By Matt Laufik, Electro Static Technology
Pumps and pumping systems account for 25 percent of the energy consumed by electric motors in the United States. In pumping intensive industries, this number is over 50 percent. In fact, providing clean drinking water to homes and businesses alone accounts for almost 12.5 percent of total U.S. pump energy consumption.
VFDS CAN SAVE 30 PERCENT OR MORE IN ENERGY COSTS
To improve the efficiency of pumping systems and reduce their electricity consumption, a growing number of pump users are turning to variable frequency drives (VFDs), also known as inverters or adjustable speed drives. Most pumping systems are designed for maximum service conditions, but running them at partial load can save a considerable amount of energy. By precisely matching electric motor speed to pumping requirements, VFDs can reduce energy costs by as much as 30 percent.
BUT VFDS CAN DAMAGE MOTOR BEARINGS
VFDs work by first rectifying 50/60 Hz AC power to DC, and then inverting the DC back to three phase AC at the desired frequency. But these drives’ output is not a smooth sine wave like line voltage. Rather, it is a series of pulses that approximates a sine wave. Because the voltage is pulsed, each phase’s voltage is either fully on or fully off. Switching between the on and off states is extremely rapid, so the voltage has a very short rise time.
These voltage pulses can cause problems in the motor. Firstly, the high peak voltages and fast rise times cause cumulative degradation of insulation and bearings, coil varnish, etc. This problem is made worse by the phenomenon of reflected waves in the VFD cable, which can lead to even higher voltages at the motor.
Most new motors are protected against winding damage with Class F or H insulation, so this is less of a problem now than it was twenty years ago. But VFDs can also cause electrical bearing damage.
Because each of the three phases of VFD output is always either on or off, the three phase voltages do not sum to zero (as three-phase line voltage does). The total voltage across the three phases, called the common mode voltage, couples to the motor rotor and capacitively induces a shaft voltage.
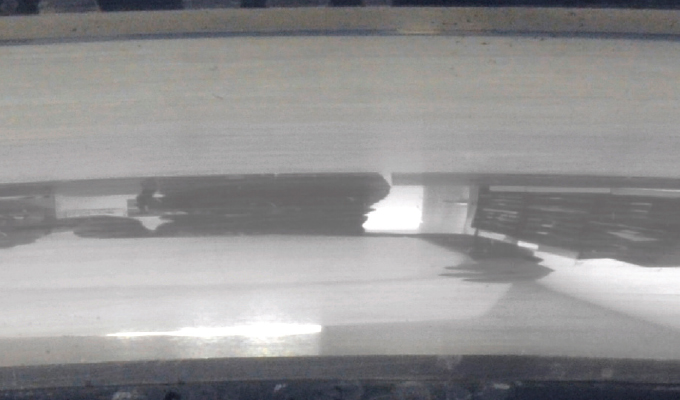
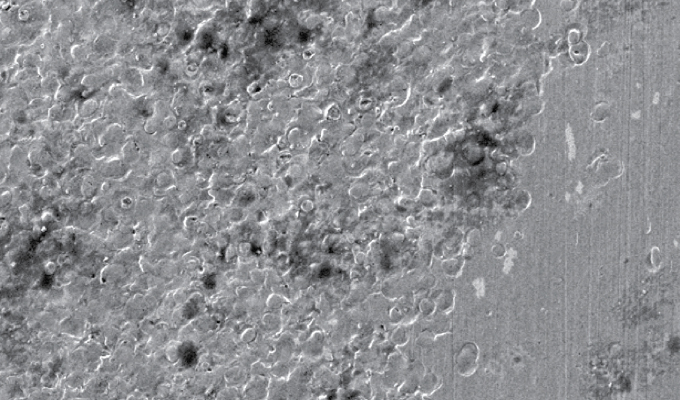
FOLLOW THE PATH OF LEAST RESISTANCE
This shaft voltage “wants” to discharge to ground. Usually, the lowest-resistance path from the shaft to ground is through the motor bearings, so shaft voltage tends to discharge by arcing through the bearings. This causes pitting (tiny craters in bearing surfaces), frosting (widespread pitting), fluting (washboard-like ridges in the bearing race), and eventual bearing failure. The rate of damage varies, but failure can occur in just a few months.
