Centrisys/CNP recently completed a 34,000 square-foot building expansion, including an upgrade of its balancing equipment with a first-of-its-kind centrifuge balancing bunker in the interior of the building. Below, Michael Kopper, the CEO and founder of Centrisys, and Bill Fairbairn, the company’s vice president and building expansion manager, discuss what the Centrisys/CNP Manufacturing and Service Campus means for their manufacturing capability and for the services they can provide customers.
MPT: What led to the creation of the Centrisys/CNP Manufacturing and Service Campus?
Bill Fairbairn: The new facility, located in Kenosha, Wisconsin, consists of three buildings totaling 130,000 square feet. In 2016, it became apparent that the capital equipment manufacturing building was running out of workable space and needed an expansion.
Michael Kopper: As the decision-making for the extension evolved, the addition of a next-generation balancing machine and bunker was logical. The safety of our employees, along with the assurance that every centrifuge we build and service is balanced correctly, was well worth the added expense.
MPT: What role does the balancing bunker play in the new facility?
Michael Kopper: Because the balancing bunker is a first-of-its-kind solution, aimed at creating higher safety standards and increasing manufacturing productivity as well as efficiencies, a company committee was formed to design and build the bunker space and determine what equipment would work best.
We’ve been doing this type of work for a long time; centrifuge manufacturing and service have been our focus since the beginning. We had a thorough understanding of what we wanted and what the industry needed. Having enough workspace in a shop is important to eliminate errors during the manufacturing process. No one likes to work in a space that’s too crowded.
Underestimating the power of accurate balancing for a centrifuge is a big mistake. There is a tremendous cost to customers when a centrifuge is not in balance. High vibrations cause premature damage and wear to the centrifuge parts and structural components, creating higher repair costs and unnecessary process downtime.
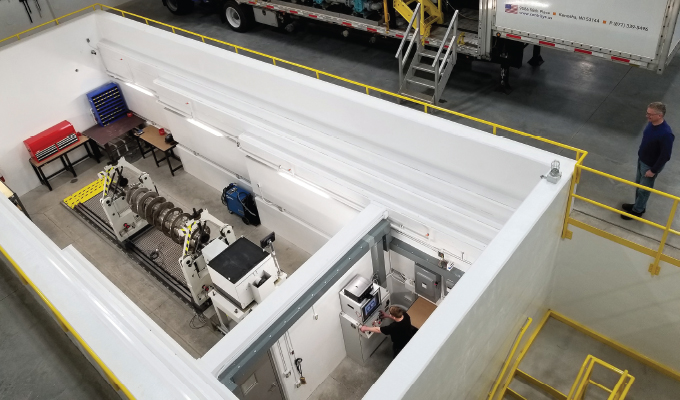
MPT: How did Centrisys’s partnership with Schenck USA Corp. factor into the upgrade?
Bill Fairbairn: We chose Schenck’s HM7U for the upgrade. It has stronger supports and higher dynamic load capabilities; we can balance over- operating speed on machines with a diameter of 44 inches or greater. We can handle larger and heavier rotors, so this is the natural next step for manufacturing and servicing next generation centrifuges.
The HM7U has a full range of safety features for all protection classes. The bunker isolates the operator in a protected control area and includes video monitoring to see into the balancing areas without the employee needing to be in proximity to the running equipment. Cranes are installed overhead to place parts and components in the balancing cradles. This set-up is something in which our team takes great pride, as it is world-class.
MPT: How do you foresee the new facility encouraging the company’s growth?
Bill Fairbairn: The expansion has allowed us to build larger and greater numbers of centrifuges, along with different types of environmental process equipment.
Michael Kopper: As the only U.S. manufacturer of decanter centrifuges in all environmental dewatering and thickening applications, I believe we’ve set the bar high for improved safety, productivity and efficiency. These are all essential to the higher standards we’ve established in our industry. I won’t compromise on any of these factors at a Centrisys facility. Our customers shouldn’t ever be required to compromise, either.
MODERN PUMPING TODAY, June 2019
Did you enjoy this article?
Subscribe to the FREE Digital Edition of Modern Pumping Today Magazine!
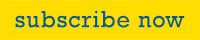