In an increasingly automated world, the importance of digital transformation, IoT, AI, and Industry 4.0 has been recognized within a range of industries, and though the food and beverage sector has been slow to adapt in comparison to others, it’s now catching up at a relatively quick pace.
The food automation market was valued at $11.29 billion in 2022, and is projected to register substantial growth over the coming years, reaching $18.60 billion by 2030. Automation provides a robust, future-proof solution to the many issues common in the food and beverage industry, such as lack of visibility and traceability, as well as the increasing need to generate cost/energy savings, reduce waste, and improve food safety.
Streamlining and optimizing production is equally as important as the above factors if manufacturers are to meet growing quality standards and consumer demand to ultimately boost profit, making automation a vital part of building long-term resilience.
So, what are the right ways to automate food and beverage facilities to effectively maximize benefits?
VISUALIZATION AS A PRIORITY
Visualization systems are quite simply becoming indispensable for food and beverage manufacturers due to their impressive capabilities, which cannot be rivalled by human labor or manual processes. These systems make it possible to analyze products coming down the production line, ensure that these have the right pieces and components, measure products in real time, as well as detect colors, foreign materials, and contamination.
This means that machine vision systems are capable of elevating quality control standards to a considerable extent, an issue of utmost importance for food manufacturers.
When it comes to food production, reducing the risk of errors and improving consistency is vital to ensure customer satisfaction, and crucially, to avoid product recalls. In the worst cases, misprinted or inconsistent labelling and packaging can be deadly or harmful for consumers, and lead to loss of revenue and brand credibility in the best of circumstances.
UNDERSTANDING THE POWER OF DATA
Automated vision systems ultimately provide access to data that allows manufacturers to be responsive and adaptable to better manage production on a holistic level. With access to historical data and trends, as well as custom reports, everything becomes easier, making optimizing operations within facilities a much more straightforward process. Manufacturers should seek to implement a network of systems and equipment that is all digitally interconnected, providing visibility across every aspect of a facility.
This would enable them to discover and address potential issues promptly and efficiently, making ongoing maintenance more effortless, too—having data at your fingertips means you don’t have to guess what the status of machines and pieces of equipment is.
Discussions regarding the power of so-called digital twins, that is, virtual copies of a food factory that utilize the Internet of Things (IoT), have focused on how these make it possible to experiment with how individual systems can work better in practice, therefore helping predict future performance and offering improved traceability, yet another way to generate cost savings.
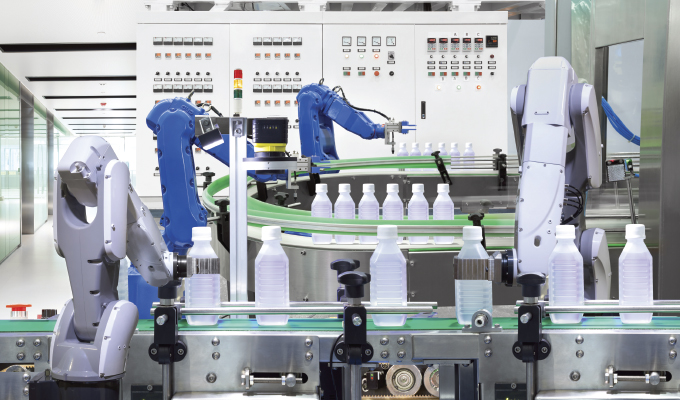
THE LINK BETWEEN AUTOMATION, SECURITY, AND CONTROL
Data collection is crucial in the context of security, too—the ability of control systems to allow manufacturers to have a clear view of their facility and control it from a remote location is nothing short of invaluable.
Automated food factories could have sensors with alerts across all equipment present, so if any of these pieces are not running at the right velocity, or are malfunctioning, owners will be able to quickly address the issue at hand. And from a security point of view, this becomes incredibly useful, ensuring neither external nor internal factors can compromise operations.
Automation can help ensure a facility is safe from both internal and external threats, including protecting it from human error. However, automated tracking also allows for the whole of the supply chain to be monitored and controlled, giving manufacturers the ability to track products from start to finish as they move through the supply chain. In turn, this enables them to resolve potential issues even after a product has left the production facility.
THE BENEFITS OF REPLACING HUMAN LABOR
It goes without saying that having people work in food and beverage facilities is inherently a risk. Individuals are the source of contamination: the more the people, the greater the risk.
Accordingly, the pandemic gave growth in automation in food factories a significant boost, with pressures around workforce availability and hygiene concerns demanding a faster transition—this is evidenced by a rise in robotics orders that was 56 percent higher in 2020 than in 2019.
What’s more, high rates of turnover can be particularly expensive for businesses. It’s ultimately about economies of scale. Profitability naturally goes up when replacing human labor, it helps build a more consistent and therefore future-proof business model, which also makes it easier to cater to demand and comply with regulations.
With extraordinary accuracy and speed, industrial robots can automate monotonous, repetitive tasks such as slicing, mixing or sorting ingredients, grinding, agglomeration, and packaging help ensures there’s no additional waste, which the food and beverage industry is knowingly particularly guilty of.
Automated facilities naturally increase in value, too. And when we discuss being future proof as a business, this is another element that should be considered. The cost of initial investment is always worth it in the long term.
FOR MORE INFORMATION
IAN HART is business development director of adi Projects, a division of multi disciplined engineering firm ADI Group. As a director and chartered engineer, Hart has twenty-five years of executive board experience, successfully establishing and developing customer focused, engineering based business, and delivering high value investments in both private and public sector organizations throughout the world. Providing specialist services to the food and beverage industry, adi Group can help manufacturers automate facilities in entirely bespoke ways, taking into account the varying needs of individual businesses. For more information, visit www.adiltd.co.uk.
MODERN PUMPING TODAY, August 2023
Did you enjoy this article?
Subscribe to the FREE Digital Edition of Modern Pumping Today Magazine!