When forging seamless rolled rings for the power and energy industries, it is crucial to tailor components for their specific applications, or “end use.” In the realm of metal parts, this term commonly denotes the ultimate form and state of the final machined part, along with a comprehension of the operating conditions it will face during service.
“By understanding the final application or purpose–the end use–for which these parts are designed and manufactured, forged parts suppliers can determine the appropriate materials, manufacturing processes, and quality standards necessary to ensure that the metal parts perform effectively and reliably in their intended applications,” says Jeff Klein, director of sales for All Metals & Forge Group. The ISO 9001:2015 and AS9100D-certified manufacturer produces open die forgings, seamless and contoured rolled rings, and complex forged parts to industry standard specifications in eight to ten weeks.
CRITICAL FOR POWER GENERATION
According to Klein, open die and forgings and seamless rolled rings play a crucial role as components in the power and energy sector for a wide variety of end uses. In this industry, forged shapes and seamless rolled rings are crucial for turbines and other power generation machinery as well as hydraulic applications including gears, shafts, hubs, and flanges. As such, these items must exhibit exceptional attributes such as strength, durability, precision, and resistance to fatigue, deformation, and harsh environments in saltwater or downhole uses to meet precise performance standards when deployed in the field.
In some cases, failing to consider the end use can even introduce serious risk, including catastrophic failure of a part while in operation, resulting in safety hazards as well as very costly production downtime when essential replacement parts are not readily available.
CONSIDER END USE, FROM THE START
The consideration and planning to meet end use requirements should begin with the service requirements outlined during the engineering phase of design and conclude when the part is in its operating position, performing as intended.
“It is vital that the manufacturer specify the end use of each part and ensure it is communicated throughout the production chain, from the design engineer, through purchasing, the forging operation, heat treating, finish machining, and final assembly of the end use, including the mechanical property requirements and the heat or corrosive conditions in which the forged part will perform,” says Klein.
According to Klein, the power and energy industries have unique specifications and standards that metal parts must meet. The specific function of the part will dictate its design, dimensions, material selection, forging, heat treating and finishing processes. In all cases, the part must be manufactured to industry standard specifications such as ASTM or AISI unless the OEM has developed their own requirements by modifying one of those standards. In short, the finished product must comply with all quality, durability, chemistry, and mechanical properties within the selected standard.
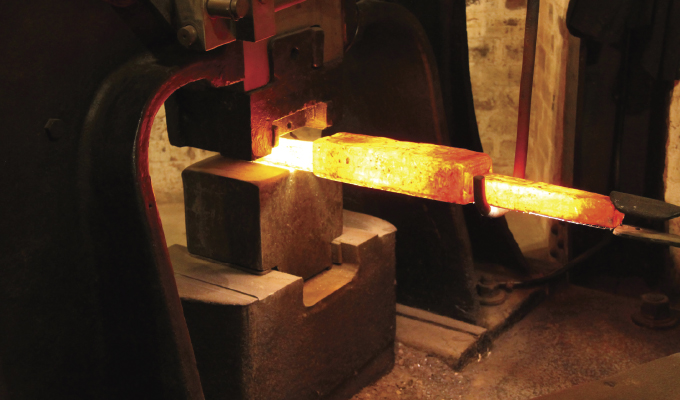
MAKING THE RIGHT CHOICES
Seamless rolled rings can be produced in a variety of alloys, sizes, and shapes specific to fit end use requirements. However, by collaborating closely with the forging supplier, engineers, buyers, and machinery builders can ensure the ideal selection of chemistry, mechanical properties, heat treatment, machining, and testing ultimately required for each part’s end use.
The process often begins with the selection of the alloy grade used in for open die forging or seamless rolled ring production, which can apply to many specific uses. These range from low and medium carbon steels, through high-carbon steels, aluminum alloys, alloy steels, stainless steels, nickel alloys, tool steels and titanium alloys. The precise alloy for the intended end use should always be specified and stated in the purchasing process according to final mechanical property requirements and service conditions.
Material properties can also be altered for specific end uses by hot working as well as by using various chemistries, temperatures, heat treatment times, and cooling methods. This facilitates the production of seamless rolled rings or forged parts with optimized mechanical properties and structural integrity before the part moves on to finish machining.
Each metal possesses unique alloy chemical compositions formed during the steel mill process, along with diverse production procedures for generating ingots or billets of different grades and purities tailored for industry specifications. Consequently, the quality of steel mill output is critical.
MATERIALS MATTER
In the case of All Metals & Forge Group, end use is emphasized from the very beginning in the request for quote (RFQ) process. The company works with its steel mills to purchase the correct starting stock to achieve the specified properties and operating reliability required of every part. In addition, rough machined parts are tested at least three times to prove chemistry, mechanical properties, and soundness before shipping.
According to Klein, there are groups of alloys within each metal material that lend themselves to specific end uses.
High-nickel alloys (I625, I718, I825), for example, are used at high temperatures in such applications as nuclear power generation, where high oxidation resistance is required.
The Inconel 600 and 700 series were developed for specific end uses. Inconel 600 resists chloride-ion stress corrosion cracking. Inconel 690 resists sulfur-bearing gases. Inconel 718 is a precipitation-hardening alloy designed to give very high yield, ultimate tensile strengths, and resistance to creep rupture at temperatures up to 1,300 degrees Fahrenheit (705 degrees Celsius).
End use is equally important with stainless steels, where the various groups of martensitic (hardenable), ferritic, and austenitic cover a very wide range of properties and applications when resistance to corrosion and heat are critical.
Basic type 410 martensitic grade stainless, with around 13 percent chromium, is sufficient for mild corrosive conditions, whereas the ferritic type 430, with 17 percent chromium shows resistance to more severe environments. The performance of the austenitic stainless steels, based on the 18 percent chromium/10 percent nickel in type 304 is selected for certain end uses when correctly heat treated and not subject to carbide precipitation. The various additions to the base 304, such as molybdenum, improve resistance to pitting corrosion. The resultant molybdenum-containing grades are types 316 and 317, normally supplied in the low-carbon versions, 316L and 317L.
The range of stainless steels continues through types 329 and 2205 duplex alloys–austenite and ferrite–that provide good resistance to pitting and stress corrosion cracking, to precipitation hardening grades such as 13-8Mo, 15-5PH, 15-7Mo and 17-4PH. These latter grades reach high yield and ultimate tensile strengths from a single, low-temperature heat treatment following a solution anneal. This makes these types of stainless steels suitable for challenging applications such as nuclear reactor parts.
PEAK PERFORMANCE FOR EVERY APPLICATION
With so many options available, a thorough grasp of the end use is vital for establishing the correct material, dimensions, and properties needed during forging to guarantee peak performance in the eventual application.
By collaborating with an experienced seamless rolled ring manufacturer that can tailor the forging process to the specific end use, power sector OEMs can ensure their final product meets all the necessary requirements and industry standards for their specific application.
Royce Lowe is a highly qualified troubleshooter when metallurgical failures occur with over thirty years of experience in metallurgy, sales, and marketing of a broad range of carbon and alloy steels, including all stages of their processing. All Metals & Forge Group provides open-die forgings, seamless rolled rings, heat treating, and rough or finish machining for all shapes and sizes, including oversized and complex machined parts. For more information, call 800.600.9290 or visit www.steelforge.com.