Safe, clean, accessible drinking water is one of our most basic human needs in the communities where we live and around the world. The wastewater treatment industry plays a significant role in this process, tasked with returning water back to lakes, rivers, and streams, having removed pollutants, broken down organic matter, and restored the oxygen content to the treated water. Municipal water treatment plants rely on pump and motor systems to move water efficiently and effectively through the treatment process. These systems typically handle wastewater flow in one of two ways.
Dry pit pumping uses a centrifugal pump and motor system that is not submerged in water. The system is housed in a pump room, which is attached or located adjacent to a wastewater sump. From there, the pump pulls water and other waste materials from the wet pit. Since dry pit systems are not submerged into the wastewater, they are easier to access, maintain, and repair; however, since they are typically below ground level, they are highly susceptible to flooding.
Wet pit pumping uses a pump and motor system that can be partially or fully submerged directly in the wet well. Wet pit systems have a smaller footprint than dry pit systems and are less costly. They also eliminate the requirement for aboveground construction to house a control center. In addition to operating in a wet pit environment, a submersible motor solution allows the pumping application to operate in areas that are prone to day-to-day (even hour-to-hour) intermittent flooding. Not every motor can function while fully submerged. To do so requires special features to ensure performance in both wet and dry pit applications.
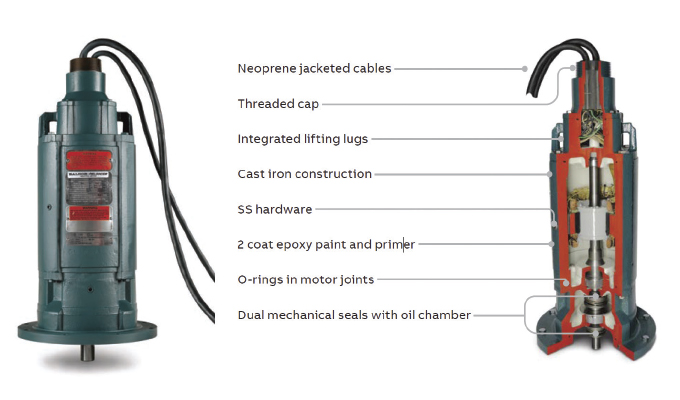
HARSH CONDITIONS
A basic electrical safety rule is that water and electricity do not mix; however, submersible alternating current (AC) induction motors must function in or under water to operate pumps, mixers, and aerators in industrial water and wastewater applications. Submersible motors must be specially designed and manufactured to prevent water from contacting any part of the electrical circuit while providing long life in these harsh applications.
Operating locations of these motors are extremely demanding, and repairs and maintenance can be difficult and time consuming. Applications in areas such as slurry pits with gritty, sandy effluent, storm water drainage systems, and—most commonly, clean water and wastewater treatment facilities—demand motors that are designed and built with seals and protective monitoring components to withstand the harshest submerged conditions.
DESIGN AND CONSTRUCTION
A submersible motor is completely enclosed and non-ventilated. It does not have an external shaft-mounted fan to cool and dissipate the heat from the frame. In wet pit applications, the motor relies on the liquid in which it is submerged to dissipate the heat from the frame. Its duty cycle must be continuous in water but must also be able to withstand extended periods of in-air operation—at least fifteen minutes in most cases. Because the air does not dissipate heat as well as liquids, the frame usually must be oversized so that more surface area is available to move the heat away from the motor.
The potential for the presence of flammable gases or liquids and combustible dusts can also affect the design of motors that operate in water and wastewater applications. Methane gas is formed by decomposing solids. It is potentially explosive and could require a motor to carry a Division 1, Class I, Group D certification. Users are responsible for specifying the hazardous area certification requirements of the motor. They can reference NFPA 70, National Electrical Code1, which defines the hazard rating of the space or envelope, or NFPA 820, the Standard for Fire Protection in Wastewater Treatment and Collection Facilities2, which defines the hazard and classification for the process areas.
Some may question why the motor must be certified for operation in the gas above the liquid if it is submerged. The reason is associated with the fifteen-minute, in-air duty cycle capability. Because the motor could operate in air in an abnormal situation, it must carry the appropriate certifications for the hazardous environment.
Heavy-duty cast iron frames should be used when constructing submersible motors. Cast iron provides good protection in an industrial environment because it does not dent, deflect, or bend easily, all of which could cause failure of the sealed enclosure. The frames are precision machined for tight fits between parts. All machined fits have grooves and O-rings to prevent water from entering the motor.
Submersible motors should be designed with a volute, direct-to-pump, mounting configuration, meaning the pumped fluid lubricates the outer seal. The benefit of this configuration is that it makes installation quicker and easier by removing the need for couplings, mounting tables, or safeguards for open shaft-to-shaft coupled connections. By removing the need for these extra components, customers have a simplified, compact motor and pump package while reducing any unnecessary potential failure points. In this case, less is better.
