The United States is the third biggest contributor to food waste, throwing away almost one-third of the food it produces. According to Earth.org, 5.9 million glasses of milk, or nearly 20 percent of the total amount produced, is poured down the sink. This makes fresh milk the second most wasted food product in the United States.
One of the most common reasons for America’s food waste habits can be attributed to people misunderstanding expiration date labels. However, consumers are not the only ones responsible for this unsustainable practice, with about 61 percent of all food waste occurring at commercial level, comprising retailers, manufacturers and farmers.
FOOD WASTE AND MILK LAKES
Milk oversupply often means that dairy farmers dispose of milk before it’s even delivered to processors. Though this seems unnecessary and wasteful, it is a complex issue. Cows need to be milked multiple times a day. Simultaneously, defined quotas in the United States and Canada set how much milk a farmer can produce, sell, or distribute. To meet these quotas, dairy farmers will often exceed their production targets. If storage is limited, that’s when waste occurs.
The nation’s largest dairy cooperative, Dairy Farmers of America, estimates that 3.7 million gallons of milk is dumped by U.S. farmers daily, enough to fill six Olympic-sized swimming pools! In Canada, exceeding the province-defined, government-sanctioned quotas results in over 300 million liters of excess milk being dumped annually.
When production continues to outstrip demand, it leads to a surplus of perishable agricultural goods that contribute significantly to our global food waste issue. It is clear that today’s industrial agricultural and food production methods are severely damaging the environment and are not sustainable the growing global population.
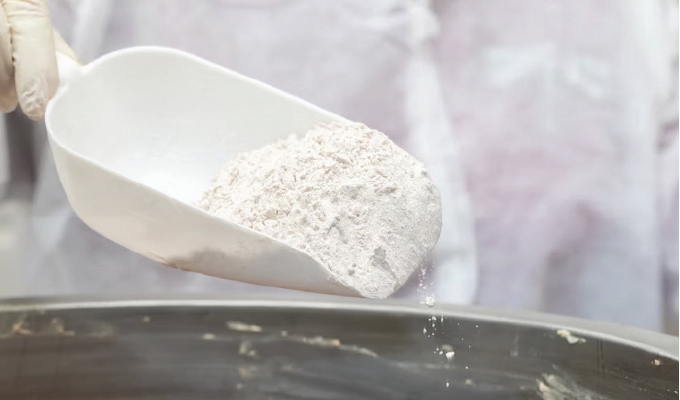
THE EXCESS MILK DILEMMA
Regardless of demand, dairy cows require daily milking. Intervention stockpiling, a concept introduced in the late 1970s, is used by dairy farmers in many economies, including the United States, Canada, and New Zealand. Europe halted the use of quotas over a decade ago. Canada, for example, currently holds an 85,000-kilogram strategic butter reserve. Now, whole milk powder and skimmed milk powder, along with other dairy by-product commodities, are the export frontrunners.
In places like India and Kenya, this process is already being used to mop up excess milk and stabilize prices during glut or deficit. Historically, it has been these regions, who have limited access to fresh milk, that are the main source of milk powder market growth. However, with an escalating demand in pre-prepared foods, baby foods, and infant formula, as well as new vitamin-fortified milk powders entering the market for direct use in beverages, yogurts, coffee, and tea whitener, milk powders have seen a significant rise in popularity worldwide.
The global market outlook is strong, with milk powder valued at $34.6 billion in 2023 and predicted to grow annually by 5.6 percent, reaching $57.2 billion by 2032.
GOING GREENER
Sustainable production, processing, transportation, and consumption of dairy products is essential to protecting the planet and achieving sustainability goals. By 2050, the Innovation Center for U.S. Dairy hopes to achieve greenhouse gas (GHG) neutrality in dairy production, optimize water usage, and reduce waste by adopting new production processes.
Aside from decreasing milk dumping, the longer shelf life of milk powders means that less milk is wasted, helping reduce food waste and conserve resources. One of the most significant environmental benefits of milk powders for food manufacturers is its compactness and reduced weight.
Around 60 gallons of fresh milk is needed to produce 1 gallon of non-fat milk powder, meaning about 60 times less space is required to transport the same amount of milk solids in powder form. Additionally, utilizing milk powders in place of fresh milk eradicates the requirement for cold storage. By transporting milk product more efficiently, using less fuel and producing fewer emissions, food manufacturers can reduce their carbon footprint and help to mitigate climate change.
PROTECTING THE ENVIRONMENT
Adopting more environmentally friendly methods of dairy production can aid the mission to a greener future. In New Zealand, new technology has been employed to reuse water from the condensation process involved in the production of milk powder. The “reclaimed” water system is expected to save half a million liters of groundwater daily.
Additionally, one of the most sustainable methods of reducing waste is implementing inspection technology into milk powder production lines. Metal detection, X-ray, and checkweighing systems help dairy processors address critical waste, sourcing, and sustainability challenges by targeting operational inefficiencies, including upstream product giveaway, non-conforming food packs, and packaging and contamination issues.
The world’s largest producer of WMP located in New Zealand recently updated fifty-six of their Fortress metal detectors to Stealth technology. By adding data logging capabilities and new software algorithms, this processor increased the stainless-steel detection sensitivity to 2 millimeters.
“The cycle of parts breaking down, being thrown away and then having to be replaced is not just wasteful, it’s also unsustainable long term,” cautions Steve Gidman, founder and president of Fortress Technology. The ability to upgrade existing inspection equipment, designed with modularity and scalability in mind, contributes to a more sustainable industry.
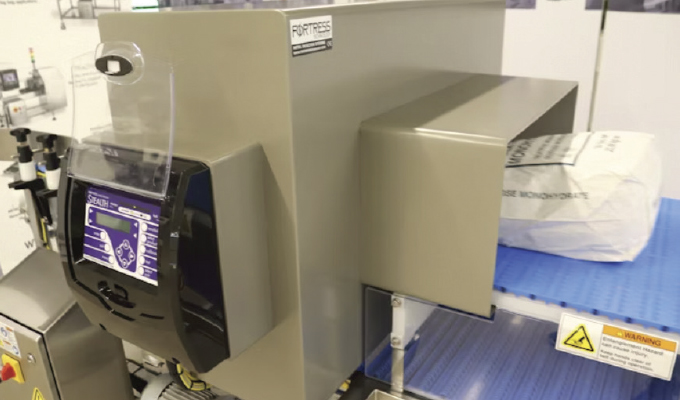
MAINTAINING SUSTAINABLE FOOD SAFETY
With the global milk powder market set to increase in value dramatically over the next ten years, and with dairy farms targeting optimized productivity, further waste reduction efforts are not just necessary but imperative.
Industrialization of farming practices combined with the rapid expansion of the global population, and its subsequent demands, has intensified the production of food and food safety pressures. As the world’s largest manufacturer and exporter of WMP and SMP, with their dairy farming predominantly pasture-based and underpinned by an ambitious “green revolution,” New Zealand provides a strong model of sustainable, safe food processing.
Fortress aims to leverage this localized processing knowledge and best practices to respond to evolving food trends and the overarching need for sustainable production processes.
Fortress Technology produces customized inspection equipment with superior product design and engineering. Our product lineup includes metal detectors, checkweighers, and combination systems designed with a Never Obsolete Commitment. We offer exceptional customer support, parts, software upgrades, and a global service team available throughout the product’s life-cycle. We prioritize customer needs and offer a full refund if products fail to perform as anticipated, demonstrating our confidence in our work. For more information, visit www.fortresstechnology.com.