By Erik Solfelt, Wilden
Despite their appearance, manufacturing systems are delicate ecosystems that must be kept in tune at all times if they are to operate effectively, efficiently, and safely. Key to ensuring the expected level of operation are the pumps that are used to transfer liquids through the manufacturing process. Therefore, it is imperative that these pumps are able to reliably meet their required demands, but at the same time, each individual pump is a unique beast. This makes monitoring pump performance a critical consideration for facility operators but staying on top of that is often easier said than done, even when the most tightly considered maintenance plans are developed and put in place.
Knowing that, here are some of the common performance-related worries that can keep manufacturing-facility operators tossing and turning at night:
- A pump in a far-off corner of the facility fails without the knowledge of the operator. The result is 1,000 gallons of product (which may or may not be hazardous) spilled on the floor, or a ruined product batch that will costs thousands of dollars to replace. The outcome in either instance is system downtime, along with associated cleanup, repair, maintenance and—in the worst-case scenario—replacement costs.
- An unmonitored pump begins operating abnormally, but this change in performance is not readily recognizable to the operator. The possible negative outcomes from a pump that is operating outside of its optimal range are many. They can range from a ruined product batch to a compromised production process that takes more time and cost to complete to a catastrophic failure.
- A facility with a preventative-maintenance schedule in place still has pumps that malfunction outside of the maintenance-plan window. Preventative-maintenance plans can also be overly conservative, calling, for example, the changing out of diaphragms that still have life in them. The schedules themselves could also be inaccurate or not account for the varying life cycles of different pump styles, increasing the chance of unplanned breakdowns or failures.
In truth, the list of potential pump disruptions and their outcomes is innumerable. Operators must live with the fact that all pumps, no matter their method of design or operation, can (or will) fail at some point, and they must take steps to ensure that those failures are not catastrophic.
AODD IS A-OK
That being said, all pump technologies are different, with varying requirements regarding monitoring, maintenance, repair, and replacement. This leads to the fashioning of different reputations for the various technologies, with the air-operated double-diaphragm (AODD) pump having built a reputation since its invention in 1955 as a reliable, durable, and flexible option for difficult pumping applications.
In many ways, the AODD pump has become a victim of its own success. It’s true that AODD pumps are highly flexible, reliable, and resilient in even the toughest pumping environments; in fact, they are routinely trusted for use in many critical and potentially hazardous applications because of their ability to handle solids, deadhead, self-prime, and run dry.
However, because of its simple method of operation, few moving parts, easy maintenance, and relatively low purchase cost when compared to other pump technologies, the AODD pump has been an afterthought in the development and installation of advanced diagnostics and cloud-based performance monitoring. In reality, many of the same pump-performance concerns—including high cost of downtime, repairs, lost product, and product cleanup—that mark other pump technologies can be managed through the advanced monitoring of AODD pumps.
SEEING INTO THE FUTURE
The science behind the drive to improve the remote diagnostic monitoring of pumping technologies has its roots in what has become known as the Industrial Internet of Things, or IIoT. The IIoT is defined as a network of physical devices, systems, and platforms that use embedded communication technology to share the operational intelligence of industrial machines. It combines data technology and machine learning to bring together sensor data and machine-to-machine communication technologies. This enables the identification of operational inefficiencies sooner and more reliably, creating real-time operational transparency and significant cost savings for the operator.
Specific to AODD pumps—despite their perceived simplicity of operation and maintenance—are a number of component and performance parameters that can be measured via remote diagnostic monitoring technology:
- All AODD pumps have wear parts—diaphragms, balls, ball seats, air distribution system (ADS) components—that can break down or fail over time.
- Diaphragm failures need to be sensed and reported as soon as possible in order to prevent catastrophic product leaks.
- Predicting a diaphragm failure is critical in ensuring that downtime is minimized.
- Identifying the window for a potential failure is critical and can be the difference between total loss of the pump or a less costly repair/replacement operation.
- Excessive dry-run conditions that will compromise the pump’s performance and its overall lifespan.
- Operational impediments such as clogged pipes, air leaks, and closed or faulty valves that can adversely affect the pump’s expected performance.
Anticipating potential failure conditions is not the only benefit of remote diagnostic technology. Since pump performance is likely to change over time, whether by normal wear or through outside system influence, monitoring indicators such as stroke rate or stroke count can be an invaluable tool for the operator. Any variance can be noted and recorded, letting the operator know if a failure may be imminent or if a proactive maintenance check may be needed.