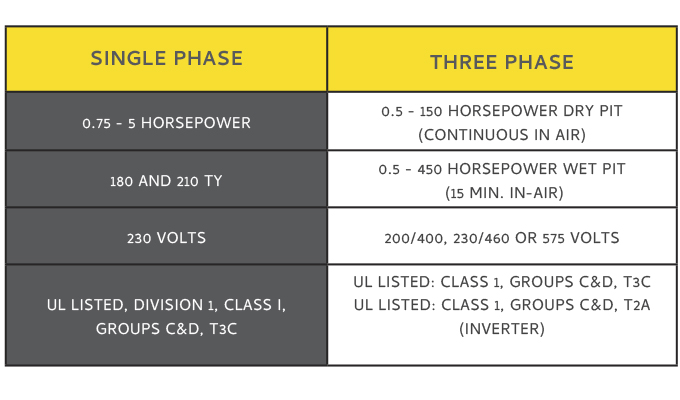
SEALS, CABLE ENTRIES, AND CABLE CAP ASSEMBLIES
However, as far as protection goes, more is better. To further protect against moisture ingress on the drive end of the motor, seal options should be are available to meet the needs of varied applications. All seal arrangements should utilize an oil chamber with moisture probes for early moisture ingress detection.
A type 21 mechanical shaft seal is often used on submersible motors. This all-purpose seal rotates with the shaft against a stationary mating face and eliminates adhesives by using mechanically crimped components. To securely seal the output shaft and protect the motor, submersible motors have an inner and outer seal arrangement on the drive-end plate.
Typical type 21 seal materials include:
- Carbon ceramic-faced seals, which are general purpose, stainless steel seals typically used in food processing, petrochemical and wastewater applications with relatively clean effluent.
- Tungsten carbide-faced seals, which provide harder seal faces for more demanding applications in more viscous fluids.
- Silicon carbide-faced seals, which are typically used for the most demanding slurry type (highly viscous fluid) applications.
Commonly called cable cap assemblies (CCA), these components are designed for easy installation in the field. A built-in alignment notch makes field installation quick and easy and reduces the chance for incorrection installation. Certain CCAs use a field-proven, potted-style cable cap with internal non-wicking lead connectors. Should the outer sheath of the power cable become damaged, and moisture were to wick down through the cable, both styles of CCA are constructed in a way that moisture cannot enter the motor, providing further protection from unwanted moisture ingress.
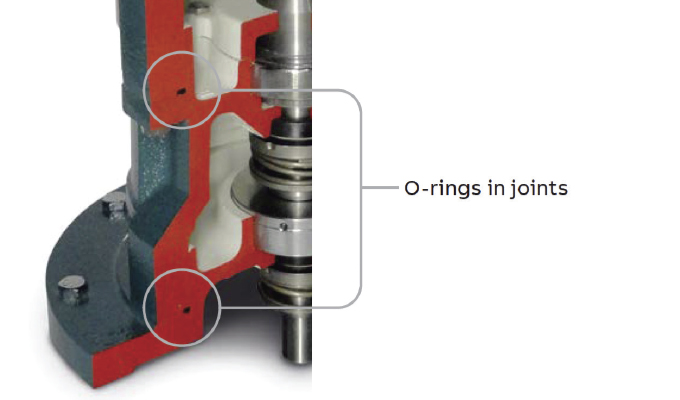
MONITORING
No matter the material of construction, seals are wear devices—or consumables. Surface abrasion on the outer seal could lead to seal failure, allowing fluid to enter the motor. In this situation, oil chamber and moisture probes provide a key safety feature for long motor life. The probes are set to the resistivity of the oil that fills the chamber. If the outer seal fails and water mixes with the oil, the moisture probes detect the moisture influx and send a signal, via a control module, to a control panel warning alarm. This gives the user time to shut down the pump, change the outer seal and restart the motor.
Submersible motors are not like other induction motors. They are specifically designed to safely operate in and under water. Their rugged construction, secure sealing and protective safety monitoring provide long life and safe operation with pump equipment.
FOR MORE INFORMATION
Bob Perdue is product manager for specialty products in the ABB NEMA Motors Division. ABB is a leading global technology company that energizes the transformation of society and industry to achieve a more productive, sustainable future. By connecting software to its electrification, robotics, automation, and motion portfolio, ABB pushes the boundaries of technology to drive performance to new levels. With a history of excellence stretching back more than 130 years, ABB’s success is driven by about 105,000 talented employees in over 100 countries. For more information, visit www.new.abb.com/motors-generators.
MODERN PUMPING TODAY, January 2024
Did you enjoy this article?
Subscribe to the FREE Digital Edition of Modern Pumping Today Magazine!