By Talmage Wagstaff
A CIP, or clean-in-place, system is vital to the daily operations of any food manufacturing facility. Without a CIP system in place that is performing to specification, the facility risks fines, shutdown, and contamination of all products coming off the production floor. It is absolutely not the area to have a mechanical failure, because we can manufacture nothing else until the CIP system does its job.
What does a CIP system do, exactly? It pumps cleaning, rinsing, and sanitizing solutions through the product piping to clean and sanitize the lines for the next product to flow through it. This is done by CIP pumps pushing fluid through the lines to remove the debris and trash, while maintaining the turbulence throughout the system’s entire circuit. It is critical that the CIP pump provide adequate pressure for the job, because the cleaners and caustic need proper fluid speed velocity in order to rid the lines of the debris.
This means that proper pump size is imperative, and its operation needs to be completely to manufacturer’s specification so that they properly perform the cleaning, and there is no risk of any residual material in the lines causing a contaminated product. In a food manufacturing facility, contaminated product could cause food-borne illnesses, product recalls, and FDA mandated shutdowns while they investigate the contamination. These are all consequences that a manufacturing facility will have a hard time dealing with, and it has put food manufacturers out of business in the past.
WHAT IS THE CIP PROCESS IN A MANUFACTURING FACILITY?
The CIP process is closely monitored in food manufacturing. This is again due to the risk of food-borne illnesses, and federal guidelines specify the depth of cleanliness that they expect to be performed prior to a product being manufactured that will be available for human consumption. This process will be automated into the control software in most cases, which removes the element of human error.
The CIP process begins with what is known as the “push out” phase. This is where the CIP pumps use pressure to blow the residual product in the lines out, usually into a rework or scrap tank or drum-off line. Then, a pre-wash cycle will begin, which typically includes a non-chemical pressure test prior to any caustic or chemicals being introduced into the line. Next, the caustic wash will take place, followed by the first rinse cycle.
An acid wash will then begin, using nitric acid, or sometimes phosphoric acid. A final rinse will be administered, and then the sanitizing cycle will be performed to disinfect the product lines prior to the introduction of another food product or ingredient running through the material line. Sodium hypochlorite is typically the chemical used to sanitize the lines. As one can imagine, all of these highly corrosive chemicals running through lines, pumps, and valves can be incredibly taxing on the machinery, and a CIP pump has to be built to withstand some of the harshest conditions a manufacturing facility can deliver.
Between the heat, chemicals, and pressure that is necessary to clean and sanitize the facilities product lines, the strain that the CIP pumps are handling can lead to the complete exhaustion of the equipment if it isn’t maintained thoroughly, and in a timely fashion. Fortunately, like most pumps in manufacturing facilities, CIP pumps can be rebuilt to manufacturers specification and run like the day that they were purchased, given that they’re properly cared for.
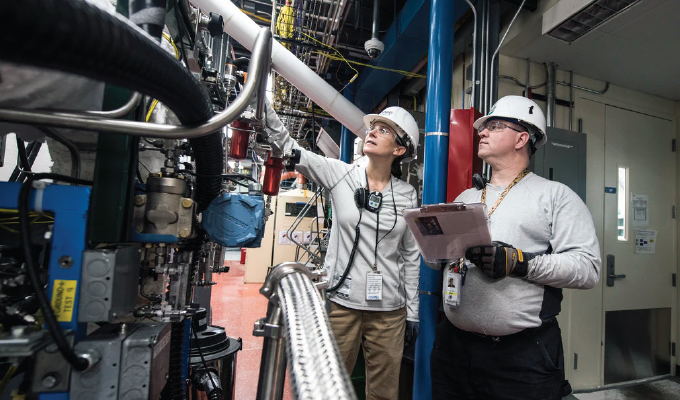
PROPERLY MAINTAINING THE CIP PUMP
CIP pumps take a brutal beating in the normal course of pumping hot chemicals throughout the production line circuit, and they need to be cared regularly. Caustic materials and high temperatures aren’t forgiving, so the proper preventative maintenance is critical for the life of the pump. A self priming pump must be used so that pump cavitation doesn’t occur, which will damage the impeller blades, or force the pump to run dry, which will burn up the pump seals.
A thorough preventative maintenance program for the CIP pumps in the facility should include the following:
- Ensuring that food grade lubrication is properly applied to all of the pump’s lubrication points.
- The rotor wing tips should routinely be inspected for metal to metal contact.
- The pump needs to routinely be checked for shaft spline wear and rotor spline wear.
- The pump should be inspected to ensure that there are no loose or worn gears.
- The gear teeth need to be inspected for improper wear.
- The front and rear pump seals should regularly be serviced and replaced.
- Check the bearings for shaft radial play.
PREVENTATIVE MAINTENANCE FOR CIP PUMPS IS COST EFFECTIVE
By performing these routine pump inspections, the majority of pump failures can be prevented. Replacing any and all worn components of the pump prior to failure helps to prolong the life of the pump, and to prevent critical breakdowns from taking place. This type of preventative maintenance requires a maintenance department to watch the pump in action, and to fully inspect the components regularly, in order to ensure that wear is spotted immediately.
The fact is that when pumps are properly maintained and run at the manufacturer’s specifications, the pump can often be rebuilt three or four times before it must be scrapped. That is an incredible amount of savings over a period of time, with the cost of the pump, production downtime to replace the pump, and the labor dollars required to perform the pump replacement. By properly maintaining the CIP pump in your facility, you’re preventing costly downtime, replacement costs, and the overall trouble that comes with critical part failure.
FOR MORE INFORMATION
Talmage Wagstaff is co-founder and CEO of RedList. Raised in a construction environment, Wagstaff has been involved in heavy equipment since he was a toddler. He has degrees and extensive experience in civil, mechanical, and industrial engineering. Wagstaff worked for several years as a field engineer with ExxonMobil servicing many of the largest industrial production facilities in the country. For more information, visit www.getredlist.com.
MODERN PUMPING TODAY, March 2021
Did you enjoy this article?
Subscribe to the FREE Digital Edition of Modern Pumping Today Magazine!
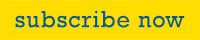