Electrical damage is believed to be the most common cause of bearing failure in VFD-controlled AC motors. Repair or replacement of failed motor bearings is a costly hassle. But these repair costs pale in comparison to the cost of unplanned downtime, which can easily wipe out any energy savings that VFDs offer.
To prevent unplanned downtime and the losses it entails, it is necessary to protect against electrical bearing damage.
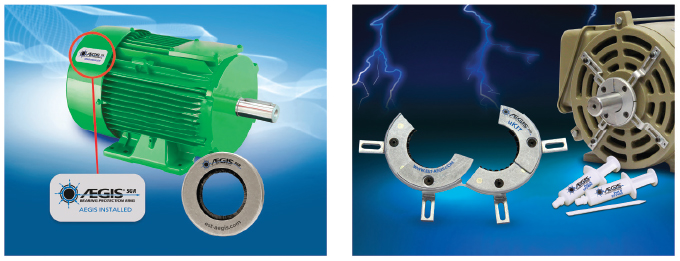
PROTECTING MOTOR BEARINGS FROM ELECTRICAL DAMAGE…
AEGIS® Shaft Grounding Rings provide a very low-resistance path from the motor shaft to ground. By offering a “path of least resistance,” a grounding ring channels charge on the shaft away from the bearings and safely to ground, ensuring the reliable, long-term operation of VFD-driven pumping systems. As proven in millions of installations worldwide, AEGIS rings provide unmatched bearing protection for the full L-10 life of the bearings.
AEGIS Shaft Grounding Rings are the only form of electrical bearing protection that comes with a two-year extended warranty against bearing failure from fluting damage.
AS WELL AS ATTACHED EQUIPMENT
One approach to electrical bearing protection is to use insulated motor bearings. But this does not remove the shaft voltage; the charge on the shaft simply seeks another path to ground—typically through a pump, gearbox, tachometer, encoder, etc., which consequently can end up with bearing damage of its own. By bleeding the voltage off the motor shaft, AEGIS rings protect attached equipment as well as the motor’s bearings.
When installed according to AEGIS Best Practices, AEGIS Shaft Grounding Rings protect pump motors and the pumps themselves from VFD-caused bearing damage and costly downtime. These Best Practices are detailed in the AEGIS Bearing Protection Handbook, available at est-aegis.com/pump.
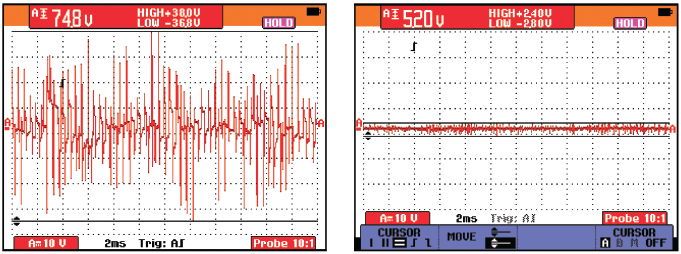
EASIEST WAY TO PROTECT A MOTOR
The easiest way to protect a motor against electrical bearing damage is to buy a new motor with an AEGIS ring factory installed. Several motor manufacturers now offer AEGIS Shaft Grounding Rings installed as standard or optional features on certain models. These include:
- ABB Baldor Super-E C-Face Motors with -G suffix (standard).
- NIDEC U.S. Motors CORRO-DUTY® Vertical HOLLOSHAFT® and World® Inverter Duty Motors (standard).
- WEG Electric Close Coupled Pump Motors (standard some lines).
- Regal Beloit Marathon XRI Motors (standard in several lines, including severe duty, IEEE-841, and explosion proof).
- TECO-Westinghouse TEFC Rolled Steel, ODP Rolled Steel and Cast Iron, and MAX-PE™ Motors.
FOR MORE INFORMATION
Matt Laufik is global sales manager for AEGIS, a leading brand in bearing protection. Electro Static Technology, the world leader in passive static control solutions, solves industry challenges posed by static charges in many of today’s sophisticated machines. For more information, visit www.est-aegis.com.
MODERN PUMPING TODAY, July 2020
Did you enjoy this article?
Subscribe to the FREE Digital Edition of Modern Pumping Today Magazine!
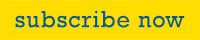