By Nancy Westcott, GoatThroat Pumps
As major segments of the economy attempt to formulate and implement effective re-opening strategies that meet state guidelines, many are forced to make critical decisions regarding mandating masks, enforcing social distancing, and improving cleaning and disinfecting procedures.
Although individual strategies for hotels, gyms, restaurants, bars, retailers, casinos, entertainment venues, and corporate offices may differ, re-opening guidelines usually have common, overlapping elements. Temperature checks for patrons and/or employees and better air filtration are good examples. But at the heart of seemingly every list is a dramatic increase in the frequency and thoroughness in cleaning common area surfaces, along with providing a readily available supply of hand sanitizer for employees and patrons.
Given the accelerated cleaning efforts, many businesses are opting to procure disinfectants and hand sanitizer in bulk. However, distributing such products from 275-gallon totes, barrels, drums and even single gallon sized bottles requires transferring or “down packing” to smaller containers or dispensers.
It also means that workers responsible for transferring such products—most of which are identified as potentially flammable or combustible substances—must do so at a dramatically higher rate and frequency. This could lead to a corresponding spike in the number of spills, worker injuries, catastrophic fires, and even explosions that occur.
So, to safely handle the spike in demand and facilitate down packing, businesses have been increasingly installing properly engineered refill stations using groundable, sealed pump systems that will allow employees to reliably and safely transfer from bulk containers to smaller containers.
EPA EASES RESTRICTIONS ON DISINFECTANTS
Coronaviruses like COVID-19 are enveloped viruses (a virus with an outer wrapping or envelope). They are one of the easiest types of viruses to kill with the appropriate disinfectant product. So, in the early stages of the pandemic, the U.S. Environmental Protection Agency (EPA) acted quickly to release a list of disinfectants that could be utilized to combat SARS-CoV-2 (see EPA’s List N: Disinfectants for Use Against SARS-CoV-2).
Shortly thereafter, the EPA made announcements that included temporarily allowing manufacturers of the List N disinfectants to obtain certain active ingredients from any source of suppliers without checking with the agency first. In addition, the EPA loosened the restrictions on refilling small containers from larger bulk containers.
However, the problem is that traditional practices of transferring liquid chemicals, including sanitizers and disinfectants on the EPA List N, suffer from a number of drawbacks. To start, common manual techniques, such as the tip-and-pour method, can cause spills and injuries to employees. Tipping heavy barrels or drums can lead to overpouring, but also toppling, so the probability of a spill is high.
This brings us briefly to the subject of personal protection equipment (PPE). Users need to review the safety data sheets (SDS) for correct and safe handling of their fluids and chemicals as well as PPE requirements at the points of use. In this way, worker protection is significantly enhanced.
The bar for safe transfer is even higher for many alcohol-based sanitizers and chemical-based disinfectants, which can pose issues of flammability or combustibility. In a flammable liquids fire, it is the vapors from the liquid that ignite, not the liquid. Fires and explosions are caused when the perfect combination of fuel and oxygen come in contact with heat or an ignition source. Based on their flash points, that being the lowest temperature at which liquids can form an ignitable mixture in air, flammable liquids are classified as either combustible or flammable.
Both combustible and flammable liquids can easily be ignited by a flame, hot surface, static electricity, or a spark generated by electricity or mechanical work. Consequently, minimizing the dangers of handling flammable and combustible liquid chemicals, including some sanitizers and disinfectants, requires proper training and equipment.
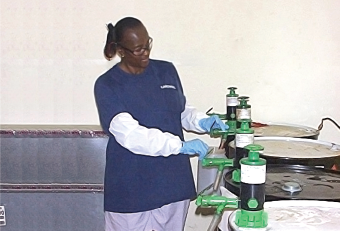
SAFE HANDLING
Without proper ventilation, the handling of flammable substances has a good chance to create an explosive atmosphere. Therefore, it is essential to work only in well ventilated areas or have a local ventilation system that can sufficiently remove any flammable vapors to prevent an explosion risk.
Because two of the three primary elements for a fire or explosion usually exist in the atmosphere inside a vessel containing a flammable liquid (fuel and an oxidant, usually oxygen), it is also critical to eliminate external ignition sources when handling such liquids. Sources of ignition can include static discharge, open flames, frictional heat, radiant heat, lightning, smoking, cutting, welding, and electrical/mechanical sparks.
