By Xavier Jauregui, Arc Machines Inc., and Matthias Schaffitz, Wolfram Industrie GmbH
Quality pays off: For example, nobody would equip a Formula 1 racing car with inexpensive all-weather tires. In order to achieve a competitive speed, the vehicle should lie optimally on the track and be perfectly matched to the respective track conditions. Even with TIG arc welding, the tool used for high-quality welds must be adapted to the respective application—and yet many welders use second-class tungsten electrodes that are not matched to the respective process. This choice leads to a deterioration in the welding results due to low electrode quality. However, efficient orbital welding requires a tungsten electrode with an individually adapted tip geometry and surface roughness to match the correct shielding gas. For optimal weld seams, other factors must also be taken into account that influence the arc start properties, arc stability, total heat input, and correspond to the characteristics of the weld seam.
The adaptation of all parameters to the respective TIG application enables a service life that is up to six times longer and thus resource savings of more than 350 percent compared to the use of non-specific no-name electrodes. However, this can only be achieved with the appropriate know-how, the correct selection, and the use of high-quality tungsten. Three central elements can be optimized in this way: the welding process itself, the chemical properties of the tungsten alloy used, and the grinding process for the electrode tip.
INCREASING DEMANDS ON THE WELDING PROCESS
In today’s industrial environment, many manufacturers and processors of metal tubes and pipes are faced with stricter requirements for weld seam properties than was the case in the past. The semiconductor industry, for example, needs narrower weld seams with fine surfaces on the inside of stainless steel pure gas pipes. These tubes transport high-purity gases that are toxic, flammable, or corrosive, which is why the weld seams produced using the fusion welding process must be corrosion-resistant and cleanly processed in order to enable trouble-free flow. In addition, designers from all technical disciplines are increasingly pushing the limits of technical feasibility, for example by reducing pipe wall thicknesses to the necessary minimum. The clean processing of the weld seams is, therefore, becoming increasingly important with regard to the safety and service life of the products.
As the industry continues to evolve and adapt its processes, welders are also finding that their entire work environment is subject to high competitive pressure. Using FMEA (Failure Mode and Effects Analysis) and data analysis of the process variables, the previously underestimated hidden costs when using orbital systems were identified—for example, the production of scrap, reduction in system availability and frequent replacement of the electrodes. This drives the total cost of ownership up, although at the same time it would save as much money as possible. This includes avoiding premature wear of the tungsten electrode and irregularities in the machining process that can result from the use of different tungsten alloys when using electrodes from different manufacturers.
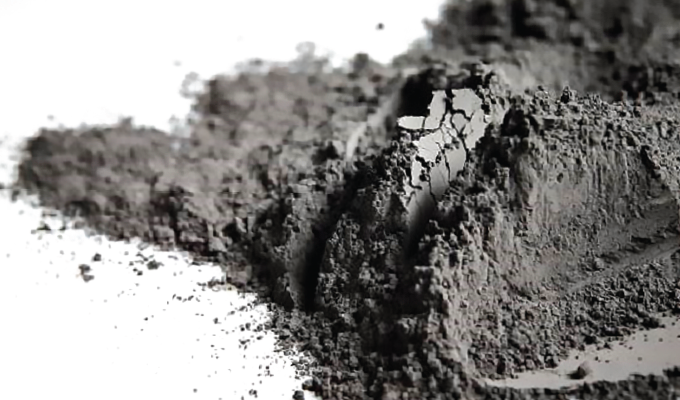
PROPER CHEMISTRY THROUGH POWDER METALLURGY
Another important element for the quality of an electrode is its chemical composition. To improve electrode performance, dopants in the form of cerium, lanthanum, zirconium, thorium, terbium, and yttrium oxides are often incorporated into tungsten electrodes. Such oxides lower the electron work function—measured in electron volts (eV). For example, pure tungsten has rating of 4.5 eV, whereas a 2 percent seriated tungsten has an eV of 2.8. By lowering the eV value or increasing the ionization potential, the oxides improve arc starting performance and arc stability.
However, the influence of this variable on the welding result is often underestimated and most companies consider the tungsten electrode as a static component. In fact, as soon as the welding current flows, the electrode becomes a dynamic subsystem, the parameters of which influence the properties of the arc significantly. Specifically, the heat of the welding arc causes oxides to migrate from the relatively cooler core of the electrode to the hotter tip. There, the oxides separate (evaporate) from the base element and leave a film on the electrode tip. Small tolerances in the grain size, the purity of the elements, and the composition ratio are essential to ensure a consistent oxide movement and evaporation rate, which in turn leads to a consistently high ignitability.
Because the melting points of the materials used for the electrodes can vary substantially—tungsten melts at 6,191 degrees Fahrenheit (3,422 degrees Celsius), cerium oxide at 4,352 degrees Fahrenheit (2,400 degrees Celsius)—the electrode manufacturers rely on the powder metallurgy process. Specific, extremely fine tungsten grain sizes are mixed in order to achieve a homogeneous oxide distribution in the matrix. After this process, the tungsten and the oxide powder are pressed together by isostatic pressure, so that a uniform density and microstructure are created. As a result, the brittle and unconsolidated electrodes are sintered for several hours in a high-purity hydrogen environment and at controlled temperatures. After sintering, the electrodes can be forged to their final shape, which further optimizes the grain structure. The complexity of the tungsten electrode manufacturing process offers many opportunities for error, which explains the performance and cost differences between brands. Therefore, extensive know-how about the electrode is required on the one hand, but also extensive knowledge of the area of application itself, on the other hand, in order to be able to optimally adapt the tool for the respective process.
A LOOK AHEAD
In next month’s conclusion, we’ll examine the critical role geometry plays in tungsten electrode performance as well as results from newer research that has been conducted under actual orbital welding conditions.
FOR MORE INFORMATION
Xavier Jauregui is vice president of the technical area of Arc Machines Inc. and Matthias Schaffitz is managing director of Wolfram Industrie GmbH. Founded in 1976, Arc Machines, Inc. is an American company that designs, manufactures and distributes advanced automated orbital welding equipment, systems and services. Wolfram Industrie develops, tests, and produces innovative tungsten and molybdenum products to meet industrial requirements. For more information, visit www.arcmachines.com and www.wolfram-industrie.de.
MODERN PUMPING TODAY, October 2020
Did you enjoy this article?
Subscribe to the FREE Digital Edition of Modern Pumping Today Magazine!
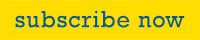