Miss part 2? Read it here.
Over the first two parts of this series, we have illustrated how combined cycle power producer, or CCPP, operating models have changed to accommodate a rise in renewables, thus bringing about the inclusion of ancillary services. Below, we walk through some of the improvement opportunities that operators are already incorporating. Making the most of this transition leads CCPPs to increased power outputs and operating efficiencies, faster starts and shutdowns, improved load ramp gradient, low-load operation, and expanded operating ranges.
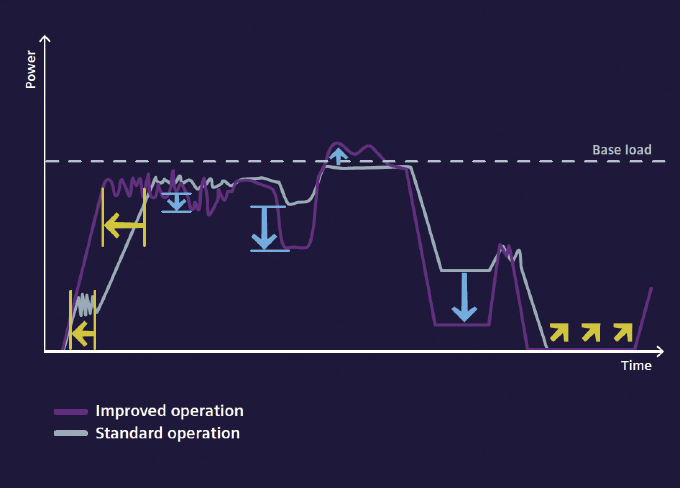
FAST, FLEXIBLE OPERATIONAL CONCEPTS
As illustrated in figure 6, these improvement opportunities include increased power outputs and operating efficiencies, faster starts and shutdowns, improved load ramp gradient, low-load operation, and expanded operating ranges.
These advanced flexible operational concepts could potentially result in faster dispatch times, reduced fuel consumption, and lower carbon emissions, while also enhancing the capability of CCPP operators to help maintain emission targets for both nitrous oxide and carbon. These strategies have been successfully implemented by Siemens Energy in combined cycle power plants around the world, particularly in Europe. Most of these concepts can be implement ed via logic upgrades to the CCPP’s control software while some may require modifications to plant and auxiliary equipment.
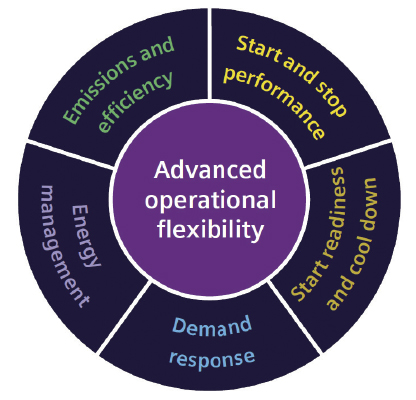
OPERATIONAL FLEXIBILITY IMPROVEMENT CONCEPTS
The transition from a CCPP base load operating model to a cycling operating model requires producers to consistently achieve fast, efficient, and reliable start-ups of their generating assets regardless of how long those assets have been offline. For this paper, hot, warm, and cold starts can be defined as follows:
- Hot start: Up to eight hours post-shutdown.
- Warm start: Between eight and forty-eight hours post-shutdown.
- Cold start: Between forty-eight hours post- shutdown and up to two weeks post-shutdown.
One core start-up improvement concept, for example, involves the parallel ramping of both gas and steam turbines. Consider the scenario of an overnight shutdown of a CCPP. The next day, parallel ramping may help reduce start-up times to approximately thirty minutes in some cases.
A Low Load Turn Down concept can help reduce the minimum part-load capability of the gas turbine. This can assist CCPP operators who seek to enhance the operating flexibility of their gas turbines even further, potentially improving response times to grid demands and enabling combined cycle applications where part-load efficiency is desired. For example, when applied to an SGT6-5000F gas turbine, this concept may optimize and extend the part-load operation range by as much as 40 percent.
