode spots, evaporation rate, or the relative exposed functional surface, the surfaces can be Ra 0.01 µm (0.4 micro inches) low, with high edge sharpness of the contour or 3.2 µm (125 micro inches) with perfectly burr-free flanks. High-quality, pre-ground electrodes made of tungsten also offer a dimensional accuracy of ± 0.05 millimeters at the tip diameter and grinding angle tolerances of ± 1 degree.
On the other hand, if a manual grinding machine is used to flatten the end of a pointed electrode, this leaves a microscopic burr without exception. If this burr breaks off during welding, it can get into the weld seam. For pharmaceutical, medical, nuclear, aerospace-related, and other critical applications, this often means that the workpiece has to be sorted out. To complicate matters, electrode point geometry affects the plasma cone’s shape, which has an effect on the weld bead profile.
OUTLOOK ON CURRENT RESEARCH RESULTS
Much of the previous plasma research in the field of electrode geometry is carried out using the spot-on-plate technique (welding spot on plate), in which an arc strikes a plate at 200 amps for two seconds. This technique does not represent the fluid dynamics (molten weld puddle behavior) that occur during orbital welding. It does not take into account the welding head that moves into the cold material from the weld seam, nor does it take into account the thermal conductivity and the preheating of the tube during the welding process.
Newer research, conducted under actual orbital welding conditions, incorporated more than 500 electrode configurations. Polished cross-sections of the welds were examined with a scanning electron microscope. Based on these results, suppliers of electrode and orbital systems can now recommend suitable tungsten solutions for specific applications. Narrow welds with a weld seam of 2 millimeters in outer diameter, for example, benefit from the increasing and constant arc pressure from the tungsten electrode, which is achieved by a mixture of mixed oxides, in which different oxide properties are combined.
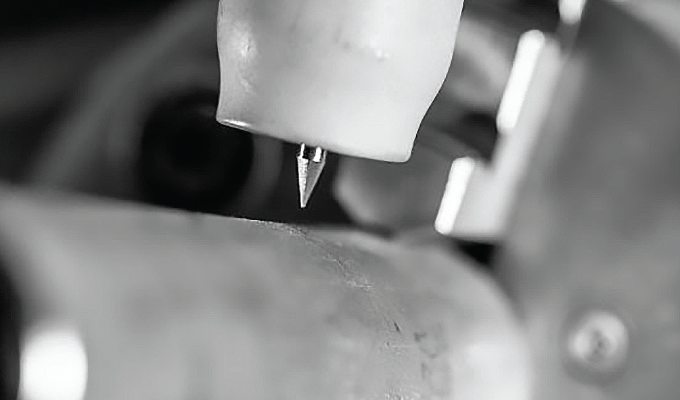
These research results also help to solve previously hidden problems. For example, recurring deviations in the welding process at a company led to a significantly higher reject rate. To reduce this, extensive measures have been taken to find the cause. The investigation team re-calibrated the power source and welding head and inspected every point in the circuit. This did not improve the welding results though. However, the team never thought of the consumable component in the circuit: the electrode. The change to higher quality, pre-ground tungsten electrodes solved the problem.
Depending on the respective operating conditions, cumulative deviations caused by these factors can easily lead to a total heat input that deviates by as much as 5 percent under otherwise identical ambient conditions. While that might be acceptable now, it won’t likely be acceptable within the next decade when end users require component fabricators to provide more complete data records and analytics.
CONCLUSION: HIGH QUALITY TUNGSTEN ELECTRODES OPTIMIZE COST EFFICIENCY
With every orbital welding process, high-quality electrodes reduce the overall welding costs. Test runs under clean room conditions confirm that with optimized tungsten electrodes, more than 650 arc starts can be easily implemented without delays in arc development. Instead of changing the electrode at the start of every shift, welders can use an electrode for several days. For example, one company recorded an arc duration of twenty-seven hours with a single electrode.
Conversely, unspecific, second-class tungsten electrodes only deliver an average of about 110 arc starts and therefore have to be changed significantly more frequently. The associated labor cost alone wipes out any money saved on the purchase price. Taking into account scrap and welding defects, it is therefore desirable to carefully select an electrode. This is the only way to produce high-quality weld seams that are still cost effective.
FOR MORE INFORMATION
Xavier Jauregui is vice president of the technical area of Arc Machines Inc. and Matthias Schaffitz is managing director of Wolfram Industrie GmbH. Founded in 1976, Arc Machines, Inc. is an American company that designs, manufactures, and distributes advanced automated orbital welding equipment, systems, and services. Wolfram Industrie develops, tests, and produces innovative tungsten and molybdenum products to meet industrial requirements. For more information, visit www.arcmachines.com and www.wolfram-industrie.de.
MODERN PUMPING TODAY, November 2020
Did you enjoy this article?
Subscribe to the FREE Digital Edition of Modern Pumping Today Magazine!
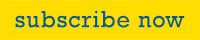