When seeking to protect industrial machinery from leaks and heat, two names within Emerson Industrial Automation’s family of brands are raising the standard for what operators can expect. Morse and Kop-Flex are fast becoming the “go to” names in machine protection.
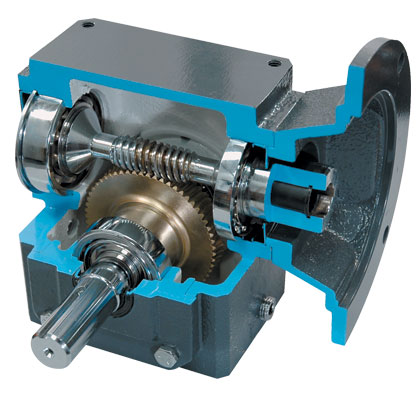
MORSE RAIDER PLUS
Morse Raider Plus speed reducers utilize advanced finishing techniques, additional bearings and special seals to arm them for leak-free performance, guaranteed for eighteen months. Ideal for conveyors, mixers and bucket elevators in the food, beverage and grain industries, the Raider Plus’ computerized gear centering optimizes the gear mesh for reduced heat and debris formation, eliminating unnecessary backlash and delivering high efficiency and long life.
A patented roll-burnished journal finish extends seal life up to four-fold, and exclusive double-lip seals on both input and output shafts provide leak-proof operation in highly contaminated applications. The Raider Plus also features an exclusive non-metallic quill liner that reduces fretting and corrosion, and eases motor removal. Large, single-row ball bearings absorb radial and thrust loads on higher input speeds, while heavy-duty tapered roller bearings on all output shafts handle inherent gear load and provide maximum overhung load capacity.
LEAK-FREE GUARANTEE
A key design component of this reducer is a second input bearing that reduces wear and fatigue on the input seal. The second input bearing minimizes shaft movement during motor installation and operation. We tracked the performance of the Raider Plus and are confident the materials and assembly of this product support an eighteen-month leak-free guarantee.
Four unit models—the “U”: a universal style with an output shaft, the “Q”: a c-face-style with an output shaft, and both styles with hollow outputs—are available from stock with a center distance range of 1 to 6 inches (25 to 152 millimeters), ratios from 4:1 to 3600:1 and output torques from 82 to 22,416 foot pounds.
All Raider Plus housings, motor adaptors, covers and mounting bases have cast iron single-piece construction for maximum strength and dependability. Forged bronze worm gears, precision manufactured to AGMA specifications, provide greater tensile strength than cast bronze. The integral worm and shaft are hardened to 58RC for extra strength and durability. The speed reducers are all factory-filled with FDA-approved polyglycol synthetic lubricant for enhanced rating and reduced thermal rise.
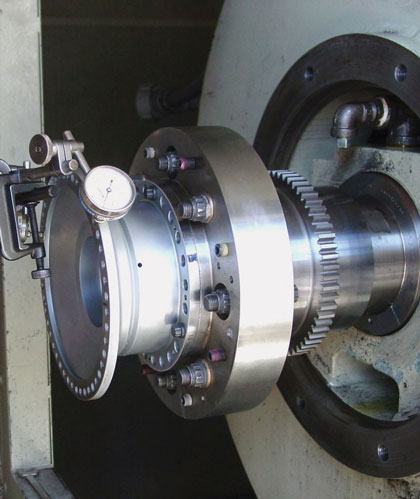
KOP-FLEX HIGH-SPEED SHEAR SPACER COUPLING
Developed to protect gas-turbine-powered generator drives during electrical faults, the Kop-Flex high-speed shear spacer coupling uses a patented double-tube design, precision machining and bearings, and special metal treatments to help provide predictable shear during torque overloads on turbo drivetrains, allowing safe coast down of systems turning at up to 20,000 revolutions per minute. The shear spacer is also ideal for drives on compressors, pumps, fans and trains subject to shock torques. The patented shear cartridge uses special bearings between two tubes to maintain concentricity and overall centering after high-speed separation. The double-bearing design, precision grooving, shot peening and a corrosion resistant coating combine to increase fatigue resistance and promote reliable operation over the life of the coupling. The high-speed shear spacers are available in all catalog coupling sizes capable of handling speeds up to 20,000 revolutions per minute and millions of inch-pounds (or Newton-meters) of torque.
TAKING THE HEAT (AND MORE)
The high-speed shear spacer is an improvement over standard shear spacers and shear pins, which can create issues when used above 3600 revolutions per minute due to balancing issues and fretting potential when using pins.
“Standard shear spacers are not engineered to survive the unbalance forces that develop when turbo drivetrains hit a torque overload at high speeds (3,600-20,000 revolutions per minute),” says Joe Corcoran, manager of global services and training for Emerson’s Kop-Flex coupling business. “Coast down from high speed can be unpredictable with a standard shear spacer, and more damage can result.
“This design takes the standard shear spacer concept to a whole new level of technology,” says Corcoran. “We start with a comprehensive understanding of the material properties of each unique unit, and use metal treatments, testing, precision machining and special bearings to create a custom shear spacer for each application.”
During manufacture, the spacer’s parts are heat-treated with a sample from the same metal batch. Samples are tested to determine exact shear strength, and test data is used to design and machine a precision shear groove on the spacer. Polishing the surface minimizes stress concentrations, and shot peening compresses the surface layer to minimize chances of crack growth. A special corrosion resistant coating is also available to further stabilize the surface.
“Our tests show we’re able to predict the static shearing force within 1.5 percent on a finished unit, and we have successfully run these cartridges at high speeds after separation to validate they can provide ample time for equipment coast down,” adds Corcoran. Many units have been in the field for years and are operating with great success.
ABOUT THE AUTHOR
DeWayne Polley is the gearing product specialist for Emerson Industrial Automation, Power Transmission Solutions. He can be reached at dewayne.polley@emerson.com or 606.564.2267. For more information, visit www.powertransmissionsolutions.com.
_______________________________________________________________________
MODERN PUMPING TODAY, January 2014
Did you enjoy this article?
Subscribe to the FREE Digital Edition of Modern Pumping Today Magazine!