STATIC ELECTRICITY GROUNDING
When transferring flammable liquids from a large container (greater than a gallon) to a smaller container, the flow of the liquid can create static electricity, which can result in a spark. Static electricity build-up is possible whether using a pump or simply pouring the liquid. If the bulk container and receiving vessel are both metal, it is important to bond the two by firmly attaching a metal bonding strap or wire to both containers as well as to ground, which can help to safely direct the static charge to ground.
When transferring Class 1, 2, or 3 flammable liquids with a flashpoint below 100 degrees Fahrenheit (37.8 degrees Celsius), OSHA mandates that the containers must be grounded or bonded to prevent electrostatic discharge that could act as an ignition source. NFPA 30 Section 18.4.2.2 also requires a means to prevent static electricity during transfer/dispensing operations.
ENGINEERING CONTROLS
Beyond workers wearing proper PPE at a jobsite with proper ventilation, it is absolutely critical to use regulatory compliant, engineered controls to safely transfer potentially flammable and combustible liquids, including bulk sanitizer and disinfectant. Most states and municipalities across the United States have adopted NFPA® 30 Flammable and Combustible Liquids Code and OSHA 29 CFR 1910.106, which address the handling, storage, and use of flammable liquids. With NFPA 30, material is classified as a Class 1 liquid (flammable) and Class 2 and 3 (combustible).
The codes account for safeguards to eliminate spills and leakage of Class 1, 2, and 3 liquids in the workplace. This begins with requirements surrounding the integrity of the container, but also extends to the pumps used to safely dispense flammable and combustible liquids.
In most workplaces, supervisors and facility managers have recommended rotary and hand suction pumps to transfer flammable liquids for decades. However, they are increasingly turning to sealed pump systems designed for class 1 and 2 flammable liquids, which are a more effective engineering control tool for protecting employees and operations.
Conventional piston and rotary hand pumps have some inherent vulnerabilities. These pumps are open systems that require one of the bungs holes to be open to the outside atmosphere. The pumps dispense liquids from the containers using suction, so it requires that a bung be open to allow air to enter the containers to replace the liquid removed. Without this opening, either the container will collapse or the liquid will stop coming out.
For isopropyl alcohol based liquids, not only will such a system lead to the evaporation of the sanitizing material—the IPA—but the liquid will also absorb water from the air such that it will be more water than air in short order.
SEALED PUMP SOLUTIONS
As a solution, the industry has developed sealed pump dispensing systems that enhances safety by eliminating spills and enables spill-free, environmentally safe transfer that prevent vapors from escaping the container.
These systems are made of groundable plastic and come complete with bonding and grounding wires. The spring actuation tap handle can be immediately closed to stop liquid flowing, preventing any spills. The design of this sealed pump system also prevents liquid vapors from exiting the container when the pump is unused. These characteristics significantly reduce the chance of an ignition event. The combination of all these features ensure the pump meets both NFPA30-2015.18.4.4 standards and NFPA 77.
GoatThroat Pumps offers refill solutions for dispensing disinfection liquids and sanitizers. In March, GoatThroat fulfilled orders for nearly 1,000 systems from both manufacturers as well as large corporate entities interested in providing hand sanitizer for all employees at all locations.
In two weeks, GoatThroat received a tsunami of calls for an isopropyl alcohol specific pump, which is designed to handle flammable liquids. Companies that just needed to use hand sanitizers in smaller capacities, like filling little bottles from large barrels, would call to order pumps with spout reducers.
The other source of inquiries were breweries switching over to manufacturing hand sanitizer and many manufacturing facilities that use the pumps as refill stations for jugs and bags to dispense product at the point-of-use.
GoatThroat has one prison authority using its pumps with pneumatic adapters reporting that they were repackaging 6,000 gallons a day of hand sanitizer with only two systems for use by the entire state prison population.
A NEW NEED FOR THE NEW NORMAL
The whole subject of personal protection is now being expanded on a broader front. PPE now also applies to those pumps on drums of sanitizers.
With the need for hand sanitizers and disinfectants expected to continue to rise given its central role in most successful reopening strategies, properly engineered refill stations will play a key role in allowing for the safe transfer of disinfectants and hand sanitizer from bulk containers.
FOR MORE INFORMATION
GoatThroat Pumps are manufactured exclusively by Westcott Distribution Inc. in Connecticut and are sold worldwide. For more information, call 866.639.4628, email info@goatthroat.com, or visit www.goatthroat.com.
MODERN PUMPING TODAY, October 2020
Did you enjoy this article?
Subscribe to the FREE Digital Edition of Modern Pumping Today Magazine!
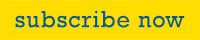