By Soren Rasmussen, Landia
Gazing across at the view in Seabrook of yachts, wild birds, and palm trees in the welcome breeze, it takes the start-up of a small submersible mixer to bring one back to reality that you’re actually at a site that is handling sewage.
Here in sunny Seabrook, just thirty minutes south of the mass of Houston, Texas, this small town on Galveston Bay can rightly boast one of the world’s most pleasant wastewater treatment centers—a facility that has also proved it pays to plan ahead through clever design. For example, when the Category 4 Hurricane Harvey devastated much of the low-lying grounds in southeast Texas, remarkably Seabrook WWTP kept operating, since the electrical controls were all mounted above the high-water mark in anticipation that one day flood waters would infiltrate the plant.
The submersible mixer in question plays a key role in Seabrook WWTP being a good neighbor, especially with so many waterfront properties close by in the vibrant yet relaxed area that feels more like a resort-style experience.
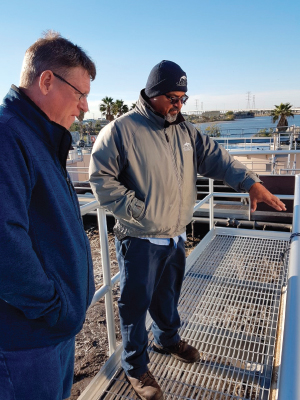
HELPING TO CONTROL ODORS
As Seabrook’s site superintendent, Rafael Gonzales explains, the submersible mixer from Landia is doing its important job in helping to control odors.
“When the air has been turned off in our digester for the dewatering process,” he says, “we use a Landia gear-driven mixer for several hours to slowly mix everything back up without creating unnecessary odors. This is very important when the digester is thick—and also depends on how long we’ve been waiting for the dewatering contractor to arrive. Sometimes the sludge has been sitting there longer than we would have liked.”
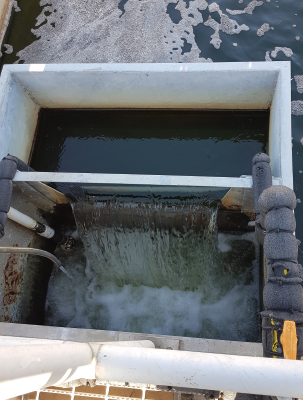
He adds, “We’re at the mercy of the dewatering process every three to four weeks, because as is the case with most deliveries and collections, the sludge haulers want to do everything as fast as possible. This puts us under pressure. We may not have to run our belt process, but we do have to be very aware of odors escaping.”
Located just a ten-minute car drive from NASA’s Johnson Space Center, the mixing process at Seabrook’s two-million-gallons-per-day plant had become complicated and at times labor-intensive until the Landia mixer was installed almost two years ago.
The previous mixer, a direct-drive model, kept tripping out. On six separate occasions, Rafael and his team had to remove it from the water for repairs.
A GOOD, STURDY REPLACEMENT
“Try as we might” continues Rafael, “moisture had gradually crept into the mixer, ultimately leading to a complete burn out, so we needed to find a good, sturdy replacement. We could have asked for another direct-drive mixer, but by discussing our needs with Landia and reviewing the application, their recommendation was that a gear-driven mixer would be much better for us, and so it has proved. We also saved money straight away by them being able to use the existing guiderail for the retrofit. There was no need to drain the tank.”
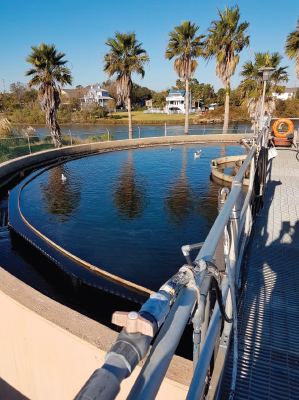
At this 1960’s-built plant, close to the third largest boating center in the United States, the switch from a direct-drive mixer to a gear-driven mixer raises an important, and what could rightly be described as an overlooked “weighty” issue, as Landia’s Art Savage explains, “As a proud manufacturer ourselves of direct-drive mixers, it goes without saying that we’re not against them! However, it is important to select the right mixer for each application. In the case of Seabrook, a gear-driven mixer was more suitable for their sludge tank than the direct-drive mixer (of a different brand) that they had previously been sold. Use of certain direct-drive mixers can become quite costly in operation and repair costs. A direct-drive mixer means the propeller rotates at the same speed as the motor shaft, e.g. up to 1,800 rpm. But at that velocity, a great deal of disruption and damage would be made to the biological process.”
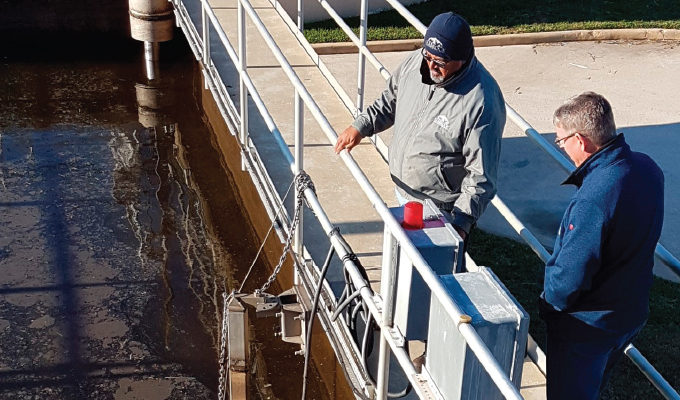
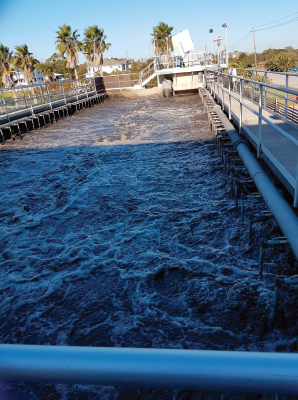
He adds, “So, without the benefit of a gear reducer, you have to slow-down the propeller speed in other ways, which is typically done by increasing the number of poles in the motor. However, this adds a lot of weight—and greatly reduces the motor efficiency. The Landia mixer weighs around 235 pounds, compared to the previous mixer of more than twice that weight, and Seabrook went from a 15- to a 12-horsepower motor with their new mixer. The higher-pole motors are also quite costly to repair, and but manufacturers don’t necessarily volunteer this information. Seabrook had certainly faced some high repair bills with their direct-drive mixer, until it became evident that it was no longer viable to keep rebuilding it.”
A HAPPY RESULT
Rafael Gonzales continues, “We run the Landia gear-driven mixer for an hour to two hours per day with no problems at all—and for its performance and reliability, we can see that it’s just right for the application. The mixing pattern is good, and with an adjustable guide pipe, we can also use it during dewatering to push the solids over in the right direction. We’re very happy with it.”
FOR MORE INFORMATION
Siemens Digital Industries Software, a business unit of Siemens Digital Industries, is a leading global provider of software solutions to drive the digital transformation of industry, creating new opportunities for manufacturers to realize innovation. With headquarters in Plano, Texas, and over 140,000 customers worldwide, we work with companies of all sizes to transform the way ideas come to life, the way products are realized, and the way products and assets in operation are used and understood. For more information, visit www.sw.siemens.com.
Soren Rasmussen is the director of Landia, Inc. For more information about Landia’s range of applications, call 919.466.0603, email info@landiainc.com, or visit www.landiainc.com.
MODERN PUMPING TODAY, September 2019
Did you enjoy this article?
Subscribe to the FREE Digital Edition of Modern Pumping Today Magazine!
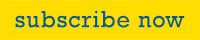