In Pali, Rajasthan, India over two hundred factories in the surrounding Punayata Industrial Area provide the economic backbone for the community. Unfortunately, the nearby Bandi River is polluted due to the discharge of industrial effluents and sewage disposal. This polluted water flowing in the Bandi is a constant threat to the health of villagers and to agriculture. The challenge, however, was that current common effluent treatment plants (CETPs) were not achieving zero liquid discharge (ZLD) and effluents were still being discharged into the river.
PROJECT UP CLOSE | |
LOCATION | Pali, Rajasthan, India |
PROJECT | PALI CETP (Textile) |
CUSTOMER | Aldee Water Pvt. Ltd. |
FACILITY CAPACITY | 3.17 million gallons per day |
ESTIMATED ENERGY SAVINGS | 13,234 kWh/day |
ESTIMATED COST SAVINGS | $483,000 per year |
PAYBACK PERIOD | 12 – 18 months |
THE SOLUTION
All the equipment in the Pali Common Effluent Treatment Plant is supplied by Aldee Water Pvt. Ltd. Advanced reverse osmosis water treatment was adopted to significantly reduce the stream volume being sent to the thermal system, reducing both CAPEX and OPEX of the thermal system. With added nanofiltration processes in place to separate salt, the high purity salt could then be recycled and sold.
To achieve more efficiency and cost savings, Detox Group and Pali CETP partnered with Energy Recovery, Inc. to install a suite of energy recovery devices, including both turbochargers and pressure exchangers, bringing higher uptime and availability to the whole system.
The plant now utilizes the following Energy Recovery products: AT Turbocharger, PX Q300s, PX Q220s, AquaBold high-pressure pump, and HP and VPXP circulation pumps.
The goal was to achieve high recover y rates in the membrane trains to minimize the brine flow into an evaporator to meet minimal or zero liquid discharge regulations. This required multiple reverse osmosis systems in conjunction with nanofiltration.
THE RESULT
Energy Recovery engineers worked with the OEM and completed the entire commissioning process in one week.
- RO1 with four trains of AT-550 turbochargers
- RO2 with two trains of PX Q220 operating at an efficiency greater than 95 percent, AquaBold high-pressure multi-stage pumps, and additional booster pumps
- RO3 with one PX Q300 train operating at an efficiency greater than 95 percent, an AquaBold high-pressure multi-stage pump, and a booster pump
- The nanofiltration system with one PX Q220 operating at an efficiency greater than 95 percent
The system is expected to realize a total of 13,234 kWh in energy savings daily. The payback for the combined energy recovery equipment and pumping solution is projected to be twelve to eighteen months, even at a reduced feed of total dissolved solids (TDS). As the plant continues to increase TDS concentrations and system pressures, the efficiency of these ERDs is expected to increase, recovering even more energy and increasing savings for the plant.
By utilizing Energy Recovery’s various solutions in the system, the facility is achieving savings in operating expenses estimated at $483,000 per year. The facility was also able to reduce investment in the thermal system. Additionally, the treated freshwater has been sold back to 215 plants, creating significant revenue. Finally, the efforts prevented further pollution of the Bandi River, helping the environment by sending the undissolved solids into an evaporation pond.
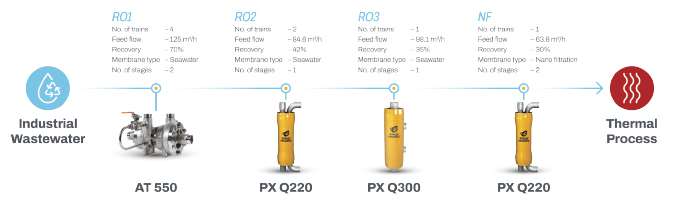
SOLUTIONS THAT ACCOMMODATE WIDE FLOW AND PRESSURE OPERATING RANGES
The textile waste stream parameters from 215 textile manufacturing businesses can pose a challenge, leading to wide flow and pressure operating ranges for the RO process. The challenge was met with a full complement of Energy Recovery products proven to perform in these demanding conditions, achieving maximum plant savings and energy efficiency. The PX devices with a suite of companion pumps provided operational flexibility and was the ideal solution for the Pali CETP plant.
FOR MORE INFORMATION
Energy Recovery creates technologies that solve complex challenges for industrial fluid-flow markets worldwide. Building on our pressure exchanger technology platform, we design and manufacture solutions that make industrial processes more efficient and sustainable. What began as a game-changing invention for desalination has grown into a global business accelerating the environmental sustainability of customers’ operations in multiple industries. Headquartered in the San Francisco Bay Area, we are a global team with sales and on-site technical support available worldwide. For more information, visit www.energyrecovery.com.
MODERN PUMPING TODAY, November 2023
Did you enjoy this article?
Subscribe to the FREE Digital Edition of Modern Pumping Today Magazine!