From a big-picture perspective, measuring total pump strokes also allows the operator to better construct and implement a more targeted and robust preventative-maintenance plan. Since each system and installation is different, crafting an effective maintenance plan requires that special and specific attention be paid to a unique set of operational variables.
Things to consider in this area include:
- The age of the AODD pump, along with a history of how long pumps have typically performed in the specific application.
- How long do the diaphragms typically last before failing? Whether it be three, six or nine months, the operator can use past history as a gauge when constructing a maintenance plan.
- What are the typical costs for spare parts? Having a well-documented history of pump and component performance can help streamline spare-part inventory requirements, which helps lower capital costs.
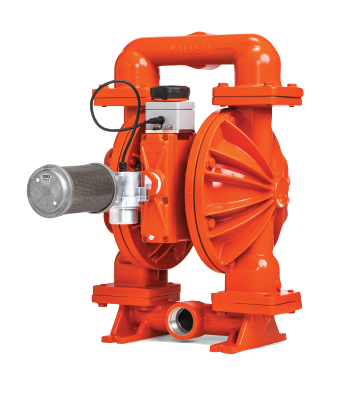
GAINING A DIGITAL EDGE
Until now, the users of AODD pumps only had manual or analog solutions for their pump-monitoring needs—if they even chose to monitor their AODD pumps at all. That, however, is about to change as Wilden® has created a simple diagnostic and monitoring technology for its lines of AODD pumps. Called Wilden SafeGuard™, it allows the AODD pump to be remotely monitored 24/7 via continuous cloud connectivity. Wilden SafeGuard promises to be a true game-changer in optimizing AODD-pump performance, reliability, and cost of operation and maintenance.
Wilden SafeGuard is an all-inclusive pump-monitoring system that tracks, records, and alerts customers to key performance indicators of AODD pumps at all times of operation via cellular access. The SafeGuard system consists of a battery-powered stroke sensor and transmitter (called an Edge device) that is installed on the pump. The sensor collects and analyzes pump-performance data in real-time and transmits it to a central gateway for encryption and transmission to the cloud. Once stored on the cloud, real-time and historic operational information can be accessed by the user anywhere in the world through a secure smartphone app or an online portal.
The design and operation of the SafeGuard system allows for complete monitoring and real-time alerts related to a number of critical performance parameters for the pump (diaphragms, balls, seats). These readings can show the user such things as:
- Leak detection to indicate diaphragm leaks and failures, preventing product loss and safety hazards.
- Stroke rates to monitor changes to highlight performance abnormalities.
- Stroke count for batching and setting maintenance schedules.
- Real-time alerts via SMS or email to indicate any noteworthy change in operation that may be a precursor to pump or component failure.
- Maintenance records that can indicate patterns and help manage preventative maintenance plans.
- Management of an entire fleet of AODD pumps within one dedicated software system.
CONCLUSION
Pump breakdowns and compromised performance, no matter how comprehensive the maintenance schedule, are always possible, making it imperative that the operators of manufacturing facilities know how their pumps have been performing. Advances in digital-monitoring technology and the growth and acceptance of IIoT principles have opened the door for users of AODD pumps to better inform themselves of the capabilities and potential shortcomings of the technology. Recognizing this, Wilden has created SafeGuard, a digital, cloud-based pump-monitoring tool that relies on cutting-edge diagnostics that give AODD pump users the ability to observe exactly how—at any moment in time—their pumps are operating and if any performance-related issues may occur in the foreseeable future.
FOR MORE INFORMATION
Erik Solfelt is the diaphragm pump product manager for Wilden®, a leading manufacturer of air-operated double-diaphragm (AODD) pumps. He can be reached at 909.422.1741 or erik.solfelt@psgdover.com. Wilden is a product brand of PSG®, a Dover company. PSG is comprised of several leading pump companies, including Abaque™, All-Flo, Almatec®, Blackmer®, Ebsray®, Em-tec, EnviroGear®, Griswold®, Hydro Systems, Mouvex®, Neptune™, Quattroflow™, RedScrew™, and Wilden®. For more information, visit www.wildenpump.com or www.psgdover.com.
MODERN PUMPING TODAY, August 2020
Did you enjoy this article?
Subscribe to the FREE Digital Edition of Modern Pumping Today Magazine!
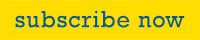