By SWPA Executive Director Adam Stolberg and John Wilson, Industrial Flow Solutions
As businesses head into the final fiscal quarter of 2020, they are setting their purchasing budgets for the year ahead. Below, SWPA Executive Director Adam Stolberg and John Wilson, president of Industrial Flow Solutions, lay out some important keys to consider if you plan on entering the market for a new submersible wastewater pump.
When choosing a submersible wastewater pump, what is the basic checklist a potential end-user should start with?
It is important to understand the type of lift station involved, the source of the wastewater, any solids the pump will be exposed to, along with a number of other criteria. A high-level check list includes understanding the:
- Make-up of the wastewater, potential solids size and materials. Critical to pump selection, confirm if the pump will be used for sewage water including size of solids or a combination of stormwater and sewage with potentially larger solids.
- Origin of the wastewater (i.e., residential, industrial, hospitality, hospitals, or prisons). This helps determine the type of effluent and potential for additional entrained foreign material.
- Need for pumps suited for explosive environment or chemical exposure.
- Application—whether the pump is for a new installation or a replacement.
- Space allowed for pump. Ensure there are no space restrictions that could affect the selection.
- Control scheme and if a back-up pump is available.
- Monitoring requirements for pump performance. Understanding the desired control approach and location of the lift station, i.e. a remote location with minimal regular inspections, will dictate the type of control and monitoring approaches needed.
- Technical requirements such as flow, total dynamic head, voltage, basin sizing, and other special needs.
A complete understanding of the above will allow you to select the correct type of pump used in a given application. In most cases, a shredder or chopper pump will hold an advantage to traditional “non-clog” pump designs. Shredder or chopper pumps reduce solid matter to a size, allowing these to pass through the pump to the bar screen at a municipal treatment plant; whereas a traditional non-clogging pump builds up solids in the eye of the pump impeller causing the pump to fail.
What characteristics should a purchaser look for in a manufacturer or distributor’s reliability? Where could one find resources to best assess a product’s reputation?
The goal of any application is to maximize uptime while minimizing total life-cycle costs. To help ensure your system operates to full performance, consider these key factors:
- Quality: Manufacturer’s proven track record of pump performance in a given application. Understand the installed base of a current manufacturer, including years of successful performance.
- Technical Expertise: Both manufacturers and distributors should have in-depth product and application knowledge in industries that they serve. A solid understanding of proper pump selection, pump operation, and application needs is essential for long term performance. These skill sets also help diagnose and address possible issues after installation.
- Responsiveness: Manufacturers and distributors should not only have components on hand to support the need for new pumps or spare parts to minimize disruption to facility operation, they should also offer proper service capabilities. Since periodic maintenance is required for submersible pumps, be sure to find a partner with local support and adequate inventory.
Also, be sure to validate past performance and capabilities of both the manufacturer and distribution. This can be done by requesting reference lists, contacts, and case studies while also reviewing technical capabilities online via company websites, social media posts, and online reviews.
Who should be involved in the decision-making process? Does it vary depending on if this is a private or municipal purchase?
Engage all key stakeholders. This could include the building owner, facility manager, engineer, operator, and service technicians. These individuals influence the final purchase to ensure long term performance and minimal cost of ownership. Be it a private or municipal purchase, all influencers should be consulted in the process. While the weighting of each input may vary, the immediate need and long-term performance will be taken into consideration.
At a minimum, the engineer, whether contracted or in-house, along with the service technician(s) should work together in the analysis and selection process. While an engineer determines lift station design and compliant pumps for a respective application, the service technician provides the knowledge required for future maintenance and repairs. Combining these subject matter expert’s opinions during the decision-making process will greatly improve the longevity of a system.
When is the best time in the life-cycle of an old pump to start shopping for its replacement?
A spare pump should always be on hand for emergency repairs. Typically, the search for a replacement should start once the spare has been installed. In cases where it is not feasible to have an inventory of spare pumps, it is important to implement preventative or predictive maintenance strategies to minimize unexpected down time and prevent unexpected costs due to emergency repairs or replacements. It is recommended to monitor performance such as:
- Preventative maintenance—implement a program to regularly inspect and service pump systems. Document the findings to provide better insight to parts or replacement purchasing strategies.
- Monitoring the system for frequent high-water alarm occurrences. This could signal a pump is unable to keep up with demand due to the possibility of an undersized pump or damage to an impeller.
- Also monitor a pattern of frequent clogging. In these cases, an upgrade to a shredder or chopper pump is in order.
- Pump performance monitoring—this could include monitoring seal chambers to determine if water has entered an oil filled mechanical seal chamber.
After the submersible is installed and running, when is the best time to assess the purchase and what performance factors should the pump user consider?
This process should start immediately after choosing a partner to work with, be it the manufacturer, distributor, or system installer. It is important to confirm the following:
- Proper equipment specified.
- On-time delivery of equipment and documentation.
- Necessary documentation such as instruction manuals, drawings and recommend spare parts listings were provided.
- Installer’s technical expertise regarding proper installation and performance validation.
- Availability of on-site support.
After installation, the assessment approach is an ongoing process. Key considerations include:
- A comprehensive start-up procedure, along with a follow-up report.
- Product meets the technical characteristics represented by electrical and hydraulic performance checks.
- Performance matches engineering specifications and manufacturer’s supplied documentation.
- Service contract options.
- Availability of customer and technical support from the manufacturer/distribution.
Given the impact submersible pumps have on a facility, be sure to continually assess the performance of the product, the manufacturer, and the distributor.
FOR MORE INFORMATION
The Submersible Wastewater Pump Association (SWPA) is a national trade association representing and serving the manufacturers of submersible pumps for municipal and industrial wastewater applications. Founded in 1976, the association’s primary focus is on industry guidelines, education, and promotion. SWPA’s Summer Meeting and Plant Tour is scheduled for August 2020. For more information, visit www.swpa.org.
MODERN PUMPING TODAY, June 2020
Did you enjoy this article?
Subscribe to the FREE Digital Edition of Modern Pumping Today Magazine!
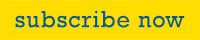