PLANT OPTIMIZATION FOR HOT STARTS HELPS CUT START-UP TIMES IN HALF
Plant start optimization for hot starts can help reduce CCPP hot and warm start times. Although most CCPPs were originally built as base load facilities, they now must often operate as peak load plants or cycling plants with frequent start-ups due to changing market conditions and fuel prices. This challenges their operators to achieve fast and predictable start-up times while maintaining high dispatch capability and in- market availability. By implementing this flexibility optimization concept CCPP operators can potentially reduce the cost of each hot start and further reduce carbon emissions. Additionally, with an improved start-up time producers can potentially generate additional revenue in times of high electricity prices.
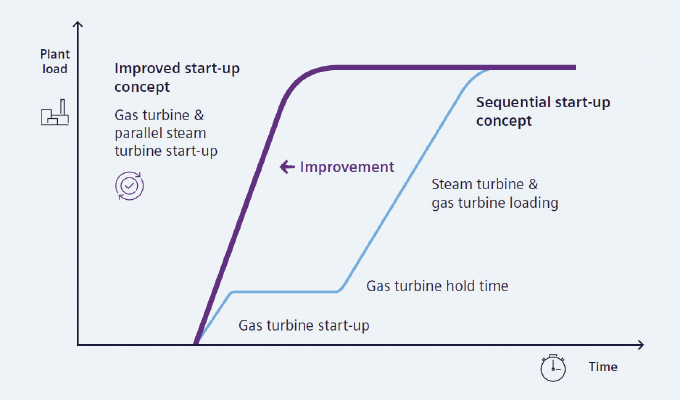
The limitations affecting load output include pressure and temperature transients in the steam turbine, waiting times for establishing required steam chemistry conditions, and warm-up times for the steam turbine, balance of plant, and main piping systems.
One key modification is a start-up on the fly process for the CCPP’s steam turbine. During this process, the turbine is rolled off with the very first “cold” steam produced in the heat recovery steam generator (HRSG), using full pressure and temperature transients. As a result, a start-up time of less than 50 percent may be possible for a CCPP after an overnight shutdown
Figure 8 illustrates the potential improvement a parallel gas and steam turbine start-up process can provide compared to starting them sequentially. This procedure is a highly integrated orchestration of the gas and steam turbine and HRSG operations.
PLANT OPTIMIZATION FOR WARM STARTS: FASTER START-UPS, LOWER FUEL COSTS
Plant start optimization for warm starts uses many hot-start techniques to help reduce CCPP start-up times by up to 50 percent when the plant block is still warm. For instance, if the start-up time of a warm start at a SGT6-5000F GT can be reduced by 50 minutes, a CCPP operator can use the warm-start concept to potentially cut start-up fuel consumption by more than 800 MMBtus, saving fuel costs and potentially avoiding associated emissions of up to 44 tons of carbon per warm start. The savings depend on the size and temperature of the gas turbine and can potentially increase responsiveness to transmission demand signals from ISOs /RTOs.
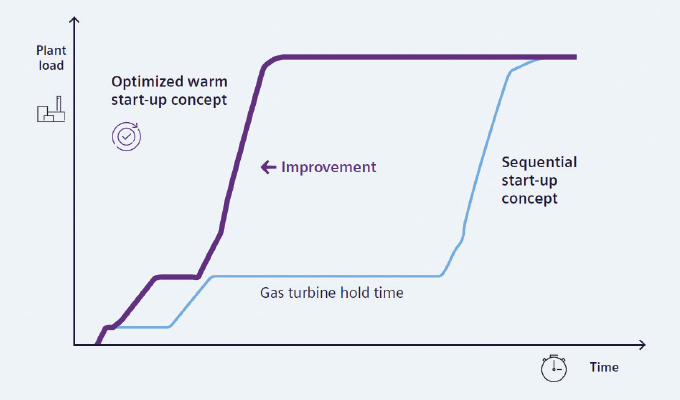
Figure 9 illustrates how the plant-start optimization concept can substantially improve CCPP start-up efficiency. This can significantly reduce combined cycle warm start-up times, in some cases to less than sixty minutes. The potential for time reductions and efficiency improvements during start-ups can be fully tapped by implementing a fast start-up load gradient of up to 30MW per minute, although this load gradient can vary across different gas turbine frames.
