A newly-designed wastewater treatment plant is using an age-old source in a unique application for wastewater treatment. The plant in Sanford, Florida, and several other installations throughout the United States, is using a “solar drying” process to reduce sludge disposal costs and support the environment. The process, which is increasingly used by operators of medium-sized and large wastewater treatment plants, includes solar dryers manufactured by Huber. The process extracts water from sewage sludge and significantly increases the percentage of solids.
“We had a very basic dewatering system where we were getting about 16 percent solids,’’ says Anne Nelson, the lead plant operator at the Sanford plant. “With the Huber system we get about 75 percent solids, and it’s very dry. The 16 percent that we got from the other system was not as dry, kind of like a gelatin mold. The solids from the Huber system are not quite soil, but it’s very dry, it reduces the number of trucks we have to send out and is more easily used.”
The Florida facility has a treatment capacity of 8.5 million gallons per day. It is similar in construction to a plant in Egypt that has been officially awarded by Guinness World Records as the largest water treatment plant in the world and the largest sludge treatment plant in the world with a capacity of 1.4 billion gallons per day.
While using energy from the sun is not a revolutionary idea, the large-scale capacity is a recent technique that is gaining appeal in the wastewater treatment industry.
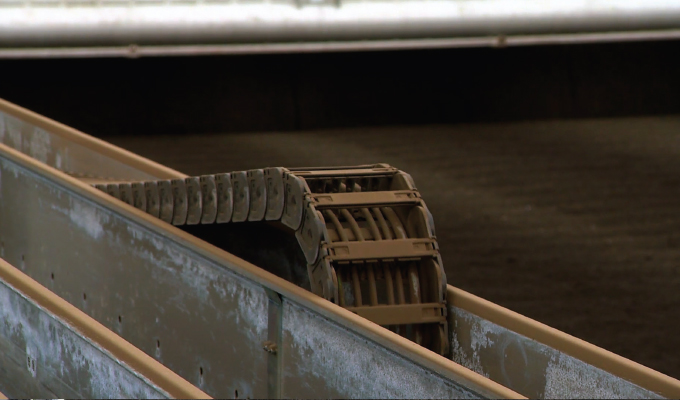
THE GREENHOUSE EFFECT
The Huber Sludge Turner Solstice® units work in greenhouses. The turner travels on rails and repeatedly rearranges the sludge on the ground. During the movement, the sludge is dried by solar energy. At the end of the drying lane, the sludge turner picks up the dry granules in the tool that repositions the sludge during its forward movement. The dry material is relocated to a recess in the ground, then collected and transported to a container.
There are several benefits. Disposal costs are significantly reduced when sludge volume is reduced through drying. Depending on the size of the plant, costs in dealing with sludge can range anywhere from 40 to 60 percent of total plant costs.
Also, costs keep rising. A report in 2019 found a 5.2 percent rise in the cost of tipping fees, which is the charge levied upon a given quantity of waste received at a waste processing facility. Sludge is accepted at some municipal landfills, but many of them have reached capacity and are closing. More strict disposal regulations and escalating fuel and hauling costs can be curbed by solar drying.
The other significant benefit to solar drying is helping the environment by using solar energy. Solar drying provides the lowest energy demand of any type of sludge dryer. Fewer trucks transporting sludge also reduces carbon emissions.
The facility in Sanford includes a 410-foot-long drying field, which is 39 feet wide. The greenhouse is slightly larger, to accommodate loading, unloading, and maintenance areas. The dryer can accept 4,790 wet tons per year.
The system takes a solid mixture that is 78 percent moisture and water and 22 percent dry solids and converts it to 75 percent dry solids. Evaporation reduces the amount of wet tons that need to be hauled offsite to 1,405 tons per year.
The plant in Egypt along the Bahr El-Baqar drainage canal is similar to the Florida plant, but with much larger capacity. The canal is considered as one of the most polluted tributaries in the world. Industrial waste and sewage from Cairo and agricultural runoff, pesticides and fertilizers end up flowing into the drain. Water quality index scores range between 37 and 48, on the edge between poor and marginal.
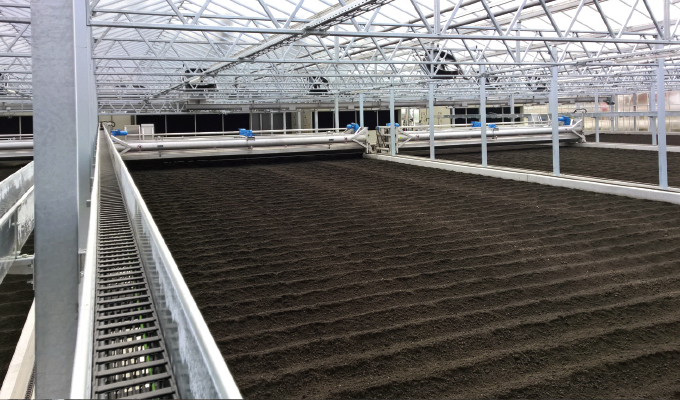
POWERED BY ENERGY CHAINS
An important component to the Huber Sludge Turner Solstice units are energy chains manufactured by igus®. The company, based in Germany, runs its North American operations out of Providence, Rhode Island. The energy chains include the company’s chainflex® cables, which provide reliable data transfer and energy supply for the sludge turners. The energy chains in the application in Egypt travel approximately 100 meters, while the Sanford system e-chain is nearly 140 yards, about 1.5 football fields.
“Energy chains are the best solution for cable guidance on long travels,’’ says André Großer, Huber SE product manager. “It requires little room, protects the cable, and is easy to install and maintain.”
The chainflex cables are also critical to the sludge turner. Three individual cores and a CFPE cable, all with a TPE outer jacket, ensure connection to the cable. Data exchange is with an igus CFBUS cable with a PUR outer jacket and those cables are designed specifically for use in energy chains. They also include an abrasion-resistant outer jacket and special interior stranding.
SAVIOR IN SANFORD
The solution with Huber’s units helped Sanford solve a sticky situation. The city near Orlando had been using a company that was using a gasification process to turn biosolids into an ash by-products.
When the company unexpectedly closed, it forced Sanford to find a new system and to pay $10,000 per month to haul sewage biosolids offsite. The Huber system proved a more reliable and cost-effective operation.
“As a company that is working in the environment, we are always looking for solutions,’’ says Großer. “We not only want to make water clean, but we also want to reduce our reliance on electric energy. We are developing the process and we are on the right track. In any project, we are concerned about the environmental impact and look for the best practices to protect our environment.”
FOR MORE INFORMATION
Thomas Renner writes on building, construction, engineering, and other trade industry topics for publications throughout the United States and Canada. Huber Technology provides state-of-the-art equipment for municipal and industrial water and wastewater treatment. The company’s main focus is liquid/solid separation in general and headworks equipment in particular, offering a comprehensive line of stainless-steel equipment. For more informationn, visit www.huber-technology.com.
MODERN PUMPING TODAY, March 2022
Did you enjoy this article?
Subscribe to the FREE Digital Edition of Modern Pumping Today Magazine!
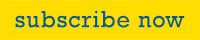