By Donald Schroeder, Power Lube Industrial
Automatic lubricators are devices that can be programmed to deliver lubricant (grease or oil) on a timed basis. In most cases, the equipment can continue running during lubrication, reducing downtime.
As a concept, automatic lubrication isn’t new. But the technology to deliver precise amounts of lubricant in a predictable and deliberate manner has evolved considerably over the years. Where first-generation lubricators relied on gravity and backpressure to regulate the lubrication process, today’s lubricators are sophisticated and come packed with microprocessors and other self-regulating componentry to ensure that just the right amount of lubricant is applied to the bearings at an optimal interval.
These lubricators can be direct-mounted to a single bearing, or remote-mounted for more convenient servicing of bearings in hard-to-reach or hazardous areas.
Several automatic lubricators on the market today are capable of generating output pressures in excess of 300 psi, making them suitable for lubricating multiple points—in essence serving as low-cost, centralized lube systems.
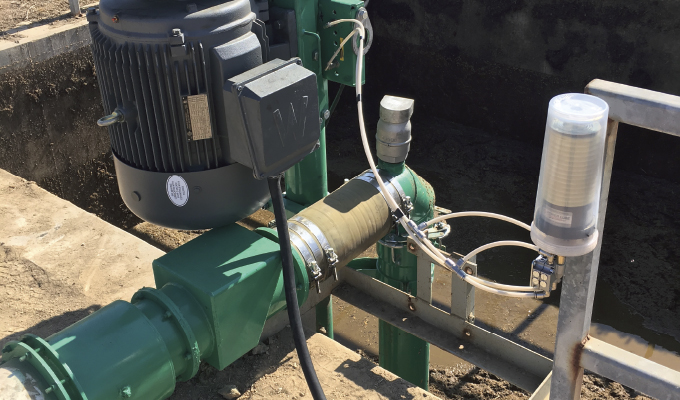
WHAT ARE THE SEVEN ADVANTAGES?
Automatic lubricators simplify equipment lubrication and bring a level of consistency that results in (among other benefits):
1. REDUCED EQUIPMENT DOWNTIME
Automatic lubricators can be remotely mounted in a convenient and safe location, away from the machinery’s service port or grease nipple. This virtually eliminates the need for time-consuming lock-out procedures because service panels, shrouds, and other machinery components don’t need to be removed in order to access hard-to-reach bearings. This means the machinery doesn’t need to be shut down to replenish the lubricant supply.
For many facilities, downtime is measured in hundreds or thousands of dollars per hour. By automating the lubrication process, these systems can quickly pay for themselves by significantly reducing downtime.
2. REDUCED EQUIPMENT MAINTENANCE COST
Optimal lubrication practices extend the life of the equipment. Also, lubrication technicians no longer need to log hours of time each week keeping a fresh supply of lubricant in equipment bearings. On average, it takes less than five minutes to service an automatic lubricator. Compare that to the fifteen minutes or more it takes to manually lubricate a bearing.
3. INCREASED LABOR FORCE EFFICIENCY
One of the biggest concerns we hear about automatic lubrication is this: maintenance managers are worried that it encourages complacency and makes it convenient for their maintenance staff to ignore the equipment. On the contrary, automating the lubrication process allows the technician to focus more of their attention on inspection of that equipment.
Furthermore, it frees them up to focus more time on higher-value tasks, significantly increasing your labor force efficiency. Automating the lubrication process is not an invitation to ignore the equipment. Rather, it promotes lubrication uniformity and facilitates better use of personnel time.
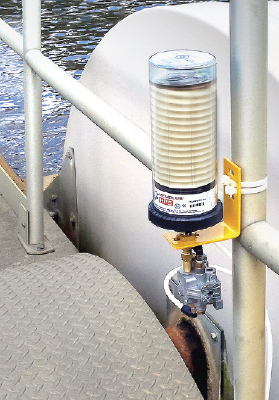
4. INCREASED SAFETY
Automatic lubricators eliminate the risks associated with manually lubricating hard-to-reach areas. These hazards include slipping, tripping and falling. For lubrication points in hard-to-reach areas, automatic lubricators can be mounted in a safe location, and a grease line can be run to those lube points.
5. PROLONGED EQUIPMENT LIFE
Uniform application of lubrication can significantly extend equipment life and reduce unplanned downtime and maintenance. Applying small amounts of lubricant over time reduces wear by consistently providing a film of fresh lubricant between friction surfaces. It also reduces the consumption of lubricants by only lubricating the bearings as needed and not as scheduled.
In addition, automatic lubrication minimizes waste, which is good for the environment. It also keeps lubricant off of the production floor and the machinery, which can improve safety.
6. LUBRICATION CONSISTENCY
Automatic lubricators provide the same amount of lubricant, at a specified interval and to the specified place on a consistent basis. There is no variation in how the lubricant is applied.
With manual lubrication, two different lubrication technicians may be using two different techniques to lubricate the same point, resulting in two different outcomes. Even a single technician doesn’t lubricate the same point exactly the same way each time. His or her routine may be affected by time constraints, workload or other circumstances.
7. LUBRICATION RELIABILITY
Automatic lubricators are working twenty-four hours a day, seven days a week—even when you’re not. You will no longer need to wonder if or when critical bearings were lubricated. Plus, you can eliminate the finger-pointing that inevitably happens after a bearing failure that was caused by improper lubrication.
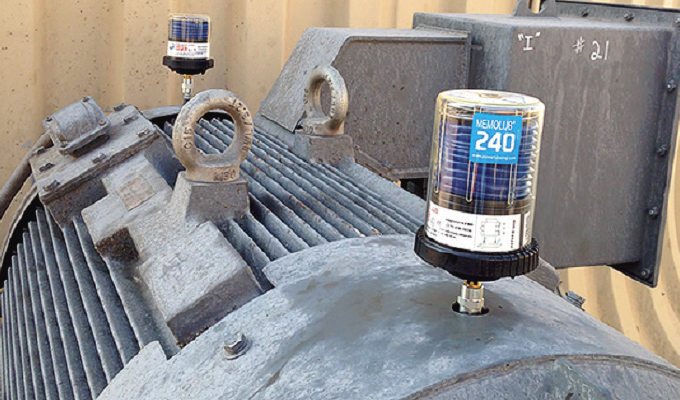
FOR MORE INFORMATION
Donald Schroeder is vice-president of operations at Power Lube Industrial, LLC. Power Lube Industrial, formerly known as PLI, LLC, is a company with almost fifty years of experience in the self-contained automatic lubricator field. To learn why manual lubrication is putting equipment bearings in danger and how single-point automatic lubrication can help maximize equipment uptime and minimize maintenance costs, visit www.powerlubeind.com/manual-vs-automatic-lubrication-eguide.
MODERN PUMPING TODAY, February 2020
Did you enjoy this article?
Subscribe to the FREE Digital Edition of Modern Pumping Today Magazine!
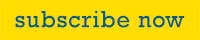