PLANT OPTIMIZATION FOR COLD STARTS: MORE EFFICIENCY, LESS TIME TO LOADING CONDITIONS
The ability to start-up a CCPP’s turbine block much faster from longer shutdowns can make a difference in dispatch in competitive markets. During extended offline periods of several days or longer, the steam cycle will cool down, especially its high and intermediate pressure steam turbines.
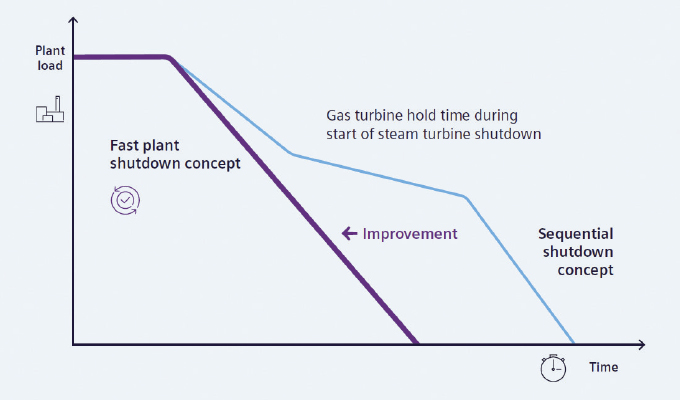
Implementing a steam turbine hot standby method, such as using electrical heating blankets, to either prevent or limit this cooling can shorten start-up times during a shutdown phase of up to two weeks. If the plant was built without a gas-fired auxiliary steam boiler, an electrical auxiliary steam generator can be retrofitted. The electrical auxiliary steam generator’s objective is to provide enough steam to seal the steam turbine and create a vacuum in the condenser before the gas turbine starts.
This helps allow early steam condenser bypass operation and helps avoid long low load operation times with the HRSG venting valves. Keeping the steam turbine sealed and under vacuum also helps prevent air ingress, improve the feedwater quality, and minimize water-chemistry related hold times during the start. This concept is intended to help (1) increase responsiveness to transmission ISO / RTO demand signals, (2) shorten start-up time, in some cases up to 50 percent, and (3) boost efficiency in the start-up process.
In addition, the degassed conductivity concept may shorten the start-up time of a combined cycle power plant—especially for cold starts as the waiting time for steam purity may be significantly reduced. This method controls the steam purity and distinguishes between the corrosive contaminants and less harmful carbon by re-boiling the sample downstream from the cation column to remove carbon.
FAST PLANT SHUTDOWN OPTIMIZATION: SAVING FUEL, LOWERING CARBON OUTPUT
CCPP shutdowns can require considerable time and fuel for conducting the necessary unloading processes. In competitive markets, the ability to shut down a plant faster can help reduce time spent in transient conditions with non-optimal efficiencies and enhance responsiveness.
The fast plant shutdown concept was developed to significantly shorten a CCPP’s shutdown time, in some cases to less than thirty minutes. As shown in figure 10, the concept leads to less fuel consumption and potential improvements to both operating costs and profitability.
SUMMARY: FLEXIBILITY WITH SPEED AND RELIABILITY
In the past decade, the operating profiles of CCPPs have significantly shifted due to the growth in renewables in producers’ energy resource mix as well as volatile fuel prices and governmental legislation. The impact of these trends on the current and future operations and profitability of typical CCPPs necessitate a shift from outdated base load to cyclical operation.
CCPP flexibility and responsiveness to market signals are critical to sustainable margins and profits. To help achieve these capabilities and prepare their CCPPs for current and upcoming market conditions, operators can implement fast start-up concepts across hot, warm, and cold turbine conditions along with fast shutdowns and load gradient improvements to potentially improve their competitiveness, asset utilization, and profitability.
Located in ninety countries, Siemens Energy operates across the whole energy landscape—from conventional to renewable power, from grid technology to storage to electrifying complex industrial processes. For more than 150 years our engineers have been spearheading the electrification of the world. Today, we are a team of 99.000 sharing the same passion, vision, and values. Our diversity makes us strong and helps us to find answers together with our partners. For more information, visit www.siemens-energy.com.