End users or service centers often need to specify replacement pumps or pump motors, sometimes involving a retrofit or re-application project. A successful outcome depends on accurate assessment of application requirements and a good understanding of the parameters that govern pump performance. The information here relates to rotodynamic pumps (centrifugal and axial flow impellers) and not to positive displacement pumps.
PUMP RATINGS AND POWER REQUIREMENTS
Unlike motors, pumps are rated by head and flow, not by power. There’s no such thing as a 50-horsepower pump or a 100-kW pump. A pump can operate over a range of heads and flows, and the power required is determined by those and by the pump’s efficiency at the particular head-flow operating point. It’s helpful to know that “head” correlates to a measure of pressure. For water, it’s a simple conversion: 2.31 feet head = 1 psi (1 meter head = 9.8 kPa). Here’s a simple formula that describes the relationship between head, flow, pump efficiency and pump power:
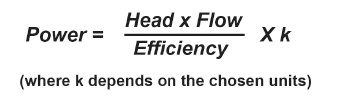
While this formula is helpful for quickly estimating the power required for a rotodynamic pumping application with known head and flow values, you can only get accurate power values from the manufacturer’s pump curve. How to read pump curves is beyond the scope of this article. What is important here is that the power requirements vary with flow rate, so knowing the range of flow rates for the pump is essential to sizing a motor to the pump.
Sizing the Pump
The process of sizing a pump and motor starts with sizing the pump for the application’s range of head and flow requirement. The following basic concepts are evident on the pump curve.
Flow Requirement
A pump may operate across a wide range of flow rates, known as the allowable operating range. Ideally, the pump should be designed to operate as close as possible to the best efficiency point (BEP) and within the preferred operating range. Pump efficiency will drop dramatically as flow rates move away from the BEP, and turbulent flow will reduce the reliability of the pump.
Head Requirement
The head that a pump can deliver must match the application. If the maximum pump head is below the system demand, the pump will not produce flow (bad!). If the maximum pump head is much greater than the system demand (more than double), the operating point will not be near the BEP, and both efficiency and pump reliability will suffer.
Cavitation
Another important concern when selecting a pump for a specific application is the possibility that cavitation may occur. If the pump is to operate across a range of flow rates (rather than always operating near a single flow rate), cavitation will be more likely at the higher flow rates. Pumps have net positive suction head required (NPSHR) ratings, which allow evaluation of the likelihood of cavitation at any flow rate using NPSHR values from the pump curve.
Generally, lower-speed pumps are less susceptible to cavitation than higher-speed pumps. If the application has low suction head demands, a lower operating speed will be an advantage. At lower operating speeds, a larger pump impeller diameter will be required, and thus a physically larger and more expensive pump may be needed.
SIZING THE MOTOR
Once a pump of the proper size is selected for the application’s range of head and flow, the motor can be sized and selected to match the pump’s requirements.
Minimum Power Requirement
For most pumps, the power requirement varies with flow rates. Power requirements may increase or decrease with increased flow. The pump curve will provide that information. Obviously, the motor must have adequate power to meet the pump demand at the application flow rate with the highest power requirement. That’s the minimum power requirement for the motor. But it is likely the pump will have an allowable operating range wider than the application demands.
Maximum Power Requirement
If application demands were to change at some future time, the pump might be expected to operate at a point where the power requirements are greater than the minimum power requirement. Therefore, it’s wise to consider the maximum power the pump could require under any operating conditions. This value is provided on the pump curve as the no overload power (NOL) rating. In some cases, the difference between the minimum power requirement for the application and the NOL rating may be absorbed by the motor service factor. In other instances, sizing for NOL power may require a higher power motor.
CONCLUSION
Sizing a pump and a pump motor for an application is not a trivial endeavor. The application head and flow requirements must be known. The pump power formula provided above, with the “k” to match the selected units, will provide a good estimate of the size of the machine. Pump vendors have pump selection charts which are generalized versions of the pump curve that will help with pump selections. Those charts and related reference data will provide NOL power ratings. The person responsible for selecting a pump and motor should have the appropriate pump curves and motor data and know how to read them.
By Eugene Vogel, EASA
FOR MORE INFORMATION
Eugene Vogel is a pump and vibration specialist at EASA, Inc., the Electrical Apparatus Service Association. EASA is an international trade association of more than 1,800 firms in nearly seventy countries that sell and service electromechanical apparatus. For more information, call 314.993.2220, fax 314.993.1269, or visit www.easa.com.
MODERN PUMPING TODAY, January 2022
Did you enjoy this article?
Subscribe to the FREE Digital Edition of Modern Pumping Today Magazine!
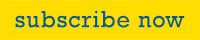