By Colin Guppy, Sundyne LLC
As we mentioned in last month’s installment of this series, standards play a key role in the chemical industry. The characteristics they define assure customers that performance and safety requirements are met, while also guaranteeing interoperability for equipment throughout a plant.
STRICT ADHERENCE TO INDUSTRY STANDARDS
The ANSI/ASME B73.3 standard specifically addresses centrifugal pumps for the chemical industry. The standard covers 27 pump sizes and specifies dimensions for height, length, nozzle, and shaft diameters, plus the location and spacing of mounting bolts. The ISO 5199/2858 standards cover the same type of industrial pumps as ANSI B73.3.
The pumps deployed for chemical processing applications should meet all relevant ISO, ASME/ANSI standards. They should be available in metallic options to withstand extremely high temperatures (such as stainless steel with silicon carbide internal bearings, or Alloy 20/Alloy C with PTFE gaskets). Pumps should also be available in non-metallic configurations, for highly corrosive applications.
ADDITIONAL PROTECTION AND PEACE-OF-MIND FOR HANDLING HARSH AND HAZARDOUS CHEMICALS
Seal-less pumps offer the best solution to fugitive emission regulation. But every pump can use help defending against unstable process conditions. Sensors and monitors alert operators to potential problems and secondary containment systems ensure that problems do not escalate.
“Gas-in-liquid” Detectors
To avoid the risk of damage and dry running, ultrasonic signal technology is available to instantaneously detect the presence of gas in a liquid stream from outside the confines of the pump pressure boundary.
Traditional temperature and power control monitoring solutions sense the secondary effects of a gas build-up in the pump—but in most cases, pump damage occurs before any change is registered. By using ultrasonic technology, the build-up of bubbles in liquid can be identified early, and operators can be warned if a pump suffers from incorrect priming or venting, entrained process gas, or incipient vaporization.
This ultrasonic technology—called VapourView—is adaptable to any application and can be retrofitted onto any seal-less magnetic drive pump. The system eliminates the potential for dry running and brings peace-of-mind against catastrophic failures and unexpected repair costs.
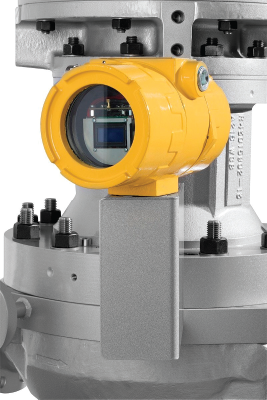
Eliminating Induction Heating and Eddy Current Losses
Applications that span the full hydrocarbon chain can pose challenges to pump seals by creating magnetic losses and by heating the process fluid. Pumps used in chemical processing applications can overcome these challenges with containment shells that eliminate induction heating and eddy current losses.
Most magnetic drive pump containment shells are made of metal. A preferred option for chemical processing applications are shells called ZeroLoss—which are engineered from a combination of poly-ether-ether-ketone (PEEK) and carbon fiber that was initially developed for military and aerospace equipment. Five times lighter than steel but just as strong, ZeroLoss Shells increase the pump’s reliability, widen temperature ranges from -40 to 305 degrees Fahrenheit (-40 to 150 degrees Celsius), bolster the pump’s resistance to thermal shock, eliminate potential vaporization of process chemicals near the pump’s bearing, and provide greater efficiency—by enabling a smaller motor to be specified (which also saves on power costs).
CHEMICAL PROCESSING PLANTS NEED ACCESS TO LOCAL AFTERMARKET SERVICE
Chemical plants run operations around the clock. If any part of the operation fails, it must be brought back on line immediately. A pump manufacturer’s Authorized Service Centers (ASCs) must be able to support every pump, and bring engineering expertise and technical support to the customers’ job site at a moment’s notice. From routine maintenance programs and onsite troubleshooting to replacement parts and components, the service network must be able to provide everything it takes to keep chemical plants up-and-running—anywhere around the globe.
MAKING THE CASE FOR SEAL-LESS PUMPS IN CHEMICAL PROCESSING APPLICATIONS
When it comes to handling harsh and hazardous chemicals, safety for plant personnel and the environment are critical factors—but bottom-line ROI is just as important. In summary, here are ten reasons for operators to choose seal-less magnetic drive pumps for chemical processing applications:
- Design Simplicity: seal-less pumps = no leaks and no emissions
- Lower Installation Costs: no need for seal support systems
- Extensive Flow and Pressure Envelope: supported via a wide range of pumps
- Support for all Industry Standards: in any geography
- Construction Materials to handle any job:
- Metallic liquid ends for high temperature applications
- Plastic liquid ends for highly corrosive substances
- Monitoring Solutions: to identify potential problems before they escalate
- Secondary Containment Options: to deliver peace-of-mind
- Flexibility: to handle solids and withstand dry running
- Extended MTBF: to decrease maintenance costs
- Global Service and Support: to deliver same day local support, anywhere in the world.
MEETING OR EXCEEDING CHEMICAL INDUSTRY STANDARDS
- Metallic Options: HMD pioneered the seal-less magnetic drive pump for the chemical industry in 1947—and since that time, HMD’s engineers have leveraged more than seventy years of experience to ensure that HMD Kontro seal-less pumps adhere to, and exceed the latest ASME and ISO standards.
- Non-Metallic Options: For highly corrosive chemical applications, ANSIMAG pumps are ASME / ANSI B73.3 compliant and are available in materials that can stand up to most abrasive or highly-corrosive applications.
FOR MORE INFORMATION
Colin Guppy is Sundyne’s chief commercial officer. He is responsible for developing strategies and tactics for Sundyne’s chemical industry sector. He can be reached at colin.guppy@sundyne.com. Sundyne has assembled industry-leading brands that provide customers with a wide range of fluid and gas handling services and solutions. Brands like Ansimag, HMD Kontro, and Marelli have broadened the original Sundyne portfolio for a wider range of markets. Sundyne equipment can be built to most standards, including ANSI, ISO, and API. For more information, visit www.sundyne.com or www.hmdkontro.com.
MODERN PUMPING TODAY, November 2020
Did you enjoy this article?
Subscribe to the FREE Digital Edition of Modern Pumping Today Magazine!
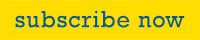