Around the world, private companies and government agencies are looking to reduce the greenhouse gas (GHG) emissions associated with their activities, including increasing their use of renewable and low-carbon energy sources and improving the energy efficiency of their processes.
Energy efficiency represents more than 40 percent of the emissions abatement needed by 2040, according to the International Energy Agency (IEA) Sustainable Development Scenario. The IEA says, “Energy efficiency is the ‘first fuel’: reining in the scale of this unprecedented challenge, supporting net zero energy goals at lower costs, and delivering a wide array of benefits for society.”
Furthermore, “According to the IEA Efficient World Scenario, currently existing cost-effective technologies are sufficient to double global energy efficiency by 2040.” Heat exchangers are just such an existing, cost-effective technology. Technologically proven for over a century, developments in materials and design mean that many types of heat exchanger, such as those utilizing corrugated tubes and energy recovery, are now more energy efficient than ever before.
SEEKING BIGGGER BENEFITS
The biggest efficiency benefits of heat exchangers come about when they facilitate the reuse of as much of the thermal energy generated or used during a process (such as heating, cooling, pasteurization, evaporation, etc.) as possible. Distributing heat more efficiently throughout production facilities has been recognized a key factor in improving efficiency and reducing greenhouse gas (GHG) emissions in industries including as chemical refining, water treatment and manufacturing.
Many processes require heat, but not all of them utilize all of it. For example, a process using steam at 212 degrees Fahrenheit (100 degrees Celsius) or more may result in a hot water stream with a temperature of 176 to 194 degrees Fahrenheit (80 to 90 degrees Celsius). In some cases, this will be reheated in a continuous cycle, but in the least efficient situations it may simply be dumped, perhaps requiring cooling before it can be discharged. Water with this temperature profile has a range of potential uses, including pasteurization and low temperature evaporation. Rather than continually heat and then dump process hot water, it makes far more sense to reuse it where possible, by transporting it to where else it is needed in the facility.
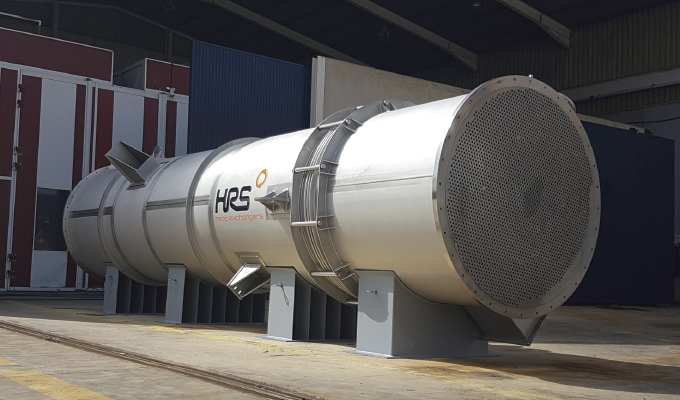
EXAMPLES OF HEAT RECOVERY WITH HEAT EXCHANGERS
The first typical example can be seen in food production, if we imagine a product that needs to be pasteurized. The product needs to be heated to the necessary temperature to achieve pasteurization, then rapidly cooled to maintain shelf life and quality. This is achieved through the use of two heat exchangers. The first uses hot water to raise the temperature, while the second uses chilled water to cool the product down again. In the second process, the temperature of the cooling water is increased significantly. There are three options for dealing with this heated water: discard or discharge it elsewhere; cool it again for re-use; or cool it again for re-use but use some of the heat it contains towards the heat required for the pasteurization phase. This third option utilizes heat recovery or heat regeneration, reducing the amount of new energy required for the subsequent first heating phases.
A second example shows how heat left over from one process can be recaptured to be used elsewhere. Many anaerobic digestion (AD) plants use heat exchangers to pasteurize the digestate produced during the AD process, so that it can be sold as an agricultural fertilizer. The “surplus” heat which is generated after the system has been running for two hours is used to preheat the digestate, reducing total heat load and improving overall plant efficiency by increasing the amount of generated energy, which is available for export or other uses, as opposed to being required for pasteurization.
Finally, combining multiple heat exchanges can often provide the greatest energy benefits, for example, in a multi-effect evaporation system such as the HRS DCS Digestate Concentration System. This uses heat exchangers and evaporation to reduce the volume and increase the concentration of sludges and digestate. The first evaporation stage heats liquid digestate and uses a cyclone separator; the steam produced from this first cycle—usually available at 158 degrees Fahrenheit (70 degrees Celsius)—is then used as the heating media for the second effect, whereby the process is repeated.
The subsequent steam—usually available at 140 degrees Fahrenheit (60 degrees Celsius)—is then used as the heating media for the third cycle. The number of effects is determined by the level of dry solids required and the amount of surplus heat available, up to a maximum of four cycles. After the final stage the steam is condensed back to water and this heat is used to pre-heat the incoming product before the first stage of evaporation.
THE FUTURE IS HEATING UP FOR RECOVERY
Heat recovery is not limited to systems dealing with liquids. HRS recently supplied a large G Series gas-to-gas heat exchanger to recapture heat from the high temperature exhaust gases leaving a large chemical reactor. This recovered heat is then used to help pre-heat the chemicals entering the reactor to around 932 degrees Fahrenheit (500 degrees Celsius). As well as helping to improve energy efficiency at the plant, the new unit has been designed to cope with challenging operating conditions in order to provide a suitable working life.
These examples show that where the situation allows, HRS corrugated heat exchangers have significant potential to reduce the energy consumption (and therefore GHG emissions) of thermal processes in a wide range of industries. The capital costs of including energy recovery in a heat exchanger system is likely to be higher than similar systems without heat recovery, but these will be recovered over the working life of the unit, particularly at today’s high energy prices.
FOR MORE INFORMATION
Matt Hale is the international sales and marketing director with HRS Heat Exchangers. Located in Atlanta, Georgia, HRS Heat Exchangers is part of the HRS Group, which operates at the forefront of thermal technology, offering innovative heat transfer solutions worldwide across a diverse range of industries. With forty years’ experience in the food and beverage sector, specializing in the design and manufacture of an extensive range of turnkey systems and components, incorporating corrugated tubular, and scraped surface heat exchanger technology, HRS units are compliant with global design and industry standards. For more information, visit www.hrs-heatexchangers.com.
MODERN PUMPING TODAY, August 2023
Did you enjoy this article?
Subscribe to the FREE Digital Edition of Modern Pumping Today Magazine!